Walec parowy część 1 maszyna parowa
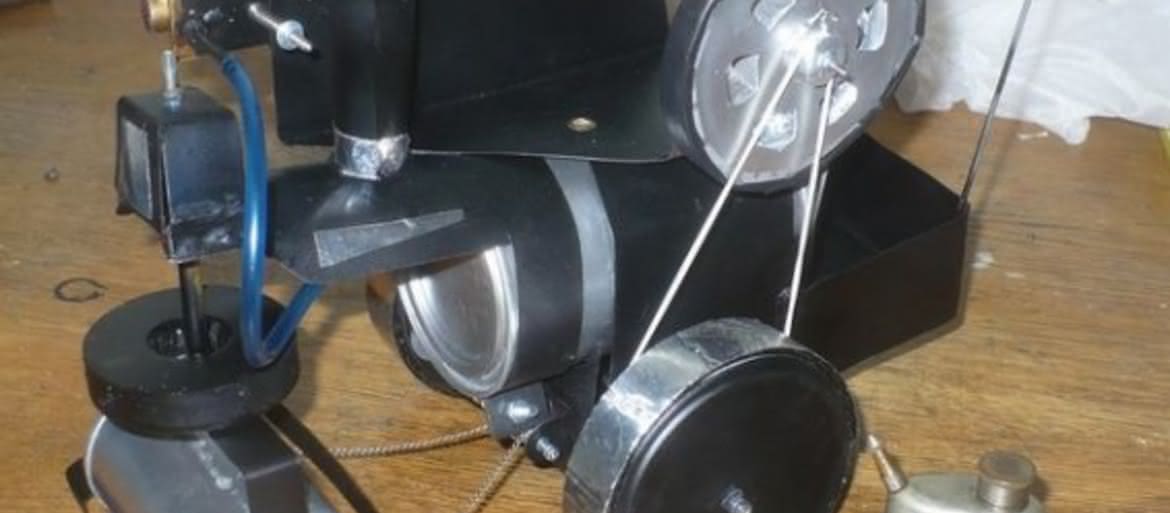
Model składa się z trzech podstawowych zespołów elementów. Najważniejsza to maszyna parowa z jej tłokiem, cylindrem i kołem zamachowym umieszczonym w stojanie. Już sama w sobie jest ciekawym urządzeniem. Uruchomiona na próbę, choćby powietrzem z domowej sprężarki da nam dużo satysfakcji i radości. Potem możemy przejść do dalszych elementów budowanego modelu. Druga część to kocioł zrobiony z puszki po czekoladzie wraz z blaszaną obudową, palnikiem i komorą spalania. Ostania, to układ kół jezdnych samego walca i pasowe przeniesienie napędu. Możemy zrobić także mechanizm skręcania walca za pomocą archaicznej metody przewijania łańcucha po ślimaku. Tak kiedyś kierowano samojezdnymi lokomobilami i właśnie parowymi walcami drogowymi. Trudność niesie zdobycie odpowiedniej przekładni zębatej, ale dla zdesperowanego majsterkowicza nie ma przeszkód, choćby miał budzik rozebrać.
Projekt walca drogowego jest trudny i będzie wymagał od nas zastosowania nowej umiejętności, do tej pory jeszcze nie opisywanej, czyli lutowania przy pomocy palnika. Nowością może być odlewanie tłoka z metalu. Z domu prawdopodobnie poginą słoiki po ogórkach a właściwie dekle od nich, rowerowe szprychy, blacha na parapety i stara teleskopowa antena radiowa, srebrny łańcuszek, sprężynki od długopisów jeszcze kilka innych rzeczy. W sklepie AVT, wydawcy MT, dostaniemy potrzebne komplety śrubek, podkładek i nakrętek, także tam można kupić przydatną przekładnię. Jeśli chcemy mieć model parowego walca lub lokomobili zabierajmy się do pracy.
Narzędzia: Wiertarka kolumnowa lub na statywie, koło z papierem ściernym zamocowanym do wiertarki, piła do metalu, duże nożyce do blachy, mały palnik do lutowania i topienia ołowiu, cyna, pasta lutownicza, rysik, punktak, narzynka M2 do gwintowania szprych, tradycyjna glutownica z klejem, nitownica do nitów oczkowych z niewielkim zapasem nitów. Do przeprowadzenia prób działania zmontowanej maszyny parowej będzie bardzo przydatna sprężarka.
Materiały: Puszka na kocioł parowy o wymiarach 110 długości na 70 milimetrów średnicy, którą daje się otwierać i zamykać deklem, blacha pół milimetrowej grubości, taka jak do budowlanych obróbek blacharskich, blacha karbowana z puszki na daszek pojazdu, pięć dużych dekli od słoików i jeden mniejszy, szprychy ze starego koła od roweru, blacha miedziana, rurka mosiężna o średnicy 12 milimetrów, cienka rurka mosiężna o średnicy 3 milimetrów, kawałki mosiądzu, karton, ołów do odlania tłoka, może to być trochę śrutu do wiatrówki, deska, łańcuszek o drobnych oczkach do mechanizmu kierowniczego, dwie sprężynki od długopisu, cienka rurka igielitowa, duża gumka jaką opakowują warzywa, taśma aluminiowa samoprzylepna, paliwo turystyczne w kostkach, drobne śrubki M2 i M3, nity oczkowe, silikon wysokotemperaturowy Tytan, a na koniec lakiery w sprayu chromowy i czarny matowy.
Cylinder. Cylinder zrobimy z rurki mosiężnej o długości 60 milimetrów. Średnica wewnętrzna 10 milimetrów a zewnętrzna 12 milimetrów. Rurka może być cieńsza, ale wtedy należy do niej odpowiednio dostosować wymiary. Z blachy miedzianej o grubości 0,5 milimetra wycinamy kółko o średnicy 12 milimetrów. Będzie ono deklem czyli tylną ścianką zamykającą cylinder. Tłok. Tą część odlejemy sobie sami z ołowiu. W niewielkim klocku drewnianym, centralnie wiercimy przelotowy otworek o średnicy takiej, jak posiadana szprycha czyli 2 milimetry. Traktując ten otworek jako pilota wiercimy drugi otwór wiertłem o średnicy 12 milimetrów ale zagłębiając się w klocek na około 8 milimetrów. Od spodu przekładamy drut szprychy rowerowej gwintem do góry tak by wystawał około 10 milimetrów ponad deskę.
Do wiercenia otworów powinniśmy użyć wiertarki na kolumnie, aby były one prostopadłe do powierzchni klocka. W szerszy otwór wstawiamy wysmarowaną oliwą od środka rurkę cylindra. Za pomocą palnika topimy ołów. Jako tygla można użyć pokrywki od puszki, takiej jak po paście do butów. Należy w niej wygiąć dziubek, który ułatwi nam wylewanie roztopionego metalu. Roztopiony ołów wlewamy do formy czyli rurki cylindra. Odczekajmy dłuższą chwilę, aż metal ostygnie. Zaraz potem możemy podnieść rurkę zobaczymy, że dysponujemy tłokiem pasującym idealnie do cylindra i do tego trwale osadzonym na tłoczysku, czyli drucie ze szprychy. Jeśli zatkamy palcem tylny otwór cylindra i poruszymy tłokiem powinniśmy czuć zmieniające się we wnętrzu cylindra ciśnienie. Tłok odlany w taki sposób z pewnością jest wystarczająco szczelny, by potem pracować w maszynie.
Mechanizm rozrządu. Z kawałka mosiądzu o wymiarach 25x10x6 milimetrów wypiłowujemy kształt jak na rysunku 1. Wiercimy w nim dwa otwory. Pierwszy ma 3 milimetry średnicy a drugi 1 milimetr. Do większego wlutujemy śrubę M3, która stanie się osią obrotu cylindra. Przez mniejszy 1 milimetrowej średnicy na zmianę będzie dostawała się para z kotła i potem z niej ulatywała. Gładź oraz tylną okrągłą ściankę przylutujemy do cylindra tak jak jest to widoczne na zdjęciach. Do otworu wlutowujemy śrubę M3. Teraz pora na dodatkowe wiercenie otworu 1 milimetrowego tak, by dowiercić się do wnętrza cylindra, bo w przeciwnym razie para nie miałaby jak dostać się do środka cylindra, by poruszać tłok.
Koło zamachowe. Zrobimy je z dekla od słoika. Do środka włożymy wieniec, czyli duże ciężkie kółko o średnicy 75 milimetrów. Takie kółko, jak na zdjęciu kupicie w GS-ie albo sklepie narzędziowym. Albo po prostu poszukajcie podobnego kółka w domowych zapasach. Jeszcze prościej można zrobić koło zamachowe napełniając dekiel gipsem.
Oś koła zamachowego. Zrobiona jest ze szprychy. Odcinamy kawałek o długości 110 milimetrów. Koło będzie od tej strony gdzie jest gwint. Do drugiego końca przylutujemy korbowód. Oś gwintujemy za pomocą narzynki M2, ponieważ koło zamocujemy za pomocą nakrętek i przeciw nakrętek. Musi się obracać razem z osią i korbowodem. Gwintowanie przeprowadza się w ten sposób, że na mocno zamocowany w imadle drut nakręca się narzynkę w uchwycie. Koniec drutu powinien być lekko sfazowany pilnikiem. Gdy narzynka załapie, robi się jeden obrót w prawo a potem jedną trzecią w lewo. W ten sposób zrywa się skrawane wióry i narzynka nam podczas pracy nie pęknie. To bardzo istotna uwaga. Już po chwili możemy się cieszyć zrobionym własnoręcznie wspaniałym gwintem.
Stojan maszyny. Wytniemy z blachy o grubości pół milimetra. Najpierw narysujmy jego kształt w skali 1:1 na kartonie. Wymiary podaję na rysunku. Dopiero od takiego szablonu trasujemy stojan na blasze. Po wycięciu blachę obrabiamy papierem ściernym zaokrąglając wszystkie rogi i wygładzając brzegi. To dotyczy wszystkich elementów wycinanych z blachy. Do tego radzę ciąć szlifować i w ogóle pracować w warsztatowych rękawicach. Mnie niejednokrotnie uratowały od skaleczenia. W miejscach pokazanych na rysunku, wiercimy dwa otwory o średnicy 2,5 milimetra. Wyginanie blachy przeprowadzamy za pomocą kombinerek w imadle, pomagając sobie młotkiem. Co zrobić jeśli blacha jest dłuższa niż szczęki imadła, a nie mamy krawędziarki, czyli specjalnej maszyny do wyginania blachy? A tak jest w przypadku kształtowania blachy na stojan. Możemy poradzić sobie w taki sposób jak na zdjęciu. W desce, od jej czoła, wysinamy szczelinę. Do niej wkładamy blachę i robimy odpowiednie zagięcie pomagając sobie młotkiem.
Korbowód i korba. Wytniemy z blachy miedzianej w kształcie jak na rysunku. Przylutujemy go do osi koła zamachowego. Do drugiego otworu wlutujemy trzpień w który trafi korba. W korbie wiercimy otwór o średnicy 2 milimetry w który trafi trzpień korbowodu. Na rysunku widoczny jest tłok oraz korbowód.
Druga gładź. Do stojana przylutujemy mosiężną płytkę będącą drugą częścią gładzi maszyny. Płytka ma wymiary 40x20x2 milimetrów. W płytce wiercimy trzy otwory wlotowy o średnicy 1 milimetr i wylotowy o średnicy 2 milimetrów pary oraz ten przez który przechodzi oś obrotu cylindra (średnicy 3 milimetrów). Zaczniemy od otworu 3 milimetrowego. Pozycji otworów wlotowego i wylotowego jeszcze nie znamy ponieważ wyznaczy ją cylinder zamontowany na korbowodzie.
Wstępny montaż maszyny parowej. Przez otwory w stojanie przekładamy szprychę z zamontowanym do niej korbowodem. Z drugiej strony tej osi za pomocą nakrętek M2 oraz przeciw nakrętki mocujemy koło zamachowe. Cylinder z tłokiem umieszczamy w otworze płytki rozrządu. Na śrubę M3 zakładamy sprężynkę od długopisu i mocujemy śrubką. Nie zapomnijmy podłożyć pod nią podkładki. Ta sprężynka dociska obie gładzie do siebie, nie pozwalając parze uciekać na boki. Z drugiej strony łączymy za pomocą nakrętki i kontr nakrętki korbowód. Gdy obracamy koło zamachowe cylinder powinien wykonywać ruch wahliwy na swojej osi.
Zaznaczamy jego skrajne położenia i na gładzi odnajdujemy miejsce gdzie powinny znajdować się otwory wlotowy pary i wylotowy. Wylotowy powinien mieć 2 milimetry a wlotowy 1 milimetr średnicy. Ja pomogłem sobie odrysowując na papierze płaską płytkę cylindra i otworek przelotowy. Znając położenie osi i skrajne położenia cylindra można napunktować poszukiwane miejsca a następnie wywiercić potrzebne otwory. Z drugiej strony gładzi do płytki przylutujemy rurkę mosiężną którą będzie doprowadzana para z kotła.
Gdyby cyna zalała otworek należy go udrożnić, czyli nawiercić jeszcze raz. Chwilowo montujemy maszynę na drewnianym klocku. Badamy, czy koło obraca się bez oporów i czy otwory wlotowy i wylotowy trafiają na otworek cylindra. Z pewnością wszystko będzie wymagało regulacji. Także koło może wymagać wyważenia. Poradzimy sobie z tym, za pomocą kilku rozpłaszczonych młotkiem ołowianych śrucin. Przykleimy je klejem z glutownicy do obwodu koła w miejscu przeciwnym do tego w którym koło uparcie zatrzymuje się a które sobie określimy jako najcięższe. Trochę cierpliwości i wszystko powinno się udać. Koło powinno zatrzymywać losowo się za każdym razem w innym miejscu. Celem ostatecznego testu działania maszyny parowej możemy podłączyć ją do sprężarki. Sprężone powietrze zastąpi chwilowo parę wodną i będziemy mogli naocznie sprawdzić czy maszyna jest prawidłowo zmontowana i czy działa.