Odlewnictwo metali
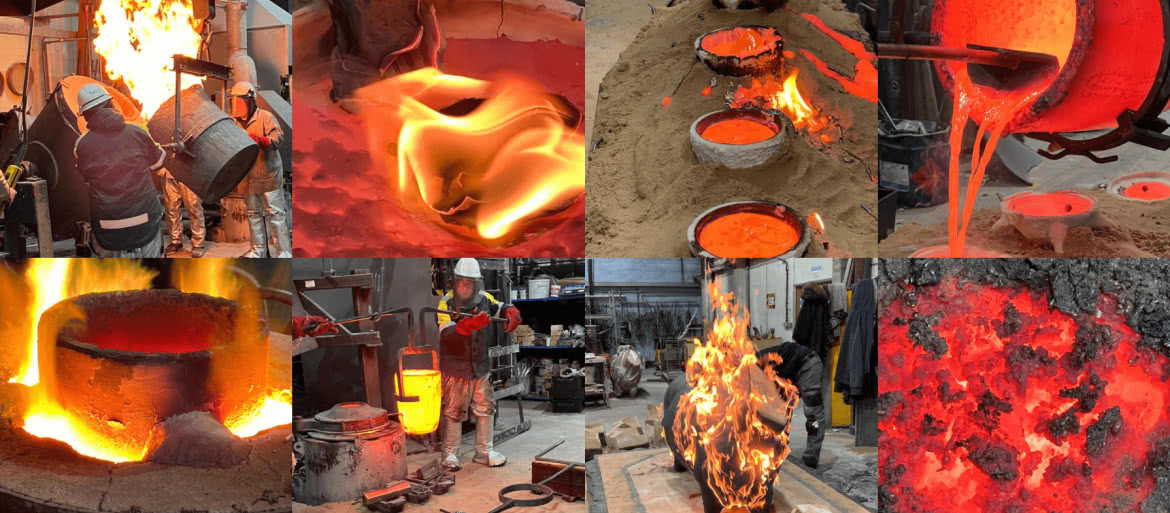
ok. 6000–2000 lat p.n.e. Wyroby ze złota odlewane do form w gruncie. Później zaczęto stosować dzielone formy z kamienia wapiennego lub gliny, które pozwalały na uzyskanie odlewów o bardziej skomplikowanych kształtach (1). Pojawiająca się z czasem konieczność wytwarzania broni, czy narzędzi z otworami, jak np. siekiery czy topory, zmusiła ludzkość do zastosowania metody wytapianych modeli. Około 2 tysiący lat p.n.e. w Egipcie starożytni rzemieślnicy znali i stosowali już odlewanie metodą traconego wosku.
VII wiek p.n.e. W starożytnych Chinach opanowano odlewanie żeliwa, stopu o wysokiej temperaturze topnienia. Wykonywano z niego przedmioty codziennego użytku, a także często kilkunastometrowej wysokości posągi. Mniej więcej w tym samym okresie pojawiły się tam pierwsze formy piaskowe.
ok. 300 r. p.n.e. Pierwszą formą odlewanej stali tyglowej była tzw. stal wootz (damasceńska), opracowana po raz pierwszy w Indiach. Podczas jej produkcji żelazo dymarkowe było mieszane ze szkłem, a następnie chłodzone. Gdy mieszanina stygła, szkło łączyło się z zanieczyszczeniami w stali a następnie wypływało na powierzchnię, pozostawiając stal znacznie czystszą.
III w. p.n.e. - V w. n.e. Metalowe elementy potrzebne do maszyn i urządzeń technicznych zostały wykonane metodą odlewania po raz pierwszy w starożytnym Rzymie. Były to elementy pomp i wodociągów odlane z brązu. Po upadku Cesarstwa Rzymskiego kunszt odlewniczy zanika i aż do XIV wieku metodą odlewania wykonuje się tylko dzwony, płyty nagrobkowe, drzwi do kościołów oraz drobne ozdoby z metali szlachetnych.
XV–XVI w. Vannoccio Biringuccio (1480–1539), określany jako „ojciec przemysłu odlewniczego”, publikuje „De la Pirotechnia” (2), pierwszym drukowany opis technik i praktyk odlewniczych. Włoch zawarł w swoich dziełach szczegółowe informacje na temat praktyk górniczych, wydobywania i rafinacji wielu metali, stopów stosowanych w odlewniach. Przed publikacją jego książki informacje na temat metalurgii i sztuki wojskowej były ściśle strzeżonymi tajemnicami.
1709 Anglik Abraham Darby jako pierwszy z powodzeniem wytapia rudę żelaza z koksem, zamiast wcześniej stosowanego węgla drzewnego. Jakość żeliwa Darby’ego umożliwiła mu produkcję cienkich odlewów, które mogły z powodzeniem konkurować z mosiądzem w takich zastosowaniach, jak produkcja garnków i innych pustych naczyń.
1740 Tygle do odlewania zaczął stosować Benjamin Huntsman. Były wykonane z gliny. Huntsman zaczął odlewać w nich stal w swoim zakładzie Handsworth w Sheffield. Ten innowacyjny proces odlewniczy oznaczał, że Huntsman mógł produkować stal dla producentów sztućców z Sheffield, które okazały się lepsze od importowanych europejskich sztućców, które do tego czasu dominowały na rynku. Huntsman utrzymywał swój proces produkcji w tajemnicy, ale nie udało mu się go opatentować. Oznaczało to, że inni później go kopiowali, co doprowadziło do szybszego rozprzestrzeniania się i rozwoju odlewni stali.
1754-57 John Wilkinson (4) z Anglii opracowuje innowacyjny, napędzany parą hydrauliczny silnik nadmuchowy do wielkich pieców, który umożliwiał osiąganie wyższych temperatur, zwiększając ich wydajność. Wynajduje również maszynę to toczenia odlewanych cylindrów, takich jak lufy armatnie.
1809 Odlewanie odśrodkowe zostaje opracowane przez A.G. Eckhardta z Soho w Anglii. Odlewanie odśrodkowe (5) jest jednym z niewielu procesów odlewania, który może być stosowany zarówno do produkcji metali, jak i części z tworzyw sztucznych.
1849-1885 Pierwszy patent związany z odlewnictwem ciśnieniowym został przyznany w USA Johnowi I. Sturgisowi w 1849 roku na małą, ręczną maszynę w celu zmechanizowania produkcji czcionek drukarskich (przez wtrysk ołowiu). W 1885 roku Ottmar Mergenthaler wynalazł drukarską automatyczną maszynę odlewniczą o nazwie Linotype, która stała się podstawą do automatycznego odlewania ciśnieniowego, jakie znamy dzisiaj. Linotyp zrewolucjonizował technologię druku (6), jak też samo odlewnictwo.
1867 James Nasmythe opracowuje kadzie odlewnicze z przekładnią zębatą, zwiększając bezpieczeństwo pracowników i ekonomię pracy. Dzięki temu wynalazkowi wystarczał jeden człowiek, zamiast kilkunastoosobowej grupy, co pozwalało wylewać stopioną zawartość łatwiej i bezpieczniej. W ten sposób zapewniono lepszą jakość odlewu dzięki stałemu, ciągłemu przepływowi rozgrzanego do białości metalu do formy.
1869 Benjamin Chew Tilghman wynalazł proces piaskowania z wykorzystaniem podmuchu powietrza do czyszczenia odlewanych obiektów i złożył patent w USA.
1876 Pułkownik William Frishmuth wyprodukował w swojej filadelfijskiej odlewni pierwsze potwierdzone odlewy aluminiowe.
1898 Firma Hargraves (Wielka Brytania) produkuje pierwsze formy piaskowe spajane krzemianem sodu.
1906-13 Pierwszy elektryczny piec łukowy zostaje uruchomiony w USA w Holcomb Steel Co. w Syracuse w amerykańskim stanie Nowy Jork. Siedem lat później technika pieca łukowego zostaje zastosowana do odlewnictwa przez Crucible Steel Casting Co. w Lansdown w stanie Pensylwania.
1918 Pierwsza w pełni zautomatyzowana odlewnia w Rockford w stanie Illinois odlewa łuski granatów ręcznych dla armii amerykańskiej.
1943-47 Odlewanie form skorupowych (7), proces opatentowany w Niemczech przez Johannesa Croninga w 1943 roku do produkcji form lub rdzeni został odkryty i rekomendowany przez amerykańskich inżynierów i naukowców po wojnie. Polega on na mieszaniu piasku z żywicą termoutwardzalną. Gdy materiał ten styka się z rozgrzaną metalową płytą modelową, wokół wzornika tworzy się cienka i mocna skorupa formy.
1949 Opracowanie żeliwa sferoidalnego, żeliwa o w pełni sferoidalnej strukturze grafitowej (8). Patent USA przyznany K.D. Millisowi, A.P. Gagnebinowi i N.B. Pillingowi z International Nickel Company za opracowanie żeliwa sferoidalnego. Uzyskuje się je w wyniku sferoidyzowania i następnie modyfikowania ciekłego stopu o małej zawartości siarki, co bez dodatków dałoby żeliwo szare. Jako sferoidyzatorów stosuje się cer lub stopy żelazo–krzem–magnez, natomiast do modyfikacji wykorzystuje się żelazokrzem. Ma dobre własności wytrzymałościowe i ślizgowe. Może ulegać odkształceniu bez uszkodzeń, jest odporne na ściskanie i zginanie oraz na wysokie ciśnienia. Znalazło zastosowanie do wyrobu wałów korbowych, pierścieni tłoków, łożysk, kół zębatych, elementów obrabiarek, maszyn rolniczych, hydraulicznych, turbin wodnych i innych części.
1958 Harold Shroyer uzyskuje patent na proces pełnej formy, prekursora procesu odlewania metodą traconej pianki. Technologia pełnej formy polega na umieszczeniu modelu z polistyrenu spienionego (styropianu) - na którego powierzchnię naniesiona jest powłoka ognioodporna - w skrzynce formierskiej oraz zasypaniu modelu odlewu i układu wlewowego suchym piaskiem kwarcowym. Jest to pierwszy proces, w którym zastosowano masę formierską bez materiału wiążącego. Ciekły metal wlany do formy zgazowuje model styropianowy, odtwarzając go doskonale w postaci odlewu. Gazy powstałe ze zgazowanego modelu przechodzą przez po-włokę ochronną i piasek na zewnątrz formy.
lata 70. XX wieku Japończycy opracowują formowanie w procesie V. Jest to forma odlewania piaskowego, ale w przeciwieństwie do innych procesów piaskowych, które wykorzystują gruboziarnisty piasek utrzymywany w kształcie za pomocą spoiwa, proces V wykorzystuje bardzo drobny, suchy piasek i nie zawiera spoiw. Piasek jest utrzymywany w formie poprzez próżniowe pakowanie piasku (V to skrót od ang. słowa „vacuum”, czyli próżnia) między arkuszami cienkiej folii z tworzywa sztucznego. Próżnia powoduje, że piasek staje się twardy, podobnie jak próżniowo zapakowana kawa. Wzór jest usuwany, a do wnęki wlewany jest metal. Próżnia jest uwalniana, a odlew usuwany.
przełom lat 70./80. XX wieku Rozwój technik projektowania wspomaganego komputerowo (CAD) i produkcji wspomaganej komputerowo (CAM), które znajdują zastosowanie w odlewnictwie (9). Pionierem w tej dziedzinie jeszcze w latach 70. była firma Computervision, a w ślad za nią szła firma IBM.
1993 Pierwsze odlewnicze zastosowanie plazmowej rafinacji kadziowej (topienie i rafinacja w jednym zbiorniku) w Maynard Steel Casting Company w Milwaukee.
1997 Proces odlewania z mieszaniem elektromagnetycznym opracowany przez Argonne i Inland Steel Corporation. Mieszanie elektromagnetyczne w procesie odlewania stali polega na wywołaniu ruchu ciekłego metalu wewnątrz wlewka, za pomocą zmiennego pola elektromagnetycznego. Efektem jest wyraźny wzrost jakości odlewanego wlewka oraz poprawa warunków oddawania ciepła przegrzania z fazy ciekłej do naskórka, pod warunkiem że parametry pracy mieszadła będą dostosowane do wymiarów przekroju poprzecznego wlewka, prędkości odlewania i gatunku odlewanej stali. Elektromagnetyczne ograniczanie krawędzi znacznie zmniejsza koszty i wydatki na energię.
Klasyfikacja technik odlewniczych
Odlewnictwo to technika (niekiedy sztuka lub umiejętność) polegająca na wykonywaniu produktów przez zalewanie uprzednio przygotowanej formy ciekłym materiałem, najczęściej stopem metali, ale również gipsem, woskiem czy tworzywami sztucznymi. Do sztuki odlewniczej należy również takie sterowanie procesem krzepnięcia lub reakcji chemicznej tężenia odlewu, aby otrzymać wyrób o odpowiedniej strukturze i właściwościach. Do odlewnictwa zalicza się także techniki przygotowania form odlewniczych (formierstwo) oraz obróbki odlanych obiektów.
1. Do podstawowych technik odlewnictwa metali, w których duża dokładność wymiarów nie jest wymagana, zalicza się:
- Odlewanie grawitacyjne, w którym formy wypełniają się roztopionym metalem przez zwykłe ich zalewanie pod wpływem siły ciążenia.
- Odlewanie w formach z mas samoutwardzalnych, stosowane głównie do dużych odlewów.
- Odlewanie do form piaskowych, tworzonych ręcznie lub za pomocą prostych maszyn takich jak prasy.
2. Metody odlewnicze o podwyższonej dokładności wymiarowej to:
- Odlewanie do form z mas piaskowych pod wpływem wysokich nacisków. Stosowane w nim metody to formowanie próżniowo-pulsujące, formowanie impulsowe oraz nadmuchiwanie. Używane materiały formierskie to masa piaskowa ze spoinami żywicznymi, masa piaskowo-bentonitowa, masa piaskowa ze szkłem wodnym. Materiały utwardzane są dwutlenkiem węgla.
- Odlewanie odśrodkowe. Jest to metoda wytwarzania odlewów o kształtach obrotowych. Stosuje się w nim metalowe formy wirujące, wypełniane roztopionym metalem pod wpływem siły odśrodkowej.
- Odlewanie odśrodkowe w formach precyzyjnych.
- Odlewanie ciągłe i odlewanie półciągłe rur i prętów. Formy odlewnicze stanowią w nim krystalizatory. Można za jego pomocą odlewać rury i pręty o różnych profilach, uzyskując pożądane kształty wyrobów takich jak profile, pręty, rury i wylewki. Roztopiony metal wlewa się do krystalizatora w sposób ciągły, z którego wyjmuje się go następnie w sposób ciągły lub skokowy.
3. Metody odlewnicze o dużej dokładności, stosowane w przypadku bardziej kosztownych i zaawansowanych materiałów (np. stopy tytanu). Wyróżnia się wśród nich m.in.:
- Metodę modeli wytapianych, która umożliwia stworzenie odlewów o szczególnie gładkiej powierzchni i precyzyjnych wymiarach. Stosuje się w niej modele wykonane z wosku syntetycznego o wysokiej topliwości lub innego materiału łatwo topliwego, przeznaczone do jednorazowego użytku. Model taki pokrywany jest masą ceramiczną, która po stwardnieniu tworzy formę odlewniczą o dużej wytrzymałości. Następnie pozostały wosk wytapia się.
- Metodę pełnej formy. Stosuje się styropian. Modele te podczas zalewania formy płynnym metalem są wytapiane.
- Odlewanie w formach piaskowych, powlekanych syntetyczną żywicą termoutwardzalną. Po nagrzaniu forma taka uzyskuje postać skorupy.
- Odlewanie próżniowe.
- Odlewanie przy obniżonym ciśnieniu.
- Odlewanie do form metalowych z wykorzystaniem ciśnienia. Stosowane są tu kokile (formy wielokrotnego użytku). Odlewanie ciśnieniowe polega na wtłaczaniu roztopionego metalu do stalowych form pod wysokim ciśnieniem, stosując sprężone powietrze lub tłoki. Pozwala ono uzyskać wysokiej jakości odlewy o złożonych kształtach (głównie z aluminium, miedzi i cynku).
M.U.