Przyszłość w proszku
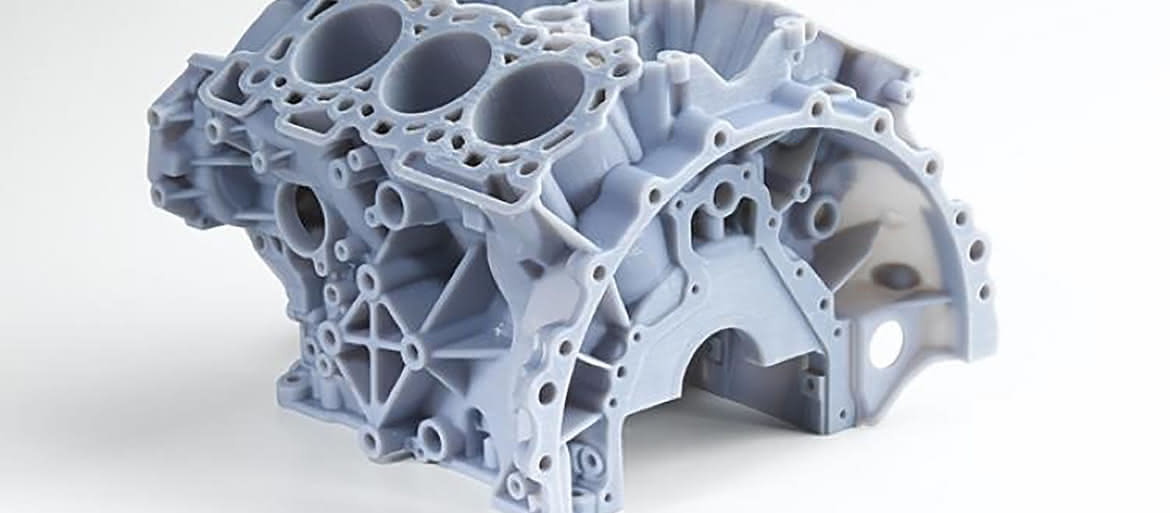
W ofercie VBN Components znajduje się np. Vibenite 290, która, zdaniem szwedzkiej firmy, jest najtwardszą stalą na świecie (72 HRC). Proces tworzenia Vibenite 290 polega na stopniowym zwiększaniu twardości materiałów do druku 3D. Po wydrukowaniu z tego surowca pożądanych części nie jest już wymagana żadna inna ich obróbka, oprócz szlifowania lub obróbki elektroerozyjnej. Nie potrzeba cięcia, frezowania czy wiercenia. Firma tworzy w ten sposób części o maksymalnych gabarytach do 200 x 200 x 380 mm, w geometriach niemożliwych do wykonania przy użyciu innych technik produkcyjnych.
Nie zawsze potrzebna jest stal. Zespół badawczy z HRL Laboratories opracował rozwiązanie, które pozwala na drukowanie w technice 3D stopów aluminium o wysokiej wytrzymałości. Nazywane jest ono metodą nanofunkcjonalizacyjną. Nowa technika, mówiąc w uproszczeniu, polega na nanoszeniu specjalnych nanofunkcjonalizacyjnych proszków do drukarki 3D, która następnie "spieka" cienkie warstwy laserem, co prowadzi do narastania trójwymiarowego obiektu. Podczas topienia się i krzepnięcia, powstające struktury nie pękają i utrzymują pełną wytrzymałość - dzięki nanocząstkom, działającym jako miejsca zarodkowania dla zamierzonej mikrostruktury stopu.
Stopy o wysokiej wytrzymałości, takie jak aluminium, są powszechnie stosowane w przemyśle ciężkim, w inżynierii samolotów (np. w kadłubach) i części samochodowych. Nowa technika nanofunkcjonalizacji nadaje im nie tylko wysoką wytrzymałość, ale i rozmaite kształty oraz rozmiary.
Dodawanie zamiast odejmowania
W tradycyjnych technikach obróbki metali niepotrzebny materiał usuwa się w obróbce skrawaniem. Proces addytywny działa odwrotnie - polega na nanoszeniu i dodawaniu kolejnych warstw złożonych z małych ilości materiału, tworzących na podstawie cyfrowego modelu trójwymiarowe części o praktycznie dowolnym kształcie.
Choć technika ta jest już szeroko stosowana do tworzenia prototypów a także modeli odlewniczych, jej wykorzystanie bezpośrednio w produkcji towarów czy urządzeń przeznaczonych na rynek było utrudnione ze względu na małą wydajność i niezadowalające właściwości materiałów. Sytuacja ta jednak powoli się zmienia dzięki pracy badaczy w wielu ośrodkach na świecie.
Na drodze żmudnych eksperymentów udało się dopracować dwie główne technologie druku przestrzennego: laserowe osadzanie metali (LMD) oraz selektywne topienie laserowe (SLM). Techniki laserowe dają możliwość dokładnego tworzenia małych elementów oraz uzyskania dobrej jakości wykończenia powierzchni, co nie jest możliwe w przypadku druku przestrzennego opartego na wiązce i łuku elektronów (EBM). W SLM punkt promienia lasera skierowany jest na proszek materiału, zgrzewając go miejscowo zgodnie ze z góry określonym wzorcem, z dokładnością od 50 do 250 μm. Z kolei w LMD wykorzystuje się laser do przetwarzania proszku w celu tworzenia samodzielnie utrzymujących się struktur 3D.
Techniki te okazały się bardzo obiecujące, jeżeli chodzi o tworzenie części samolotowych. Druk 3D, a w szczególności nanoszenie laserowego osadzania metalu, poszerza przestrzeń projektową dla komponentów lotniczych i kosmicznych. Mogą być one wykonane z materiałów o skomplikowanych strukturach wewnętrznych i gradientach w przeszłości niemożliwych do wykonania. Ponadto obie laserowe techniki umożliwiają tworzenie złożonych geometrii i uzyskanie zaawansowanych funkcjonalności produktów przy pomocy szerokiej gamy stopów.
We wrześniu ubiegłego roku Airbus ogłosił, że wyposażył swój seryjnie produkowany samolot A350 XWB w drukowany addytywnie tytanowy wspornik, wykonany przez firmę Arconic. To nie koniec, bo umowa Arconic z Airbusem przewiduje druk 3D z tytanowo-niklowego proszku części kadłuba i systemu silnikowego. Trzeba jednak zaznaczyć, że Arconic stosuje nie techniki laserowe, lecz własną zaawansowaną wersję łuku elektronów EBM.
Jednym z kamieni milowych w rozwoju technologii addytywnych w obróbce metali stanie się zapewne zaprezentowany jesienią 2017 r. w siedzibie holenderskiej Damen Shipyards Group pierwszy w historii prototyp śruby okrętowej ze stopów metali wydrukowany w 3D, nazwany WAAMpeller. Po odpowiednich testach, z których większość już się odbyła, model ma szansę otrzymać homologację do pracy na statkach.
Skoro przyszłość technologii metali leży w proszkach stali nierdzewnej czy komponentów stopów, warto poznać głównych graczy na tym rynku. Według opublikowanego w listopadzie 2017 r. opracowania „Metal Powders for Additive Manufacturing Market Report”, najważniejsi obecnie producenci metalowych proszków do druku 3D to: GKN, Hitachi Chemical, Rio Tinto, ATI Powder Metals, Praxair, Arconic, Sandvik AB, Renishaw, Höganäs AB, Metaldyne Performance Group, BÖHLER Edelstahl, Carpenter Technology Corporation, Aubert & Duval.
Faza ciekła
Najbardziej znane techniki addytywne z zastosowaniem metali polegają w tej chwili na wykorzystaniu proszków (tak powstaje wspomniany Vibenite), "spiekanych" i stapianych z użyciem lasera w wysokich temperaturach, wymaganych przez surowiec wyjściowy. Pojawiają się jednak nowe koncepcje. Badacze z pekińskiego laboratorium inżynierii kriobiomedycznej, należącego do Chińskiej Akademii Nauk, opracowali metodę drukowania 3D "tuszem", składającym się ze stopu metalu o temperaturze topnienia nieco powyżej temperatury pokojowej. W opracowaniu opublikowanym przez czasopismo "Science China Technological Sciences" badacze Liu Jing i Wang Lei prezentują technikę drukowania w fazie ciekłej, ze stopów na bazie galu, bizmutu lub indu z dodatkiem nanocząsteczek.
W porównaniu z konwencjonalnymi technikami prototypowania metali, drukowanie 3D w fazie ciekłej ma kilka ważnych zalet. Po pierwsze - można uzyskać stosunkowo dużą prędkość produkcji struktur trójwymiarowych. Poza tym temperaturę i przepływ cieczy chłodzącej da się tu regulować bardziej elastycznie. Płynny metal przewodzący może być w dodatku używany w połączeniu z materiałami niemetalowymi (np. tworzywami sztucznymi), co zwiększa możliwości projektowania złożonych elementów.
Nową technikę druku 3D z metali, tańszą i mniej skomplikowaną niż znane dotychczas, opracowali także naukowcy z amerykańskiego Uniwersytetu Northwestern. Zamiast metalowego proszku, laserów lub wiązek elektronowych, korzysta ona ze zwykłego pieca i płynnego materiału. W dodatku metoda sprawdza się dla szerokiej gamy metali, stopów, mieszanek i tlenków. Przypomina drukowanie z dyszy, jakie znamy w przypadku tworzyw sztucznych. "Tusz" składa się z proszku metalicznego rozpuszczonego w specjalnej substancji z dodatkiem elastomeru. W momencie nakładania ma temperaturę pokojową. Następnie warstwa nakładanego z dyszy materiału jest spiekana z poprzednimi warstwami w podwyższonej temperaturze wytwarzanej w piecu. Technika opisana została w specjalistycznym czasopiśmie "Advanced Functional Materials".
Badacze z Uniwersytetu Harvarda zaprezentowali w 2016 r. jeszcze inną metodę, w ramach której trójwymiarowe metalowe struktury mogą być drukowane "w powietrzu". Na Uniwersytecie Harvarda stworzono drukarkę 3D, która, w przeciwieństwie do innych, nie tworzy obiektów warstwa po warstwie, ale kreuje kompleksowe struktury „w powietrzu” - z metalu, który natychmiast zastyga. Urządzenie opracowane w John A. Paulson School of Engineering and Applied Sciences drukuje obiekty za pomocą nanocząstek srebra. Skupiony laser ogrzewa materiał i scala go w trakcie produkowania różnorodnych struktur, np. spirali.
Zapotrzebowanie rynku na wysoce precyzyjne, drukowane produkty użytkowe 3D - takie jak implanty medyczne i części do silników lotniczych - szybko rośnie. A ponieważ dane o produktach można dzielić z innymi online, firmy na całym świecie, jeśli tylko mają dostęp do proszku metalowego i odpowiedniej drukarki 3D, są w stanie pracować nad obniżeniem kosztów logistyki i zapasów. Jak wiemy, opisywane technologie znacznie ułatwiają produkcję metalowych części o skomplikowanej geometrii, wyprzedzając w tej kwestii tradycyjne techniki produkcji. Rozwój wyspecjalizowanych zastosowań przyniesie zapewne spadek cen i otwieranie się na wykorzystanie druku 3D także w konwencjonalnych zastosowaniach.
Najtwardsza szwedzka stal - do druku 3D:
Film o druku z aluminium: