Beton, stal, plastik - co zrobić z materiałami rewolucji przemysłowej? Inaczej produkować, lepiej utylizować, czy to możliwe?
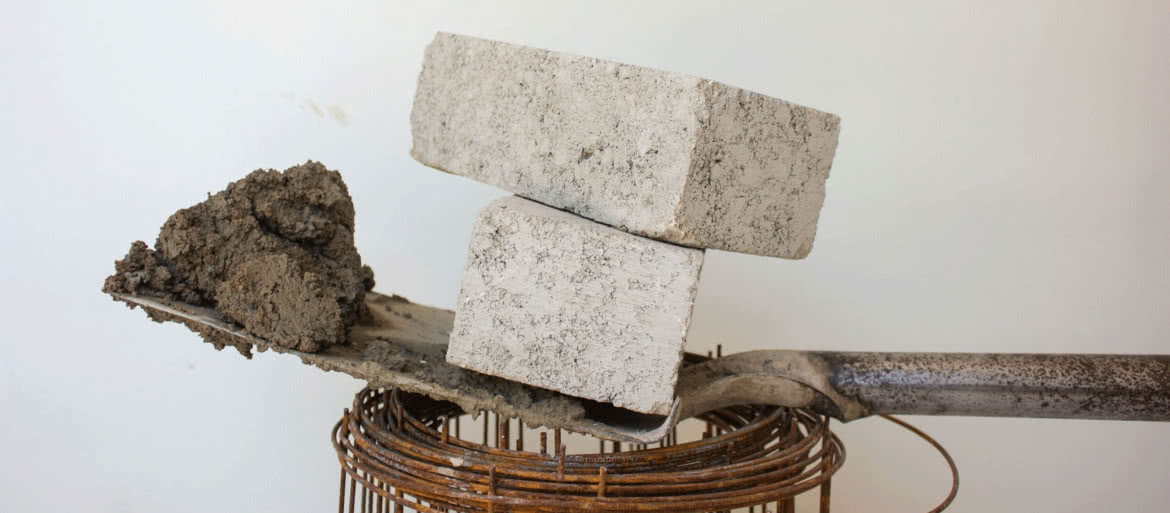
Beton (1) jest drugą najpowszechniej używaną substancją na świecie, zaraz po wodzie. To najważniejszy materiał budowlany, jakim się dzisiaj posługujemy. Jest kompozytem składającym się z kilku prostych składników, piasku, kruszywa (zwykle żwiru lub kamieni) i wody, zmieszanych ze spoiwem na bazie wapna (cementem). Materiał ten, w różniących się szczegółami wersjach, był wykorzystywany już przed naszą erą.
Beton jest zatem prosty w produkcji, tani, a do tego bardzo wytrzymały. Dlatego zyskał popularność, np. w okresie po drugiej wojnie światowej, dzięki niemu możliwa była szybka i stosunkowo niedroga odbudowa zrujnowanych bombardowaniami miast. Dzisiaj jest wykorzystywany z nie mniejszym natężeniem. Zaspokaja wszakże potrzeby rosnącej populacji ludzkiej.
W czym zatem problem? Piasku nam przecież na świecie nie brakuje. Czy może jednak brakuje? Pisaliśmy o tym zresztą niedawno w MT, zwracając uwagę, że z piaskiem na świecie jednak jest pewien problem. I narasta. Piasek na cele budowlane wydobywa się najczęściej z dna zbiorników i cieków wodnych. Taka praktyka pozbawia zwierzęta ich siedlisk i narusza naturalne procesy oczyszczania się i przepływu wód, co z kolei powoduje pogorszenie jej jakości i dalszą degradację środowiska.
W Chinach, dla przykładu, zapotrzebowanie na beton jest tak duże, że piasek w tonach pozyskiwany jest z niezwykle cennych przyrodniczo obszarów (np. jeziora Poyang). Biorąc pod uwagę fakt, że Chiny w ciągu trzech lat wylały więcej betonu niż Stany Zjednoczone w całym ubiegłym wieku, wydobycie piasku przestaje być drobnym, lokalnym problemem, a coraz częściej przybiera formę kryzysu ekologicznego.
Ale piasek to dopiero początek. Ogólne koszty ekologiczne przemysłu cementowego są oceniane jako ogromne. Jak oceniał w 2020 r. "The Guardian", gdyby przemysł cementowy był krajem, byłby trzecim co do wielkości emitentem dwutlenku węgla na świecie z emisją do 2,8 mld ton rocznie, ustępując miejsca jedynie Chinom i USA. Wśród materiałów więcej gazów cieplarnianych emitują tylko paliwa kopalne.
Zagrożenia środowiskowe stwarza wydobycie wapienia, z którego pozyskuje się wapno niezbędne do produkcji cementu. Także wytwarzanie kruszywa jest procesem środowiskowo obciążającym (2). Produkcja betonu generalnie zużywa duże ilości wody. Może to potencjalnie wpływać na dostępność wody powierzchniowej i gruntowej. Największym problemem są zrzuty ścieków z cementowni do lokalnych zbiorników wodnych.
Mielenie i spiekanie surowców mineralnych (np. wspomnianego wcześniej wapienia) na klinkier, z którego powstaje cement, wymaga dużych nakładów energii pochodzącej w zdecydowanej większości z paliw kopalnych. Do wypalania wapieni w piecach cementowych i powstania klinkieru cementowego potrzeba wysokich, w niektórych przypadkach przekraczających tysiąc stopni Celsjusza temperatur. Klinkier jest mielony na proszek i mieszany z innymi skład mieszany z kruszywem, głównie żwirem i piaskiem, w celu uzyskania betonu, który jest wzmacniany stalą w celu stworzenia budynków i konstrukcji.
Według Międzynarodowej Agencji Energii, sektor cementowy jest trzecim co do wielkości przemysłowym konsumentem energii na świecie. Jest również drugim co do wielkości przemysłowym emitentem dwutlenku węgla, odpowiedzialnym za siedem procent globalnej emisji. Globalna produkcja cementu może wzrosnąć 23% do 2050 roku, uważa organizacja Mission Possible Partnership. Jednocześnie przemysł cementowy ma zmniejszyć swoje roczne emisje o co najmniej 16% do 2030 roku, aby spełnić standardy Porozumienia Paryskiego w sprawie zmian klimatu.
Beton na bakteriach lub z recyklingu
Jak zmniejszyć ślad ekologiczny betonu? Oprócz rozwiązań takich, jak urządzenia wychwytujące CO2 czy zamiana paliw kopalnych na alternatywne źródła energii, naukowcy proponują rozwiązanie problemu jego źródła, czyli w procesie produkcji cementu. Chodzi o nowe, mniej obciążające składniki i procesy technologiczne.
Przykładem takiego nowatorskiego cementu jest biocement opatentowany przez firmę bio-MASON (3). Zamiast energochłonnego spalania materiału na cement, pomysłodawcy postanowili stworzyć go w temperaturze pokojowej za pomoc bakterii. Drobnoustroje "karmione" w systemie hydroponicznym formują cement, nadając mu odpowiednią wytrzymałość, bez wysokiej temperatury i kosztów środowiskowych. W innym projekcie zespół inżynierów z Uniwersytetu Boulder w Kolorado opracował sposób na stworzenie zrównoważonego betonu poprzez dodanie do mieszanki żywych organizmów. Kluczowym składnikiem są mikroalgi, kokkolitofory. Te małe organizmy pokryte są mikroskopijnymi płytkami z węglanu wapnia, który w tym procesie jest niejako "hodowany". W 2019 roku naukowcy z Tajwanu i Indii odkryli, że naturalne odpady z rolnictwa i akwakultury mogą częściowo zastąpić składniki i materiały wiążące w ekobetonie.
Nowy przykład bioalternatywy dla cementu pochodzi z Uniwersytetu Tokijskiego. Kota Machida i Yuya Sakai stworzyli cement z odpadów spożywczych. Odpady spożywcze były już wcześniej wykorzystywane jako wypełniacz w alternatywnych cementach, ale to pierwszy na świecie proces produkcji cementu wyłącznie z odpadów spożywczych.
Wykorzystali liście herbaty, skórki pomarańczy i cebuli, fusy z kawy, kapustę pekińską, a nawet resztki z pudełek na posiłki. Udało im się znaleźć odpowiednią kombinację temperatury i ciśnienia, która pozwoliła na wytworzenie cementu z samych odpadów żywnościowych bez dodatków. Używając techniki "prasowania na ciepło", zwykle używanej do produkcji materiałów budowlanych z proszku drzewnego, zmieszali proszek z odpadów spożywczych z wodą i wcisnęli go do formy podgrzanej do 177 stopni Celsjusza. Badacze mówią, że wytrzymałość na rozciąganie lub zginanie cementu jest ponad trzykrotnie większa niż zwykłego betonu.
Inni badacze za najbardziej obiecującą strategię ograniczania emisji CO2 uważają ponowne wykorzystanie. Recyklingowany może być sam beton pochodzący ze zburzonych konstrukcji - rozdrobniony i wmieszany w nowy beton jako kruszywo. Ponownie wykorzystane mogą zostać także inne odpady. W środowiskach akademickich dużym zainteresowaniem cieszy się ostatnio beton z plastikiem zamiast piasku, co jest sposobem również na odpady z tworzywa sztucznego, do czego wrócimy. W 2021 roku naukowcy z uniwersytetu w Tokio opracowali proces wytwarzania betonu z użyciem starych produktów betonowych, który wymaga niższych temperatur. Istnieje wiele innych alternatyw o podobnym charakterze, jednak wszystkie te innowacje są na wczesnym etapie rozwoju.
Jednym z pomysłów jest to, co proponują inżynierowie z uniwersytetu w Cambridge, twierdzący, że wynaleźli "pierwszy na świecie cement o zerowej emisji", który nazwali Cambridge Electric Cement. Zespół Brytyjczyków zauważył, że zużyty cement oddzielony od betonu z recyklingu był praktycznie identyczny z topnikiem wapiennym używanym do usuwania zanieczyszczeń ze stali zarówno w elektrycznych piecach łukowych, jak i w wielkich piecach, który unosi się na wierzchu stopionej stali, aby chronić ją przed utlenianiem. Kończy jako żużel, zwykle uważany za produkt odpadowy. Jednak jest pełen tlenku wapnia, kluczowego składnika klinkieru używanego do produkcji cementu. Badacze z Cambridge zmielili żużel na proszek, twierdząc, że jest on praktycznie identyczny z klinkierem, podstawą cementu portlandzkiego.
Z kolei naukowcy z Uniwersytetu Marcina Lutra w Niemczech i brazylijskiego uniwersytetu w Pará opracowali niskoemisyjną alternatywę dla konwencjonalnego cementu używającą niewykorzystywanego wcześniej nadkładu z kopalni boksytów. Okazało się, że alternatywa jest tak samo stabilna jak tradycyjny cement portlandzki. Wyniki badań opublikowano w czasopiśmie "Sustainable Materials and Technologies".
Stosowanie alternatywnych cementów w betonie do bardziej skomplikowanych i wymagających konstrukcji budowlanych wymagałoby wielu testów bezpieczeństwa i trwałości. Organizacje regulujące przemysł i sami wykonawcy musieliby być przekonani o jego opłacalności. W przypadku dużych projektów budowlanych wykonawcy wybierają wciąż najbardziej ekonomiczne rozwiązania.
Wodór zamiast koksu, czyli wizja bezemisyjnej stali
Stal, niezbędna w inżynierii i budownictwie, jest jednym z najpopularniejszych materiałów przemysłowych na świecie. Rocznie produkuje się jej ponad dwa miliardy ton. Ta obfitość ma jednak wysoką cenę dla środowiska. Produkcja stali odpowiada za 7–11% światowej emisji gazów cieplarnianych, co czyni ją jednym z największych przemysłowych źródeł zanieczyszczenia atmosfery. A ponieważ produkcja może wzrosnąć o jedną trzecią do 2050 roku, to obciążenie środowiska może się zwiększyć. Aby sprostać międzynarodowym celom klimatycznym, emisje ze stali i innych gałęzi przemysłu ciężkiego będą musiały spaść o 93% do 2050 roku. Tak szacuje Międzynarodowa Agencja Energii.
W obliczu rosnącej presji ze strony rządów i inwestorów wielu producentów stali, jak i startupy, eksperymentują z rozwiązaniami niskoemisyjnymi, które wykorzystują wodór lub energię elektryczną zamiast jednak zgadzają się, że przejście na nowe techniki w tej branży będzie bardzo trudne.
70% światowej stali produkuje się metodami wielkopiecowymi, opartymi głównie na technice Bessemera jeszcze z XIX wieku. Wytwarza się w ten sposób prawie dwie tony dwutlenku węgla na każdą tonę wyprodukowanej stali. Pozostałe 30% jest wytwarzane w elektrycznych piecach łukowych (4), które wykorzystują prąd elektryczny do topienia stali - w tym przypadku w dużej mierze pochodzącej z recyklingu złomu, co oznacza znacznie niższą emisję CO2 niż w wielkich piecach. Jednak ze względu na ograniczoną podaż złomu, nie cały obecny i przyszły popyt może zostać zaspokojony w ten sposób. Przy odpowiedniej polityce recykling mógłby zaspokoić do 45% globalnego zapotrzebowania w 2050 roku. Reszta to będzie wciąż tradycyjny wytop oparty na rudach.
Boston Metal, firma, która dekadę temu wyłoniła się z MIT, ma nadzieję radykalnie zmienić branżę wytopu stali. Stawiając na energię elektryczną do procesu oddzielenia żelaza od rudy, firma twierdzi, że może produkować stal bez emisji dwutlenku węgla. Boston Metal opracował proces zwany elektrolizą stopionego tlenku, w którym prąd przepływa przez ogniwo zawierające rudę żelaza. Gdy prąd przepływa pomiędzy oboma końcami ogniwa i podgrzewa rudę, wydziela się tlen, a ruda żelaza jest redukowana do płynnego żelaza. Oczyszczone żelazo jest następnie mieszane z węglem i innymi składnikami. Jeśli energia elektryczna pochodzi ze źródeł wolnych od kopalin, to proces rzeczywiście nie generuje żadnych emisji dwutlenku węgla.
Kolejna z testowanych alternatywnych technologii zastępuje koks wodorem. W Szwecji projekt Hybrit pilotuje proces, który wykorzystuje wodór w miejsce koksu do ekstrakcji tlenu z rudy żelaza, pozostawiając porowate granulki żelaza zwane żelazem gąbczastym. Wodór ma docelowo być tzw. zielonym wodorem, czyli ma być pozyskiwany w sposób nieemisyjny. W procesie tym produktem ubocznym jest jedynie para wodna. Firma ma już zakład eksperymentalny (5) i planuje budowę zakładu do produkcji na skalę komercyjną, którą zamierza zakończyć do 2026 r.
Jednak na razie wodór jest znacznie droższy niż większość paliw, więc ekonomia tego rozwiązania nie kusi. Inne szwedzkie przedsięwzięcie wodorowe, H2 Green Steel, buduje zakład produkcyjny stali wodorowej na skalę komercyjną z pomocą środków pozyskanych od prywatnych inwestorów i firm, w tym firm Mercedes-Benz i Scania. Firma planuje rozpocząć produkcję do 2024 r. i do końca dekady wytwarzać 5 mln ton bezemisyjnej stali rocznie.
Przed innowatorami chcącymi zmienić oblicze przemysłu stalowego wciąż jest mnóstwo poważnych wyzwań. Głównym z nich jest ogromna rozbudowa infrastruktury energii odnawialnej zgodnie z wymaganiami tej wielkiej, ciężkiej i energochłonnej branży. Szacuje się, że do elektryfikacji istniejącej produkcji stali pierwotnej świat potrzebowałby nawet trzykrotnie więcej niż obecnie zainstalowanych źródeł energii słonecznej i wiatrowej. Kolejną barierą są koszty. Przejście na energię elektryczną lub wodór wymagałoby ogromnych nakładów kapitałowych na budowę nowych i modernizację starych zakładów.
W przypadku metody czystego wodoru cena stali wzrośnie z powodu ceny wodoru, także z tego względu, że jej huty są zlokalizowane zwykle w pobliżu zasobów taniego węgla koksującego, a nie tanich źródeł wodoru.
Albo coś zrobimy z plastikiem, albo on coś zrobi nam
Trzeci fundamentalny materiał zbudowanej w XX wieku cywilizacji technicznej to tworzywa sztuczne (6). W tym przypadku, gdy mówi się o środowiskowych kosztach, to częściej niż kwestie wytwarzania porusza się problem odpadów i ich utylizacji. W 2050 r. w oceanach masa plastikowych odpadów, w tym, uznawanych za jeszcze niebezpieczniejsze niż butelki i torebki, mikroodpadów, prześcignie łączną masę ryb - takie ostrzeżenie znalazło się w raporcie fundacji Ellen MacArthur i firmy McKinsey, opublikowanym przy okazji Światowego Forum Ekonomicznego w Davos, w 2016 r. Uczeni, autorzy raportu zwracają uwagę, że jedynie 14% plastikowych opakowań jest recyklingowanych. W przypadku innych materiałów wskaźnik recyklingu jest znacznie wyższy - odzyskuje się np. 58% papieru i do 90% metali.
Istnieje około dwudziestu powszechnie stosowanych różnych rodzajów tworzyw sztucznych. Każdy z nich występuje w licznych odmianach, co pomaga wybrać dany materiał najbardziej odpowiedni do określonego zastosowania. Wyróżnia się pięć (lub sześć) grup tworzyw wielkotonażowych: polietylen (PE, w tym - wysokiej i niskiej gęstości, HD i LD), polipropylen (PP), polichlorek winylu (PVC), polistyren (PS) oraz politereftalan etylenu (PET). Materiały z tych grup zaspokajają blisko 75% europejskiego zapotrzebowania na wszystkie tworzywa sztuczne i stanowią największą grupę plastikowych odpadów zalegającą na wysypiskach komunalnych. Tworzywa z tej grupy stanowią dominującą grupę odpadów.
Utylizacja tych substancji przez spalanie na wolnym powietrzu nie jest w żadnym wypadku akceptowane zarówno przez specjalistów, jak i przez ogół społeczeństwa. Składowanie odpadów na wysypiskach nie jest aż tak toksyczne jak spalanie tych odpadów na wolnym powietrzu, ale obecnie w cywilizowanych krajach też nie jest już akceptowane. Nie jest wprawdzie prawdą, że "plastik jest wieczny", jednak biodegradacja polimerów trwa o wiele dłużej niż odpadków z jedzenia, papieru czy metali. Na tyle długo, że przy obecnym poziomie produkcji śmieci plastikowych, wynoszącym w Polsce ok. 70 kg na głowę rocznie, przy poziomie odzyskiwania, który niedawno ledwo przekroczył 10%, nasza górka tych śmieci osiągnęłaby 30 mln ton w ciągu kilkunastu lat.
Teoretycznie utylizacja odpadów z grupy tworzyw termoplastycznych jest stosunkowo prosta, gdyż mogą one być wielokrotnie przerabiane. Jednak w czasie powtórnego przetwórstwa następuje częściowa degradacja polimeru, której konsekwencją jest pogorszenie się właściwości mechanicznych wyrobu. Z tego powodu w procesie przetwórstwa dodaje się tylko pewną część surowca wtórnego. Znacznie większym problemem podczas utylizacji zużytych wyrobów z termoplastów jest konieczność ich sortowania pod względem asortymentu. Nie zawsze jest to opłacalne i możliwe.
Tworzywa z polimerów usieciowanych w zasadzie nie mogą być ponownie przetwarzane. Ich spalanie wydziela toksyczne substancje. Wydzielają się przede wszystkim chloroorganiczne związki aromatyczne, przewyższające toksycznością wielokrotnie cyjanek potasu, tlenki węglowodorów w postaci dioksanów - C4H8O2 i furanów - C4H4O przedostających się do atmosfery.
Znane są metody utylizacji tych odpadów w sposób nieemitujący zanieczyszczeń. To m.in. metody chemiczne, m.in. hydroliza - polegająca na rozłożeniu polimerów pod działaniem pary wodnej (surowce do ponownej produkcji poliestrów, poliamidów, poliuretanów i poliwęglanów) lub piroliza niskotemperaturowa, za pomocą której utylizuje się np. butelki PET i zużyte opony. Jednak jak łatwo się domyślić, nie są to metody tanie, także dlatego, że wymagają kosztownej segregacji.
W ostatnich latach pojawiło się sporo pomysłów na kreatywny recykling plastikowych odpadów; np. duńska studentka inżynierii Lise Fuglsang Vestergaard podczas pobytu w indyjskim mieście Joygopalpur w Indiach wpadła na pomysł wytwarzania cegieł z odpadów z tworzyw sztucznych. W tym samym kraju na dużą skalę dodaje się plastikowe odpady do mieszanek bitumicznych do budowy dróg. Martín Olazar, inżynier z Uniwersytetu Kraju Basków, wynalazł minirafinerię, która na zasadzie pirolizy materiałów wejściowych przerabia plastikowe odpady na biopaliwo zdane do wykorzystania w silnikach.
Pomimo nowych pomysłów i postępów technologii recyklingu, wciąż jednak tylko niewielki odsetek z setek milionów ton plastikowych odpadów produkowanych co roku na świecie trafia do recyklingu. Według badań fundacji Ellen MacArthur, tylko 15% opakowań trafia do pojemników segregujących, a zaledwie 5% jest poddawanych recyklingowi.
Wielu liczy, że z czasem wzrastać będzie znaczenie gospodarcze tworzyw "biodegradowalnych" materiałów nowej generacji, opartych np. o pochodne skrobi, kwasu polimlekowego albo nawet jedwab. Produkcja z tych materiałów jest wciąż stosunkowo droga, jak to zwykle bywa z nowatorskimi rozwiązaniami. Warto jednak je obserwować.
Jednym z najbardziej interesujących pomysłów w dziedzinie biodegradacji tworzyw sztucznych wykonanych m.in. z polietylenu, polipropylenu oraz polistyrenu wydaje się technologia oparta na zastosowaniu w ich produkcji różnego typu dodatków znanych pod symbolami d2w lub EPI. Od kilku lat w Polsce znany jest produkt d2w produkcji brytyjskiej firmy Symphony Environmental. Jest to dodatek do produkcji miękkich i półsztywnych tworzyw sztucznych, od których wymagamy szybkiej nieszkodliwej dla środowiska samodegradacji. Fachowo działanie d2w określa się jako oksybiodegradację tworzyw sztucznych. Proces ten oznacza rozpad tworzywa na wodę, dwutlenek węgla, biomasę oraz pierwiastki śladowe, bez innych pozostałości i bez wydzielania metanu. Proces degradacji tworzywa dzięki d2w skrócony został do nawet 60 dni.
Kolejny nurt badań to poszukiwanie mikroorganizmów lub egzymów, które skutecznie i wydajnie "pożerałyby" plastik. Instytut Technologiczny w Kioto odkrył parę lat temu, że istnieje bakteria powodująca rozkład tworzyw sztucznych. Nazwano ją Ideonella sakaiensis. Odkrycie zostało opisane w magazynie "Science". Bakterię odnaleziono w jednej z próbek pobranych z otoczenia zakładu przerabiającego butelki PET. Wchodziła ona w skład zespołu mikroorganizmów, który degradował powierzchnię błony z PET w tempie 130 µg/cm² na dobę w temperaturze 30°C. W celu uzyskania energii z PET bakteria najpierw hydrolizuje PET za pomocą enzymu o angielskiej nazwie PETase (hydrolaza PET) do kwasu mono(2-hydroksyetylo)tereftalowego (MHET), który potem w kolejnym kroku hydrolizuje przy użyciu enzymu o angielskiej nazwie MHETase (hydrolaza MHET) na monomery wyjściowego tworzywa sztucznego: glikol etylenowy i kwas tereftalowy.
Te związki chemiczne bakterie potrafią wykorzystać bezpośrednio do produkcji energii. Niestety, na rozłożenie cienkiego kawałka tworzywa sztucznego cała kolonia Ideonella sakaiensis potrzebuje aż sześciu tygodni i odpowiednich warunków (temperatura musi wynosić 30 stopni Celsjusza).
Grupa naukowców z University of Texas w Austin w maju 2022 roku poinformowała o stworzeniu zmodyfikowanego enzymu, który potrafi w ciągu kilku dni rozłożyć plastik, którego degradacja w innym przypadku trwałaby wieki. Badacze, którzy opublikowali swoje odkrycia w "Nature", użyli uczenia maszynowego w celu odnalezienie białka, które może szybko rozłożyć bloki budulcowe politereftalanu etylenu (PET). Czyni to poprzez proces zwany depolimeryzacją, w którym katalizator rozdziela bloki budulcowe tworzące PET na ich oryginalne monomery, które następnie mogą być ponownie spolimeryzowane i przekształcone w inne produkty. Co istotne, enzymy rozłożyły plastik w ciągu jednego tygodnia. Naukowcy nazwali enzym FAST-PETase, co jest skrótem terminu - "funkcjonalna, aktywna, stabilna i tolerancyjna PETaza". Mają nadzieję, że uda się go wytwarzać i stosować na wielką skalę.
To właśnie odpowiednia duża skala, wydajność i opłacalność są słowami kluczami do wszelkich rozwiązań ekoproblemów z betonem, stalą i plastikiem. Na razie trudno mówić o przełomach, jeśli chodzi nadanie tym fundamentalnym materiałom bardziej zielonego koloru. Warto jednak obserwować wysiłki uczonych i poszukiwania.
Mirosław Usidus