Jak się robi kafle?
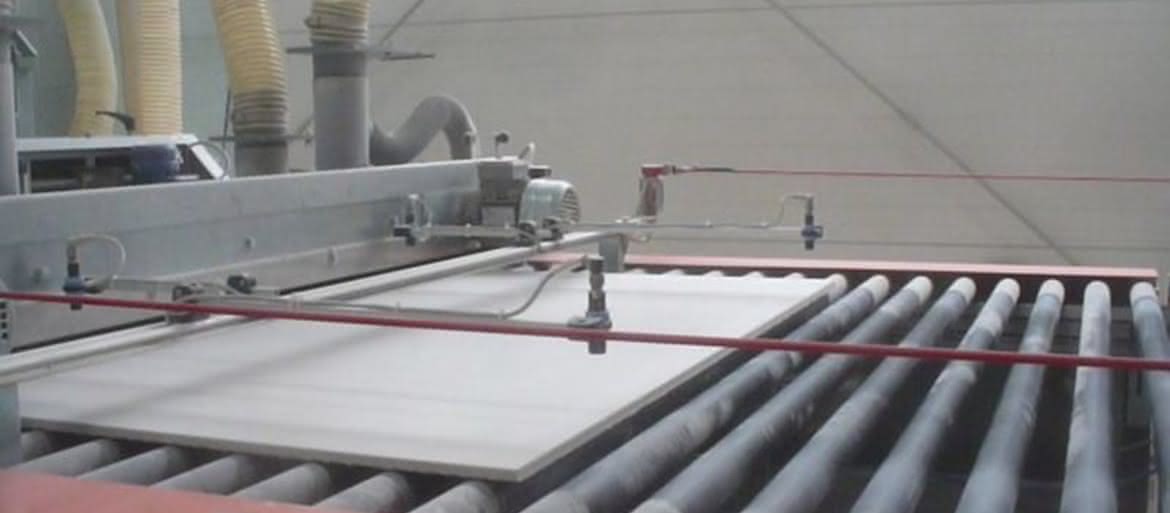
W Polsce otworzono właśnie najnowocześniejszą na świecie fabrykę produkującą płytki ceramiczne. Płytki każdy zna i docenia ich zalety, ale ich proces powstawania z surowców mineralnych jest wart poznania.
Surowcami do produkcji kafli są różnego rodzaju iły, glina, do tego sypkie krzemionki, czyli piasek albo kwarc mielony oraz topniki. Gliny nadają płytkom plastyczność, krzemionki zmniejszają kurczliwość, a skalenie zawierające dużo K2O i Na2O, czyli topniki, stosuje się dla zmniejszenia porowatości. Skalenie topią się podczas końcowego wypalania płytek. Wytwarzanie leiwa. Dostarczone ciężarówkami materiały gromadzi się i przechowuje w magazynie pod chmurką w oddzielnych boksach. W miarę potrzeb transportuje się je do hali produkcyjnej.
Bryły gliny polewane wodą trafiają na walce nożowe. Już częściowo rozdrobnione kierowane są do bełtaczy łopatkowych, w których powstaje jednorodny wodny roztwór. Piasek tymczasem transportuje się do młyna rurowego. Tam trafia też skaleń i wodny roztwór gliny. Młyn pracuje bez przerwy, czyli w ruchu ciągłym. Przetwarza 15 ton masy piaskowo-glinowo-skaleniowej na godzinę. Komora wewnętrzna młyna wyłożona jest gumą odporną na ścieranie, a surowiec jest mielony alubitowymi. Kulki te ścierają się podczas procesu mielenia i trzeba je stale uzupełniać. Zapasy kulek alubitowych w workach czekają na użycie.
Zmielona i wymieszane glina, iły i piasek z wodą od tej pory stają się leiwem. Leiwo z końca młyna rurowego wypływa na ruchome sita. Sita zatrzymują niedostatecznie zmielone cząstki, a cała reszta trafia do zbiornika pośredniego wyposażonego w dwa mieszadła. Te, wolno wirując, nie pozwalają rozwarstwiać się leiwu.
Granulat
Ze zbiornika dolnego leiwo przepompowuje się do drugiego górnego zbiornika, który mieści się nad suszarnią rozpyłową. W suszarni rozpyłowej system dysz rozpyla pod wysokim ciśnieniem leiwo do postaci drobnych cząstek. Te trafiają na przeciwbieżny strumień gorącego powietrza o temperaturze około 500°C. Leiwo w gorącu błyskawicznie odparowuje i opadając, zmienia się w kulki granulatu. Po przejściu przez sito wibracyjne granulat przenośnikami taśmowymi transportowany jest do magazynu, albo zaraz potem do linii produkcyjnej.
Wytłaczanie
Formowanie płytek odbywa się poprzez sprasowanie granulatu pod ciśnieniem 59 MPa. Ważne jest równomierne rozmieszczenie granulatu pomiędzy żeberkami wózka zasypowego oraz odpowietrzenie masy. Wózek wykonuje cykl ruchów do przodu do tyłu, i ruchy te są sprężone z podnoszeniem i opadaniem dolnych i górnych stempli formy. Wreszcie sprasowane, oczyszczone i wypchnięte z formy płytki jadą przenośnikiem rolkowym do suszarni. Jeszcze tylko po drodze zostaną omiecione przez miękkie wirujące okrągłe szczotki.
Suszenie
Suszarnia wieżowa ma półki poruszające się w cyklu zamkniętym a płytki suszy się w przeciw prądzie ogrzanego powietrza. Komora spalania opalana jest gazem ziemnym, a wewnętrzna temperatura suszenia wynosi około 100°C. Płytki wilgotne samoczynnie wypychają z półek płytki już wysuszone. W czasie kilkudziesięciu minut wilgotność masy spada poniżej 1%. Suszenie nadaje surowym płytkom wytrzymałość mechaniczą oraz utrwala kształt. To jednak nie wystarcza, bo przecież płytka powinna mieć twardą, nieporowatą, gładką i lśniącą powierzchnię.
Szkliwienie i dekorowanie
Efekt taki można uzyskać tylko podczas procesu szkliwienia. Linia szkliwierska ma kilkadziesiąt metrów. Jest to rodzaj przenośników paskowych transportujących surowe płytki pod urządzeniami do aplikacji szkliwa. Szkliwa komponowane są z barwnikami. Schłodzone i oczyszczone płytki transportowane są dalej. Po drodze spodnia część płytki pokrywana jest tak zwaną podbiałką. Podbiałka zapobiegnie w przyszłości przyczepieniu się płytki do walców ceramicznych podczas wypalania.
Wzory na wierzchniej powierzchni płytek nakłada się urządzeniem nazywającym się Rotocolor. Jest to zestaw walców ustawionych prostopadle do kierunku linii. Metalowe walce pokryte są silikonem na którym laserowo wygrawerowano wybrany wzór. Walce tymczasem nanoszą na przesuwające się płyt-ki wzór z past ceramicznych w rożnych odcieniach. Niekiedy do nakładania dekoracji używa się pistoletów pneumatycznych czyli aerografów. Tak przygotowana płytka wędruje do prasy o naciski 7500 ton. Tu następuje finalne zgęszczenie granulatu.
Wypalanie
Po zakończeniu procesu dekorowania płytki są wyrównywane, fazowane i czyszczone a następnie automatycznie układane w rolkowych regałach. Teraz płytki są suszone i wypalane w piecach do wypału. Proces trwa około godziny a przepływający strumień płytek ogrzewany jest od temperatury otoczenia aż do 1250 stopni Celsjusza. Płytki jadą na obracających się ceramicznych rolkach napędzanych silnikami elektrycznymi przez całą długość pieca.
Utrwalona zostaje dekoracyjna powłoka a w masie ceramicznej uzyskuje się finalne właściwości fizyko-chemiczne, czyli nasiąkliwość i tak ważną wytrzymałość mechaniczną. Praca pieców jest całkowicie zautomatyzowana. Największe wrażenie robią samodzielnie, bez żadnej obsługi poruszające się po wielkiej hali wózki. Ruszają z miejsca zawracają zakręcają i zabierają całe pełne regały płytek do wypalenia i przywożą wypalone. Sterowane są za pomocą komputera i same wiedzą, kiedy i który regał jest pełen płytek i należy go zabrać do sortowni, a który jest pusty i należy go podstawić, by znowu został napełniony płytkami do wypalenia. Po za tym taki samodzielny wózek wyposażony jest w system bezpieczeństwa, bo natychmiast zatrzymał się, gdy stałem na jego drodze, zagapiłem się i robiłem jedno ze zamieszczonych tu zdjęć. Tymczasem wypalone gotowe płytki poddawane są weryfikacji.
Ostateczna kontrola
Weryfikacja automatyczna eliminuje płytki które nie mają prawidłowych wymiarów geometrycznych i planimetrycznych. Robią to bezdotykowe instrumenty pomiarowe. Wszystkie płytki są rafinowane, czyli mają dokładne takie wymiary, jakie zaprojektowano. Potem wpływa to na łatwość i dokładność ich ułożenia. Na końcu jest jeszcze pracownik, który bacznie kontroluje płytki wzrokiem. Z linii sortowniczej przenośnikiem transportowane są płytki do maszyny pakującej. Ta owija stosowną liczbę płytek kartonem i nadrukowuje dane opisujące produkt.
Pakowanie i ekspedycja
Kartony układane są na drewnianych paletach, oczywiście za pomocą zautomatyzowanego chwytaka. Popakowane płytki wysyłane są do sklepów i hurtowni w kraju i za granicę.
My tymczasem z grubego folderu, możemy sobie wybrać, którym z 35 rodzajów płytek wyłożymy sobie podłogi i łazienkę. Do wyboru mamy kafelki o wielkości od małych 20 na 20 milimetrów do wielkich kafli 1200 na 1200 milimetrów. Do tego różnych rozmiarów pośrednich jest naprawdę dużo. Kafle mogą być matowe naturalne lub lśniące, wyglądające jak polane wodą ale wcale nie bardzo śliskie. Takimi wykłada się posadzki bardzo luksusowych i prestiżowych miejsc.