Jak to działa - technologie membranowe
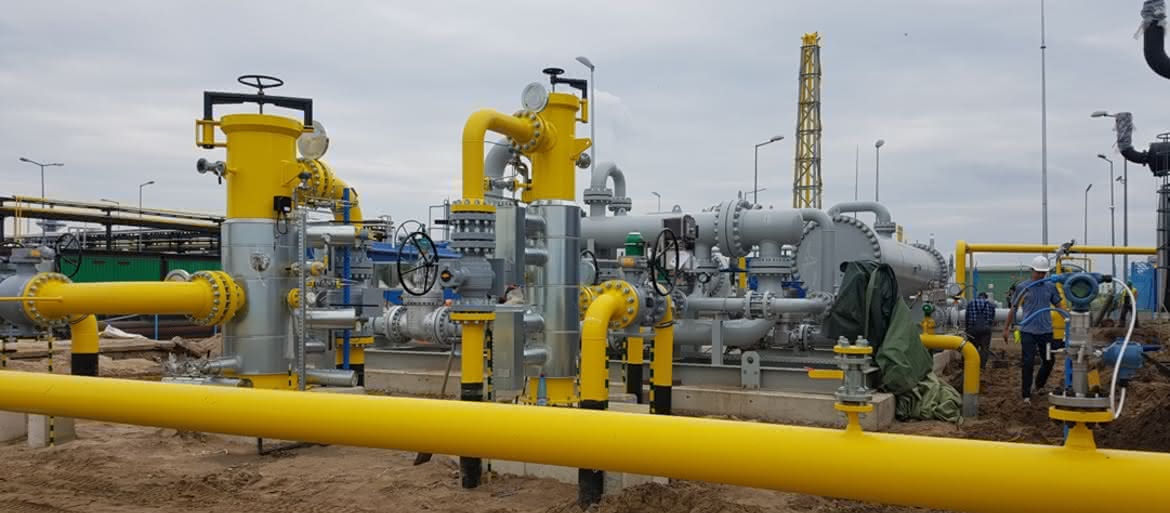
Główne technologie wykorzystywane obecnie do rozdzielania to destylacja i sorpcja. Dobrze spełniają swoje zadanie, lecz są kosztowne ze względu na duże zużycie energii (do ich przeprowadzenia potrzeba dużych ilości ciepła). Z tej przyczyny przemysł poszukiwał i nadal poszukuje nowych, bardziej energooszczędnych metod rozdziału. Należą do nich technologie membranowe.
Membranę można zdefiniować jako przegrodę, która przepuszcza pewne składniki mieszaniny, a inne zatrzymuje. Jest to więc przegroda półprzepuszczalna. W pokazanym na rys. 1 przykładzie membrana przepuszcza jedynie substancję A, zatrzymując substancję B, co pozwala na rozdzielenie mieszaniny. Transport substancji przez membranę jest wymuszany poprzez zastosowanie odpowiedniego bodźca - najczęściej różnicy ciśnienia po obu stronach membrany.
Zaletą wykorzystania membran jest brak konieczności dostarczania ciepła, co sprawia, że prowadzenie rozdziału staje się tańsze niż w przypadku destylacji. Widać to na przykładzie odsalania wody morskiej za pomocą membran (w procesie odwróconej osmozy, znanym powszechnie z zastosowania w domowych filtrach wody). Wymaga ono dziesięciokrotnie mniejszej ilości energii niż termiczne metody odsalania. Instalacje membranowe mają prostszą konstrukcję, co zapewnia im mniejszą awaryjność. Niewielkie rozmiary w porównaniu do wysokich kolumn destylacyjnych, które nieraz sięgają kilkudziesięciu metrów wysokości, stanowią przewagę w odległych bądź trudno dostępnych miejscach (np. na wieżach wiertniczych).
Jak to się zaczęło?
Pierwszy eksperyment związany bezpośrednio z membranami został wykonany w połowie XVIII wieku przez francuskiego fizyka Jeana Antoine Nolleta, który zaobserwował, że błona ze świńskiego pęcherza przepuszcza szybciej wodę niż alkohol etylowy. Systematyczne badania transportu gazów przez membrany zapoczątkował i prowadził przez dwadzieścia lat XIX wieku Thomas Graham.
Pierwsza połowa XX wieku to dalszy rozwój rozumienia tych procesów, w czym miał swój udział również polski uczony Zygmunt Wróblewski (który jednak bardziej znany jest z tego, że wspólnie z Karolem Olszewskim dokonał pierwszego na świecie skroplenia tlenu i azotu). Prawo dyfuzji, podane przez Grahama, stało się podstawą pierwszego zastosowania membran, czyli rozdzielania izotopów uranu na potrzeby budowy bomby atomowej przez Stany Zjednoczone podczas II wojny światowej. Ze względu na bardzo nietypowy charakter tego projektu i zachowywanie wszystkich wyników w ścisłej tajemnicy, nie przyczyniło się to jednak do rozwoju membran przemysłowych. Dopiero dalszy rozwój technologii membranowych sprawił, że w 1980 r. amerykańska firma chemiczna Monsanto wyprodukowała i wypuściła na rynek pierwsze na świecie membrany do separacji gazów. Ich przeznaczeniem było wydzielanie wodoru. Ponieważ pozwalały one ograniczyć straty tego gazu podczas różnych procesów (m.in. przy produkcji amoniaku), wkrótce firma odniosła komercyjny sukces, instalując kilkadziesiąt takich instalacji.
Dlaczego pierwsze rynkowe zastosowanie membran dotyczyło akurat wodoru? Wynika to z faktu, że cząsteczki tego gazu bardzo łatwo przenikają przez różne materiały. Z tego względu wytworzenie membran, które szybko przepuszczają wodór, a inne gazy wolno (nawet dwieście razy wolniej!), było łatwiejsze niż skonstruowanie membran do separacji innych gazów.
Jak to działa?
Dwoma podstawowymi parametrami opisującymi membranę są przepuszczalność i selektywność.
Pierwszy parametr mówi o tym, jak szybko membrana przepuszcza daną substancję. Drugi - jak dobrze rozdziela mieszaninę substancji.
Jak to się dzieje, że gazy czy ciecze mogą przenikać z jednej strony membrany na drugą i w jaki sposób zachodzi separacja? Najłatwiej jest zrozumieć, jak działają membrany filtracyjne. Funkcjonują one na zasadzie sita - w membranie filtracyjnej znajdują się pory (kanaliki) o określonej średnicy. Cząstki o rozmiarach mniejszych niż ta średnica mogą swobodnie przepływać przez kanaliki, natomiast cząstki większe są zatrzymywane. Tego typu membrany stosowane są np. do usuwania różnych mikroorganizmów z produktów spożywczych (np. mleka) i wody.
Membrany filtracyjne nie umożliwiają jednak rozdziału mieszanin związków chemicznych, ponieważ ich cząsteczki są tak małe, że wszystkie przepływają swobodnie przez pory i żadne nie są zatrzymywane. Aby był możliwy rozdział różnych związków chemicznych, membrana nie może mieć porów, a przenikanie substancji musi odbywać się na zasadzie dyfuzji pomiędzy molekułami tworzącymi membranę. Gdybyśmy zmniejszyli się do rozmiarów cząsteczek, to zobaczylibyśmy, że we wszystkich otaczających nas przedmiotach jest dużo pustych przestrzeni. Dzieje się tak dlatego, ponieważ molekuły zazwyczaj nie znajdują się jedna tuż obok drugiej, ale w pewnych odległościach od siebie. Dodatkowo drgania termiczne, które wykonuje każda molekuła, powodują zwiększenie tych odległości. W materiałach membranowych te puste przestrzenie są na tyle duże, że cząsteczki gazów czy cieczy mogą w nie wnikać, a potem przemieszczać się, wykonując tzw. skoki dyfuzyjne z jednego pustego obszaru do drugiego. I tym sposobem, wykonując miliardy skoków dyfuzyjnych, cząsteczka przenika z jednej strony membrany na drugą. Jedne poruszają się szybciej, inne wolniej i to umożliwia ich rozdzielenie.
Można się jednak domyślać, że taka „wędrówka” molekuł musi trwać dosyć długo. I rzeczywiście, dzieje się tak nawet w dobrze przepuszczalnych polimerach, z których wytwarza się membrany. A do zastosowań przemysłowych konieczne jest, by rozdzielanie zachodziło z odpowiednio dużą prędkością. Jak to pogodzić?
Poradzono sobie z tym na dwa sposoby: stosując bardzo cienkie membrany (cieńsze niż 1 mikrometr) - żeby droga, którą molekuły muszą pokonać, nie była długa - oraz wytwarzając membrany o bardzo dużej powierzchni. Membrany przemysłowe mają nawet kilka tysięcy metrów kwadratowych powierzchni, ale są tak upakowane, że mieszczą się w niewielkich obudowach.
Gdzie pracują membrany?
Obok wspomnianego wcześniej odzyskiwania wodoru obecnie najczęstszym zastosowaniem membran jest wydzielanie azotu z powietrza. Metoda ta pozwala otrzymywać azot o wysokiej czystości z szybkością nawet do 6 tys. m3/h! Azot jest używany najczęściej do tworzenia atmosfery ochronnej wokół zbiorników i rurociągów z łatwopalnymi cieczami - w celu zapobiegania zapłonom i wybuchom, do których konieczna jest obecność tlenu. Tak ochraniane są np. łatwopalne ładunki statków, zbiorniki z paliwem w samolotach, szyby wiertnicze. Atmosferę azotu wytwarza się także w celu ochrony materiałów przed korozją oraz żywności przed zepsuciem.
Kolejnym bardzo ważnym zastosowaniem membran jest usuwanie dwutlenku węgla z gazu ziemnego. Jest to konieczne, ponieważ CO2 obniża wartość opałową gazu ziemnego oraz powoduje korozję rurociągów przesyłowych. Membrany stosuje się także do usuwania wody z różnych mediów (z powietrza, z rozpuszczalników organicznych) oraz do odzyskiwania cennych związków organicznych z roztworów wodnych. Ciekawostką jest użycie membran do wzbogacania powietrza w tlen, w celu ułatwienia oddychania pasażerom najwyżej położonej linii kolejowej na świecie, łączącej miejscowości w Chinach i Tybecie.
Membrany do separacji gazów i cieczy stosuje się również w Polsce. Obecnie trwają prace instalacyjne modułów membranowych w kopalni gazu ziemnego Kościan-Brońsko, należącej do PGNiG. Ich zadaniem będzie odzyskiwanie helu, który jest obecny w tamtejszych złożach. Ma to być jedna z niewielu takich instalacji na świecie. Innym przykładem jest instalacja membranowa w jednym z oddziałów PKN Orlen SA w Płocku, umożliwiająca odzysk 90% glikolu etylenowego, który inaczej byłby całkowicie tracony.
Jedną ze szczególnych odmian membranowej separacji jest hemodializa, czyli proces oczyszczania krwi u ludzi z poważnym uszkodzeniem nerek. Krew pacjenta podłączonego do dializatora pompuje się do środka włókien o półprzepuszczalnych ściankach, przez które usuwane są mocznik oraz inne toksyczne produkty przemiany materii, po czym oczyszczona krew powraca do krwioobiegu pacjenta. Z tej formy terapii korzysta obecnie ok. 2 mln ludzi na świecie. Hemodializa stanowi jedno z najstarszych zastosowań technik membranowych. W Polsce wykonano ją po raz pierwszy w 1958 r.
Przyszłość
Rozwojem membran zajmują się przede wszystkim inżynierowie w przemyśle, a także naukowcy w jednostkach badawczych i na uczelniach. Podobnie jak w przypadku innych dziedzin, te dwa światy - przemysłu i nauki - z jednej strony są sobie bardzo bliskie, a z drugiej odległe. Przykładem mogą być badania nad membranami do separacji gazów - pomimo że w publikacjach naukowych opisano wiele setek materiałów membranowych, to znakomita większość stosowanych obecnie rozwiązań przemysłowych opiera się o mniej niż dziesięć polimerów, w dodatku znanych już od pewnego czasu.
Co prawda zsyntezowano i zbadano już materiały o lepszych właściwościach separacyjnych, ale aby materiał odniósł sukces komercyjny, musi spełniać wiele warunków, co nie jest proste. Oprócz wysokiej zdolności separacyjnej musi być wytrzymały oraz, co równie ważne, niedrogi. Z drugiej strony, membrany produkowane obecnie są znacznie bardziej wydajne od egzemplarzy, które powstawały u początków tej technologii. Co więcej, omawiane techniki znajdują się w fazie intensywnego rozwoju i nie ulega wątpliwości, że ich zastosowanie będzie stale rosło. W początkowej fazie wdrażania są obecnie instalacje membranowe do odwadniania biopaliw oraz rozdziału gazowych mieszanin związków organicznych. W fazie badawczej zaś - materiały o bardzo obiecujących właściwościach separacyjnych, m.in. nowe materiały polimerowe, sieci metalo-organiczne, a także membrany grafenowe.
Piotr Kubica