"Drukujący" przemysł motoryzacyjny. Oszczędności i śmiałe wizje
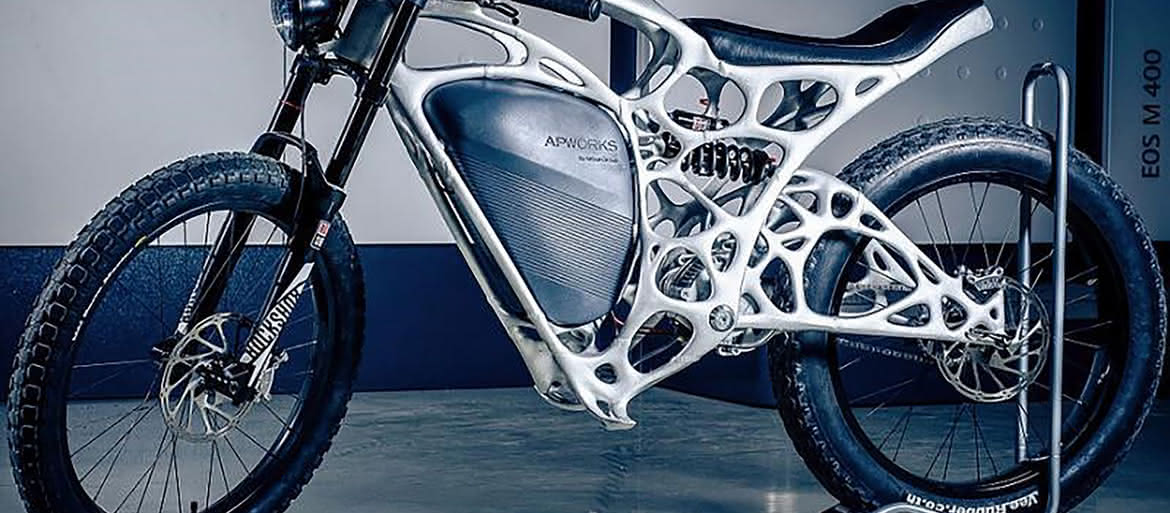
Wewnętrzna struktura Vision przypomina gąbkę - w środku jest twarda, na zewnątrz elastyczna. Koło to nigdy nie złapie gumy. Bieżnik można odnawiać, a stacje do druku 3D potrafią ponoć zastąpić go nowym z pomocą minimalnej ilości gumy. Wzory bieżnika można również łatwo zmieniać, dopasowując je do warunków jazdy, i to bez konieczności zdejmowania koła z pojazdu. Ze względu na naturalne składniki Vision nadaje się też doskonale do recyklingu.
Części i narzędzia
Jeśli takie wejście druku 3D do motoryzacji jak koncept Vision wydaje nam się zbyt futurystyczne i jeszcze mało realne, to popatrzmy na inne, bliższe rzeczywistości przykłady. Choćby ten, w którym Volvo, dzięki drukowi 3D, skróciło czas oczekiwania na zestaw metalowych narzędzi do montowania modeli samochodów aż o 94%, co znacząco obniżyło koszty. Fordowi druk 3D posłużył do skrócenia czasu prototypowania Forda Mustanga aż 30-krotnie i obniżenia kosztów 166-krotnie. Inne modele z warsztatu amerykańskiego producenta kryją już pod maską drukowane części. Opel korzysta z drukowanych narzędzi na linii montażowej, twierdząc że koszt ich produkcji zmniejszył się dzięki temu o 90%, a masa o 70%, jednocześnie nie wpływając na właściwości wytrzymałościowe.
Mercedes Benz Trucks przedstawił niedawno pierwsze części zamienne do swoich samochodów ciężarowych wykonane przy użyciu profesjonalnych maszyn, pracujących w technologii selektywnego laserowego spiekania proszków metalowych. Przykładem jest pokrywa termostatu do pojazdów ciężarowych. Element przeszedł pomyślnie testy wytrzymałościowe, a sam proces wytwarzania pozwala na znaczną oszczędność materiału w stosunku do metod tradycyjnych. Niewykorzystany w procesie druku 3D proszek aluminiowy zostaje poddany oczyszczaniu, a następnie wykorzystany ponownie.
Technologia laserowego spiekania proszków metalowych w niedługim czasie może zostać wprowadzona do produkcji innych części zapasowych - wśród nich wymieniane są zewnętrzne elementy silnika, układu chłodzenia, skrzyni biegów czy podwozia. Metoda otrzymywania elementów na podstawie wirtualnego modelu ma szansę okazać się szczególnie cenna w przypadku części zamiennych dla starszych, wycofanych z produkcji wersji samochodów. Zgromadzenie modeli przestrzennych każdego elementu zamiennego w dużej, łatwo dostępnej cyfrowej bazie danych i wytwarzanie ich dzięki technikom addytywnym może znacząco obniżyć koszty, związane z magazynowaniem i wysyłką części. Technologie addytywne dają możliwość modyfikacji klasycznego łańcucha dostaw części zamiennych na życzenie klienta.
Volkswagen w swojej fabryce korzysta z technologii druku 3D z metalu do wytwarzania narzędzi i części samochodowych. Z metalowego proszku, spiekanego za pomocą lasera, wytwarzane są prototypowe części montażowe, np. blokujące pokrywę silnika, oraz elementy, których złożoność kształtu uniemożliwiała dotąd wykonanie ich metodami tradycyjnymi. W listopadzie 2017 r. niemiecki koncern poinformował, że dzięki drukowi 3D jedna z fabryk Volkswagena zmniejszyła koszty narzędzi dziesięciokrotnie. Cena przyrządu do zabezpieczenia felg w czasie montażu kół spadła z 800 do 21 euro.
Zakup kilku drukarek 3D kosztujących w sumie tyle co nowy VW Beetle pozwolił portugalskiej fabryce Volkswagena oszczędzić setki tysięcy euro na własnej produkcji narzędzi i osprzętu zamawianego wcześniej u zewnętrznych dostawców. Inwestycja zwróciła się w dwa miesiące. Redukcja kosztów wytwarzania narzędzi sięgnęła 91%. Oszczędność czasu projektowania i testowania wszystkich drukowanych elementów doszła nawet do 95%.
W 3D drukowane są proste przyrządy wykorzystywane na linii produkcyjnej jako pomoce w procesie montażu. Ich zadania to zwiększenie kontroli nad tym procesem przez zapobieganie uszkodzeniom czy optymalizację pozycjonowania. Są to np. zasobniki pozwalające na wkładanie od razu wszystkich śrub w montowane koło i chroniące felgi przed uszkodzeniem podczas pracy czy ramki ułatwiające równe naklejenie liter nazwy modelu zawsze w tym samym miejscu klapy bagażnika.
Volkswagen produkuje również przy pomocy technik addytywnych szereg części do swoich aut, np. przekładnie zębate, złączki do silników oraz metalowe elementy do łączenia klamek drzwi z wnętrzami skórzanymi.
Zdaniem Knutha Walczaka, szefa działu innowacji i zarządzania rozwojem Porsche, teoretycznie drukować da się nawet silnie obciążone części, takie jak tłoki.
- Ponieważ materiał układa się warstwa na warstwie, można systematycznie oddziaływać na mikrostrukturę - powiedział w jednym z wywiadów.
Przeważa jednak opinia, że nowa technologia nie zastąpi tradycyjnych procesów. Twierdzi tak m.in. Jörg Spindler, stojący na czele Audi Competence Center, w niemieckim Ingolstadt, oraz wielu innych przedstawicieli branży. Zazwyczaj wszyscy zgadzają się jednak, że techniki addytywne zapewnią w branży motoryzacyjnej nowe, fascynujące możliwości.
Auto z drukarki, przynajmniej częściowo
Części i oprzyrządowanie produkcyjne to rzeczy ważne, ale na opinii publicznej największe wrażenie robią projekty "idące na całość" - czyli pomysły na konstrukcje całych aut w technologii 3D. Na rynku tego rodzaju samochodów jeszcze nie ma, ale mogą pojawić się prędzej, niż myślimy.
Kevin Czinger, prezes zarządu wytwórni Divergent 3D, zaprezentował w listopadzie 2017 r. na konferencji Solid supersamochód Blade, tworzony w większości techniką druku 3D.
Podwozie ważącego ok. 700 kg sportowego wozu zostało zbudowane z części ze stopów metali, które były drukowane w technologii 3D, a nie odlewane. Inne elementy konstrukcji nie są wykonane techniką addytywną, ale łączniki już tak. Elementy łączą się w system modułowy i wraz z rurkami z włókien węglowych tworzą konstrukcję samochodu, porównywaną przez Czingera do budowli z klocków Lego.
Z punktu widzenia ochrony środowiska, dla szefa Divergent 3D nie ma większego znaczenia, czy samochód będzie napędzany silnikiem spalinowym, elektrycznym, wysokoprężnym czy wodorowym ogniwem paliwowym. Metoda napędu ma mniejsze znaczenie niż sam proces produkcji.
- Jeśli chcesz wprowadzać ekologiczne innowacje, musisz znaleźć nowy sposób produkcji, ponieważ tam właśnie decydują się koszty materiałów, energii i kapitału - powiedział Czinger, prezentując swój projekt.
Innowacje Divergent pozwalają w procesie wytwarzania zaoszczędzić właśnie materiały oraz energię. Czinger powiedział, że w całości cyklu produkcyjno-użytkowego Blade pojawia się zaledwie jedna trzecia poziomu emisji typowego dla analogicznego cyklu samochodu elektrycznego.
Ciekawe jest też podejście Divergent 3D do produkcji swojego modelu. Firma wcale nie zamierza zajmować się jego wytwarzaniem. Planuje licencjonowanie projektu z myślą o drobnych wytwórcach, produkujących własne egzemplarze w spersonalizowanych wersjach, w dowolnym miejscu na świecie. Firma opracowała nawet kompletne oprogramowanie o nazwie Divergent Production System, służące do budowy lekkich, metalowych konstrukcji pojazdów wykorzystujących dodatki uszlachetniające.
Drukowany w 3D motocykl Light Rider to z kolei dzieło firmy APWorks, której spółką macierzystą jest Airbus. Dzięki wykorzystanemu w nim stopowi aluminium o nazwie Scalmalloy, masa pojazdu wynosi zaledwie niecałe 40 kg, razem z silnikiem o mocy 6 kW, akumulatorem i częściami mechanicznymi. Sama drukowana w 3D rama waży niewiele ponad 7 kg. Firma rozpoczyna właśnie produkcję próbnej partii pięćdziesięciu Light Riderów na sprzedaż, w cenie 56 tys. dolarów za sztukę.
W branży motoryzacyjnej widać zatem wyraźnie dwa nurty myślenia o druku 3D. Pierwszy to strategia małych kroków, czyli szukanie w technologiach addytywnych racjonalizacji, oszczędności i usprawnień, które z ich stosowania wynikają. Drugi to wizjonerskie projekty dotyczące budowy nieomal całych pojazdów i zrewolucjonizowania samego modelu produkcji. Obie drogi nie są wcale sprzeczne i być może spotkają się w całkiem niedalekiej przyszłości.