Vademecum Młodego Wynalazcy
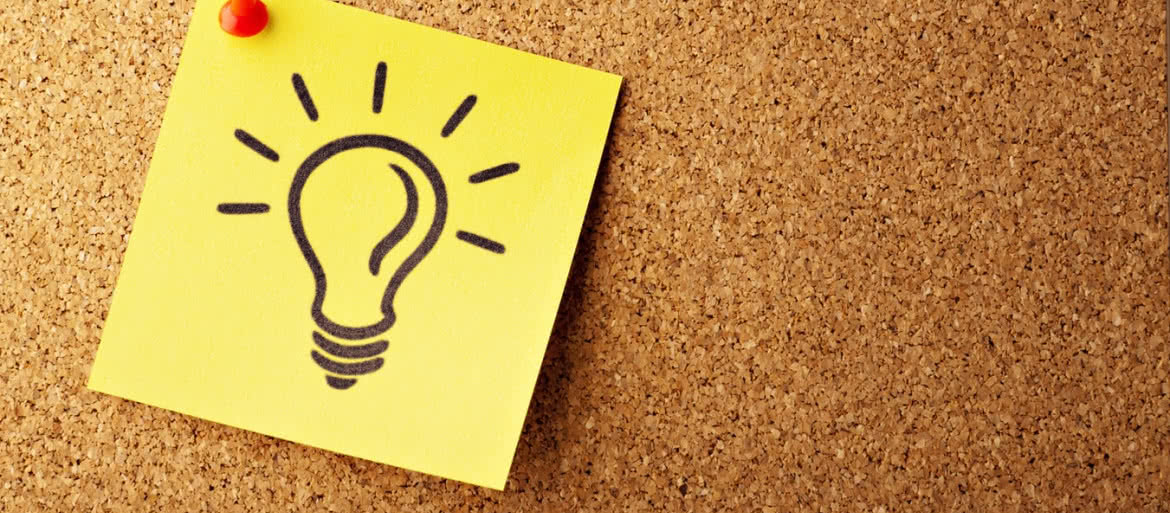
Na problem resursów należy spojrzeć z dwóch punktów widzenia. Po pierwsze, rozważamy, co by się nam przydało do rozwiązanie problemu, lub inaczej – jak może wyglądać x-element, który jest w stanie rozwiązać problem. Niezależnie od tego, trzeba też patrzeć na kwestię resursów od strony „operatora systemowego”, a więc widzieć resursy systemowe, nadsystemowe i podsystemowe, oraz spojrzeć na nie „wczoraj” „dziś” i „jutro”.
Dowolny system „dziś” ma jakiś pakiet resursów, ale wcześniej miał nieco inne resursy, a w przyszłości może mieć zupełnie inne. Prostym przykładem ilustrującym tę sprawę niech będzie problem… mielenia karkówki w maszynce elektrycznej.
Powrót do przyszłości, czyli karkóweczka raz!
Karkówka to mięso dość tłuste, nieco żylaste, bardzo łatwo nawijające się na ślimak maszynki, po czym dalej… ani rusz – „nie chce” iść do przodu w strefę nożyków i sitka. Gdy przyjrzymy się sytuacji, łatwo zauważyć, że mięso po prostu ślizga się wewnątrz korpusu i obraca razem ze ślimakiem. Należałoby jakoś wyhamować jego ruch w stosunku do powierzchni wnętrza maszynki. Rozporządzalne resursy to:
● mięso, wraz z jego szczególnymi cechami: śliskie, żylaste, tłuste;
● korpus maszynki: żebrowany, co ma zabezpieczać mięso przed obrotem;
● nożyki i sitko – na razie nie biorą udziału w procesie przesuwania mięsa do przodu.
Zmienić tych elementów „dziś” nie możemy. „Wczoraj” – też nie. Przyjrzyjmy się więc, co zmieni się w zestawie resursów „jutro”. Dojdą dalsze komponenty sznycli: a więc: jaja, mąka, bułka tarta, przyprawy. Z tych elementów najbardziej obiecująco wygląda bułka tarta: jest sucha, czyli może zmienić warunki tarcia mięsa o żeberka wnętrza korpusu.
Wyjmujemy więc mięso z maszynki i lekko przesypujemy bułką tartą, po czym… mielimy, aż miło! Mięso gładko przechodzi przez maszynkę i wychodzi elegancko zmielone! Wykorzystaliśmy resurs systemowy: którego „dziś” nie ma, ale wiadomo, że „jutro” będzie, czyli lekko wyprzedzając kolejność, wprowadzamy bułkę tartą do systemu i już!
Spojrzeć w przeszłość, czyli połączyć kropki
To był przykład sięgnięcia po resursy „z przyszłości”. Teraz przedstawmy resursy „z przeszłości”.
Dość często zdarza się, że przechowywany w pojemniku lub silosie materiał sypki „nie chce” wypadać ze zbiornika z powodu zbrylenia. Chodzi m.in. o takie materiały, jak gips, cement czy wapno. Przechowywanie mączki wapiennej w dużym silosie o średnicy nawet do 7 m i wysokości do 35 m (2) stanowi wygodny sposób – pod warunkiem, że mączka się nie zbryla. W przeszłości podejmowano w tym celu różne wysiłki, począwszy od walenia drągiem po gardzieli silosu, przedmuchiwania sprężonym powietrzem z pomocą dysz, które oczywiście zatykały się natychmiast po wyłączeniu ciśnienia, instalowania kapturków, osłaniających wyloty dysz od góry, ale wszystko to było nie do końca skuteczne.
Sprawdzamy resursy. „Dziś” mamy:
● duży silos, wypełniony mączką wapienną,
● mączkę wapienną,
● wilgoć wchłoniętą przez mączkę,
● grawitację,
● higroskopijność całej partii mączki w silosie.
Już bez głębszej analizy widać, że „przeszkodą nr 1” dla procesu wysypywania porcji mączki pozostaje wilgoć. Wydaje się więc, że należy ją po prostu usunąć i po kłopocie. To nie jest jednak takie proste; mączkę najpierw transportuje się taśmociągiem z pieca na samochody, a następnie przewozi w tych samochodach – skrzyniowych – osłoniętych plandeką. Wszystko to trwa średnio ok. godziny, w trakcie której mączka nieustannie chłonie wilgoć z powietrza.
To nie koniec. Na miejscu mączka jest przeładowywana transportem pneumatycznym – powietrzem takim, „jakie jest”, a więc zazwyczaj zawierającym nieco wilgoci. A co się dzieje z wilgocią w zamkniętym już silosie? Mają tu miejsce dwa procesy: grawitacyjne opadanie wilgoci oraz podciąganie jej dzięki zjawisku włoskowatości.
Gdyby udało się jakoś wzmocnić to ostatnie, powstałaby szansa na uzyskanie w dolnej części silosu mączki suchej, a więc łatwiej wysypującej się po otwarciu zasuwy. Być może, gdyby skorzystać ze zjawiska elektroosmozy, udałoby się „przegonić” wilgoć do góry. Należałoby jednak wykonać próby, dobrać parametry elektryczne i oczywiście przeanalizować całość także z punktu widzenia ekonomicznego.
Nie wiemy jednak, które zjawisko działa efektywniej: czy grawitacyjne opadanie wilgoci, czy higroskopijne podnoszenie jej, oraz czy elektroosmoza dałaby radę grawitacji i wystarczająco intensywnie podciągnęła wilgoć. A sprawa dotyczy przemysłu budowlanego, jest więc poważna w skali krajowej.
Prześledźmy kolejne resursy, czyli spójrzmy na pion operatora systemowego – „wczoraj”.
Wapno powstaje w piecu wapienniczym, a więc:
● w chwili wydobywania mączki z pieca jest ona w 100% sucha, gorąca i sypka;
● mączka wchłania wilgoć z powietrza podczas przesyłania jej taśmociągiem do skrzyń samochodów;
● w trakcie jazdy autem mączka, przykryta jedynie folią lub plandeką, chłonie wilgoć z powietrza;
● podczas przeładowywania mączki z samochodu do silosa nadal chłonie ona wilgoć – tym razem z powietrza użytego przez dmuchawy lub sprężarki wdmuchujące ją do silosa.
Jak widać, mączka jest naprawdę sucha i sypka tylko w chwili, gdy wydobywa się ją z pieca. Oczywistym wnioskiem staje się więc pakowanie jej wówczas do worków „wentylowych” (jak cement) lub foliowych, z pomocą maszyny pakującej, ustawionej tuż przy wylocie z pieca.
Taki sposób przechowywania i transportu byłby optymalny. Pozostaje jednak problem silosów – co z nimi zrobić?
Rozwiązując tę kwestię na zasadzie analizy resursów, staramy się wykorzystać te z nich, które są w systemie lub pozostają darmowe, albo tanie.
Ciekawym rodzajem resursów są resursy informacyjne, z których najpowszechniejsze są informacje, a nawet tylko szkice idei, mające uniwersalny charakter, nadające się do wykorzystania w różnych dziedzinach.
Przykładów takich idei jest w technice bardzo dużo.
Oto najprostszy przykład: od wielu stuleci obudowy chodników kopalnianych wykonywano z drewna. Składały się z dwóch stempli, na których spoczywała belka pozioma (3).
Cały szereg takich „bramek” tworzył ciągłą obudowę chodnika. Gdy pojawiła się stal i zaczęła być coraz bardziej dostępna, zaczęto wykonywać obudowy z profili stalowych. Poziome belki stalowe nie wytrzymywały jednak ciężaru górotworu i uginały się pod jego naciskiem.
W którymś momencie jeden z inżynierów górnictwa zaproponował więc obudowę z łukowych, „stropopodobnych” elementów (4). Okazały się znacznie skuteczniejsze niż poprzednie belki poziome.
Czy był to jakiś nowy wynalazek? Oczywiście nie. Łukowe sklepienia znano już od stuleci jako sklepienia romańskie, a wcześniej „rzymskie” – stosowane w budowie mostów (5).
To znane już dobrze rozwiązanie trafiło następnie do hydrobudowy, co spowodowało „erę” tam i zapór wodnych, wznoszonych w linii łukowej (6).
Idea łukowych elementów oporowych trafiła wreszcie do przemysłu maszyn budowlanych i ziemnych. Koparki jednoczerpakowe, a później wieloczerpakowe, zaczęto wyposażać w krawędzie czerpaków, ukształtowane również po łuku (7).
Jak widać, idea była prosta, ale od sklepień romańskich do koparek „musiało” upłynąć ponad tysiąc lat. Informacja znajdowała się „w systemie”, istniała jednak inercja psychologiczna, hamująca postęp. Zjawisko „opóźniania” wdrożeń znanych idei jest typowe. Prawdopodobnie wchodzi tu też w grę izolacja różnych gałęzi przemysłu i techniki. Przykłady historyczne mówią o setkach lat opóźnienia w wykorzystaniu rozmaitych gotowych już koncepcji.
Szkła optyczne umiano szlifować od dawna, ale pomysł ustawienia jednej soczewki za drugą i stworzenia w ten sposób lunety musiał czekać aż trzysta lat! Oznaczało to jednocześnie trzysta lat opóźnienia w badaniach najbliższego nam kosmosu, a także trzysta lat opóźnienia w badaniach biologicznych, do których potrzebny był mikroskop!
Współczesny TRIZ przywiązuje dużą wagę do dogłębnej analizy oraz udzielania wszechstronnej i dokładnej odpowiedzi na proste pytanie: gdzie TO jeszcze można wykorzystać?
Prezes Klubu Wynalazców, Instruktor TRIZ, Jan Boratyński