Nowe materiały budowlane
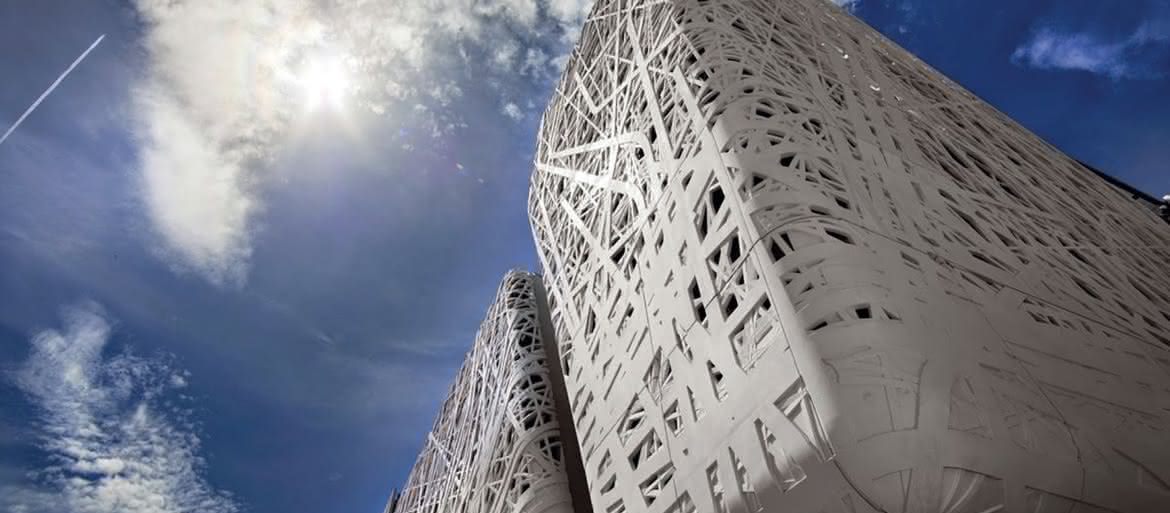
Pomysłów na zupełnie nowy beton nie brakuje. Taki np. Hendrik Jonkers, mikrobiolog z holenderskiego Uniwersytetu Delft, chce w nim umieszczać zarodki bakteryjne, aby drobnoustroje leczyły powstające w materiale pęknięcia.
Według szacunków tylko na terenie Unii Europejskiej naprawa betonowych konstrukcji, konieczna z powodu uszkodzeń i pęknięć, pochłania rocznie 6,5 mld dolarów.
Jonkers uznał, że zastosowanie biologicznej metody leczenia betonu to dobry pomysł, zarówno pod względem ekonomicznym, jak i ekologicznym.
Jednak alkaliczne środowisko chemiczne panujące w tym materiale budowlanym nie służy mikrobom. Na szczęście Holender przypomniał sobie swoje wczesne badania nad ekstremofilami, mikroorganizmami zdolnymi do przetrwania w miejscach, gdzie inne formy życia giną.
Jego zdaniem gatunki takie jak bacillus pseudofirmus i bacillus cohnii mogą dać radę, gdyż normalnie żyją w jeziorkach o zasadowym odczynie w okolicach wulkanicznych. Ich endospory, czyli formy przetrwalnikowe, potrafią znieść odczyn pH 12-13.
Ten biobeton powstaje przed dodanie do mieszanki endosporów oraz mleczanu wapnia, który stanowi ich pożywienie. Zawartość tych komponentów to ok. 1% objętości mieszanki.
Po zastygnięciu betonowego elementu, endospory mogą "przespać" nawet i dwieście lat w niezmienionym stanie. Gdy jednak dotrze do nich powietrze lub woda, co dzieje się właśnie w przypadku pęknięć, przetrwalniki ożywają i rozpoczynają swoją pracę.
Polega ona na pochłanianiu wapniowego "pokarmu" i wydzielaniu jonów węglanowych, które reagują z wapniem w betonie, tworząc w miejscu spękań wapienny wypełniacz (1). Bakteriom zajmuje to ok. trzy tygodnie.
Oczywiście drobnoustroje dają sobie radę jedynie z drobnymi pęknięciami, do 0,8 mm szerokości. Jednak zważywszy, że zapobiegają ich powiększaniu wtedy, gdy są niewielkie, spełniają swoją funkcje znakomicie.
Biobeton opracowany przez holenderskiego naukowca ma być dostępny na rynku już w 2016 r. Będzie o połowę droższy niż zwykły, ale jego twórca jest pewien, że wydatek zwróci się dzięki oszczędnościom na remontach betonowych konstrukcji.
Rozwiązanie w elementach małych, choć niekoniecznie żywych, znajduje również znana firma BASF. W ubiegłym roku przedstawiła alternatywę dla napowietrzonego betonu, materiału budowlanego stosowanego w klimatach zimnych, gdzie występują cykle zamarzania i topnienia.
Zamiast napowietrzania proponuje się tu użycie mikrokapsułek (2), pokrytych wytrzymałym, ale elastycznym materiałem polimerowym. Ich działanie w poddanym naprężeniom z powodu zmian temperatur betonie można porównać do amortyzacji. Producent zapewnia, że jego beton jest o 30% wytrzymalszy niż napowietrzona mieszanka.
Cement czyszczący powietrze
Co łączy włoski pawilon Palazzo Italia (3) na rozpoczęte w maju targi EXPO 2015 w Mediolanie i ruchliwy most w Barcelonie? Obie konstrukcje zostały wykończone betonem filtrującym zanieczyszczenia z powietrza.
Supermateriał zamienia szkodliwe tlenki azotu i siarki w nieszkodliwe sole. W obu projektach przewidziano zastosowanie tzw. betonu fotokatalitycznego, a więc reagującego na światło.
Gdy materiał zostaje wystawiony na działanie promieni słonecznych, uruchamia się proces fotokatalizy, w ramach którego zanieczyszczenia zaczynają się utleniać, rozkładać i zamieniać w nieszkodliwe sole osadzające się w strukturze betonu. By je wypłukać, a przy okazji zmyć beton, wystarczy obfity deszcz.
Zespołowi badawczemu pracującemu w ramach projektu udało się opracować fotokatalizator na bazie dwutlenku tytanu, który pozwala oczyszczać powietrze również w świetle widzialnym, w przeciwieństwie do katalizatorów poprzedniej generacji, działających wyłącznie w świetle ultrafioletowym.
Jak na razie projekt znajduje się na etapie procedury składania wniosku patentowego, a gdy produkt uda się opatentować, ma być produkowany na skalę przemysłową.
Pokrewną filtrującemu cementowi jest technologia kanadyjskiej firmy CarbonCure Technologies Inc., która wykorzystuje mieszankę betonową do sekwestracji dwutlenku węgla, głównego gazu cieplarnianego, którego nadmiar w atmosferze stanowi główną przyczynę globalnego ocieplenia.
CO2 jest tu dodawany do mieszanki na etapie powstawania betonu. Gaz reaguje z wodą, tworząc jony węglanowe, co na zasadzie opisanej już przy okazji biobetonu daje w efekcie nanodrobiny wapienia rozmieszczone w mieszance.
Zsekwestrowany gaz cieplarniany stanowi 1% wagi powstałego betonu. Wydaje się, że to niewiele, ale gdy weźmiemy pod uwagę, że na świecie rocznie produkuje się ok. 20 mld ton betonu opartego na cemencie portlandzkim, to potencjalnie zyskujemy miejsce na przechowanie 200 mln ton CO2!
To choć trochę zmniejszałoby karbonowy odcisk, jaki pozostawia w środowisku produkcja cementu i betonu - choć go nie niweluje, gdyż emisję dwutlenku węgla podczas produkcji betonu szacuje się na ok. 180 kg/tonę przy gęstości 2,3 g/cm3 (14% cementu).
Beton tekstylny zamiast żelbetu
Concrete Canvas Shelter (4) to rodzaj namiotu zrobionego, na pierwszy rzut oka, z płótna. Po dodaniu wody "płótno" twardnieje i powstaje podobna do cienkiej warstwy betonu skorupa, która może być wykorzystana np. w warunkach klęski żywiołowej.
Tym sposobem witamy w świecie "betonów tekstylnych", czyli materiałów budowlanych, które zamiast stalowych prętów typowych dla żelbetonu, wzmacniane są włóknami tkanin lub innych podobnych materiałów.
Cała ich generacja była niedawno prezentowana podczas targów Techtextil we Frankfurcie nad Menem. Płytami wykonanymi z takiego właśnie tekstylnego betonu pokryto fasadę budynku restauracji "Am Schiefersee" w niemieckim mieście Dormettingen.
Panele o długości 4 m i grubości 50 mm ważą łącznie o połowę mniej niż ważyłaby ściana z tradycyjnego betonu (5). Badania nad nowymi rodzajami tekstylnego betonu, z zastosowaniem jednowarstwowej lub wielowarstwowej osnowy wzmacniającej, wykorzystującej włókna szklane lub węglowe (6), mają w Niemczech zielone światło.
Powstaje już sporo konstrukcji, takich jak lekkie membranowe dachy (7), łączących lekkość płótna ze sztywnością betonu. Pojawiają się pomysły, aby stosować naturalne włókna, np. len i konopie, jako świetny sposób na izolację cieplną ścian.
Do włóknistej osnowy planuje się wplatać sensory monitorujące ciepło, światło, wilgotność, zadymienie i ewentualne pojawienie się ognia. Tekstylny beton stałby się więc podstawą infrastruktury domów inteligentnych - smart home.
Biologiczna cegielnia
Cegły z powszechnie dostępnych, niedrogich materiałów, produkowane przez drobnoustroje (8) - oto propozycja biotechnologicznego startupu o nazwie bioMason. Wynalazek został niedawno wyróżniony przez wspierający innowacje instytut Cradle to Cradle z San Francisco.
Twórcy nowej metody produkcji materiałów budowlanych podkreślają, że ich technologia w porównaniu z dotychczasowymi, energochłonnymi procesami produkcji dla budownictwa z betonu, szkła, stali i drewna, jest niezwykle przyjazna dla środowiska.
Ich "biocement" wytwarzany przez bakterie z dostarczanych składników, powstaje naturalnie, w temperaturze otoczenia, podobnie jak twarde rafy koralowe. Mikrobom do produkcji owego organicznego cementu potrzebna jest, oprócz substancji odżywczych, jak azot i wapń, także woda.
Przedstawiciele firmy bioMason twierdzą, że jest ona w procesie technologicznym poddawana recyklingowi, krążąc w zamkniętym cyklu. Co więcej, do produkcji może być wykorzystywana z powodzeniem słona woda morska.
Jako dodatek ekologiczny z powodzeniem mogą być dodawane do cementu i betonu łuski słonecznika.
Twierdzi tak grupa tureckich uczonych, którzy przekonują, że wprowadzenie tej technologii utylizacji słonecznikowego odpadu da wiele korzyści środowiskowych i technologicznych.
Turcja, jeden z największych plantatorów i producentów oleju słonecznikowego, produkuje milion ton łusek rocznie. Jeśli dodać, że beton z dodatkiem zmielonych odpadów ma mniejszą gęstość i większą odporność na naprężenia związane ze zmianami temperatur, to turecki pomysł wygląda coraz ciekawiej.
Beton z takim dodatkiem, zdaniem naukowców, powinno stosować się w pierwszej kolejności przy zabudowaniach gospodarczych i przemysłowych. W przypadku budynków mieszkalnych nadawałby się raczej do izolacji, nie zaś do głównych elementów konstrukcyjnych.
Polacy też mają pomysły
W ostatnich latach jednymi z ciekawszych i najbardziej obiecujących materiałów budowlanych są geopolimery. Jest ich wiele rodzajów i mają ciekawe zastosowania. Amerykański GeoSpray jest np. coraz szerzej stosowany do bezwykopowej naprawy uszkodzeń rur kanalizacyjnych (9).
Także w Polsce powstają tego rodzaju materiały. Geopolimer, stworzony na Politechnice Krakowskiej przez zespół kierowany przez prof. Janusza Mikułę, posłużyć może do produkcji superodpornych materiałów budowlanych, które mają szansę zrewolucjonizować światowy rynek.
Powstał na bazie tufu, czyli kamienia wulkanicznego z Filipowic. O jego wyjątkowości w dużej mierze decyduje stosunek krzemu do aluminium wynoszący 5:6, podczas gdy w standardowych geopolimerach na bazie metakaolinu czy popiołu lotnego to 2:3.
Materiał ma bardzo wysoką wytrzymałość termiczną, nawet do 1000°C i jest odporny na siarczyste mrozy, sięgające nawet -50°C.
Nie poddaje się szkodliwemu działaniu kwasów, chlorków oraz siarczanów i jest wręcz ekstremalnie odporny na ścieranie, a co za tym idzie - na rozmaite uszkodzenia mechaniczne.
Do wspomnianych cech dodać trzeba również odporność na korozję, która charakteryzuje wszystkie polimery tego typu, co ma ogromne znaczenie w kontekście budownictwa. Na uwagę zasługuje także jego wytrzymałość na ścieranie.
Podczas gdy na zwykłych geopolimerach skutki ścierania są widoczne po ok. 20 minutach, nasz pozostał nienaruszony po trzech dniach, nie licząc nadanego mu połysku. Po naniesieniu takiej powłoki np. na ścianę, na jej powierzchni utworzy się cienka warstwa kamienia o właściwościach geopolimeru.
Jeśli nadamy jej odpowiednią porowatość, będzie ona zdolna do regulacji poziomu wilgotności i pochłaniania zapachów. Jak zapewniają członkowie krakowskiego zespołu badawczego, geopolimer, po wzbogaceniu barwnikami ceramicznymi, przyjmuje dowolny kolor, więc może zastąpić zwykłą farbę.
A może jednak kompozyty?
Specjaliści wciąż szukają nowych, szybszych i tańszych sposobów na budowę obiektów o jak najlepszych właściwościach mechanicznych. Nową metodę przedstawili właśnie naukowcy z renomowanego Massachusetts Institute of Technology (MIT).
Polega ona na budowaniu rzeczy wielkich z elementów o bardzo małych rozmiarach. Tym samym wracamy do szukania wielkich rozwiązań w bardzo małych skalach.
Propozycja, przedstawiona w znanym magazynie "Science" przez dwóch badaczy z MIT, Kennetha Cheunga i Neila Gershenfelda, polega na składaniu dużych i bardzo dużych elementów z małych struktur z włókien kompozytowych (10), przypominających sieć.
Struktura sieci nie jest oczywiście przypadkowa. To właśnie uzyskany drogą badań ten a nie inny rodzaj struktury powoduje, że składane z niej konstrukcje są dziesięciokrotnie sztywniejsze niż wykonane innymi technikami, o podobnej masie.
Obecnie w przemyśle, np. lotniczym (Dreamliner), wytwarza się już bardzo wiele elementów z kompozytów. Jednak stosowane technologie wymagają dużych fabryk, linii produkcyjnych, nakładów itd. Proponowana przez badaczy z MIT technologia materiałowa jest prostsza, tańsza i w dodatku stworzone elementy można w razie potrzeby dość łatwo rozkładać.
Cheung i Gershenfeld pracują nad robotami produkcyjnymi, które mogłyby służyć do składania obiektów z zaprojektowanych przez nich struktur.