Co by tu jeszcze zautomatyzować?
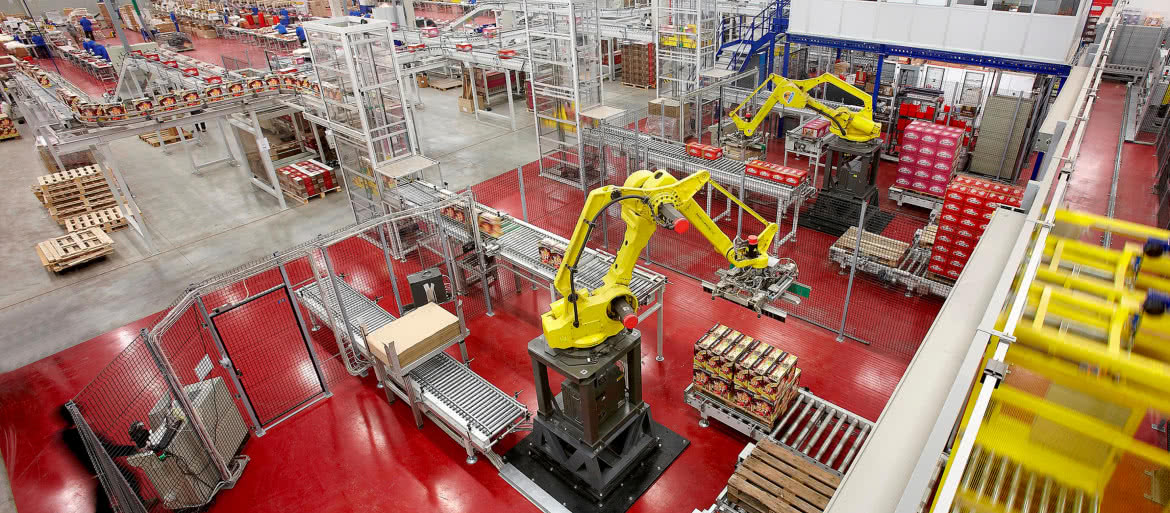
Obecnie do najbardziej dynamicznych startupów należą takie firmy jak dubajski LogSquare, dostawca rozwiązań automatyzujących transport, logistykę i magazynowanie. Kluczowym komponentem w ofercie LogSquare jest rozwiązanie automatycznego składowania i pobierania towaru, zaprojektowane tak, aby zminimalizować wykorzystanie przestrzeni w magazynie i uzyskać wyższy poziom wydajności i produktywności.
Szefowie firmy mówią o swojej ofercie "miękka automatyzacja" (1). Wiele firm pomimo presji, jaką wywołała pandemia koronawirusa, wciąż nie jest gotowych na radykalne działania, więc rozwiązania LogSquare, automatyzowania drogą drobnych ulepszeń i racjonalizacji, jest dla nich atrakcyjna.
Kiedy wyjście poza "strefy komfortu"?
Automatyzacja to m.in. planowanie i prognozowanie. Algorytmy uczenia maszynowego można zaprogramować tak, aby analizowały dane statystyczne, uwzględniały informacje historyczne i środowiskowe, a następnie umożliwiały wgląd we wzorce lub tendencje. To również lepsze zarządzanie rezerwami i zapasami. A także wykorzystanie pojazdów autonomicznych. Systemy AI zasilane stałym strumieniem danych na bieżąco za pomocą najnowocześniejszych technologii sieciowych, takich jak 5G, zapewnią pojazdom i maszynom, np. pojazdom autonomicznym, samodzielność w podejmowaniu decyzji.
Wielkie firmy górnicze, takie jak Rio Tinto i BHP Billington, od kilku lat inwestują w tym obszarze, automatyzując używane przez siebie ciężarówki i ciężki sprzęt (2). Może to przynieść wiele korzyści - nie tylko jeśli chodzi o koszty zatrudnienia, ale również przez zmniejszenie częstotliwości konserwacji pojazdów i podniesienie standardów bezpieczeństwa i higieny pracy. Jednak działa to na razie jedynie w strefach ściśle kontrolowanych. Gdy pojazdy autonomiczne są zabierane poza owe strefy komfortu, kwestia ich sprawnego i bezpiecznego działania ogromnie się komplikuje. Ostatecznie jednak będą musiały wyjść do świata zewnętrznego, radzić sobie i pracować z zachowaniem bezpieczeństwa.
Robotyzacja przemysłu to nie wszystko. Analizy grupy MPI wskazują, że prawie jedna trzecia procesów i urządzeń produkcyjnych oraz procesów i urządzeń nieprodukcyjnych zawiera już inteligentne urządzenia/wbudowaną inteligencję. Według firmy konsultingowej McKinsey & Company, dzięki powszechnemu zastosowaniu technologii konserwacji prognostycznej można zmniejszyć koszty utrzymania ruchu w firmach o 20 proc., ograniczyć nieplanowane przestoje o 50 proc., wydłużając żywotność maszyn o lata. Programy konserwacji prognostycznej monitorują urządzenia za pomocą dowolnej liczby mierników wydajności.
Zakup robotów bezpośrednio może być kosztownym przedsięwzięciem. Jak wspominamy na początku artykułu, pojawia się nowa fala usług oferujących robotykę jako usługę. Koncepcja polega na wynajęciu robotów po obniżonej stawce zamiast ich kupowania na własność. W ten sposób można szybko i skutecznie wdrażać roboty, nie ryzykując ogromnych nakładów inwestycyjnych. Istnieją również firmy oferujące rozwiązania modułowe, które pozwalają producentom wydawać tylko tyle, ile potrzebują. Firmy oferujące takie rozwiązania to m.in.: ABB Ltd. Fanuc Corp, Sterraclimb.
Automat w domu i zagrodzie
Obszarem, któremu wróży się szybkie zawojowanie przez automatyzację, jest produkcja rolna. Zautomatyzowane narzędzia rolnicze mogą pracować godzinami bez odpoczynku i są już stosowane w wielu obszarach agrobiznesu (3). Są przewidywania, że postępy w zautomatyzowanym rolnictwie, zwłaszcza w krajach rozwijających się, będą miały w dłuższej perspektywie największy globalny wpływ na siłę roboczą, większy niż w przemyśle.
Automatyzacja w rolnictwie to po pierwsze oprogramowanie do zarządzania gospodarstwem rolnym, wspomagające zarządzanie zasobami, produkcją roślinną i zwierzętami. Precyzyjne zarządzanie oparte na analizie danych historycznych i prognostycznych prowadzi do oszczędzania energii, zwiększania wydajności, optymalizacji stosowania herbicydów i pestycydów. Są to też dane dotyczące zwierząt, od modeli hodowlanych do genomiki.
Inteligentne autonomiczne systemy nawadniania pomagają monitorować i automatyzować zużycie wody w gospodarstwach. Wszystko oparte na precyzyjnie pobieranych i analizowanych danych pochodzących nie z kapelusza, lecz z systemu czujników, które gromadzą informacje i pomagają rolnikom monitorować zdrowie upraw, pogodę i jakość gleby.
Rozwiązania zautomatyzowanego rolnictwa oferuje obecnie mnóstwo firm. Jednym z przykładów jest FieldMicro i jej usługi SmartFarm i FieldBot. Rolnicy widzą i słyszą to, co widzi i słyszy FieldBot (4), zdalnie sterowane przenośne urządzenie, które łączy się ze sprzętem rolniczym/oprogramowaniem.
FieldBoty są wyposażone we wbudowany panel słoneczny, kamerę HD i mikrofon, a także czujniki, które monitorują temperaturę, ciśnienie powietrza, wilgotność, ruch, dźwięk i inne. Użytkownicy mogą sterować swoimi systemami nawadniania, zaworami przełączającymi, otwieranymi zasuwami, monitorować zbiornik i poziom wilgotności, przeglądać nagrania w czasie rzeczywistym, słuchać dźwięku w czasie rzeczywistym i wyłączać pompy z centrum operacyjnego. Zarządzanie FieldBotami odbywa się za pośrednictwem platformy SmartFarm, która pozwala użytkownikom na ustawianie reguł dla każdego FieldBota lub wielu współpracujących FieldBotów. Reguły mogą być ustawiane dla dowolnego sprzętu podłączonego do FieldBota, który następnie może aktywować inny sprzęt podłączony do innego Field-Bota. Dostęp do platformy można uzyskać za pośrednictwem smartfona, tabletu lub komputera.
FieldMicro nawiązał współpracę ze znaną, produkującą sprzęt rolniczy firmą John Deere w celu dostarczania danych do platformy SmartFarm. Użytkownicy będą mogli zobaczyć nie tylko lokalizację, ale również inne szczegóły dotyczące pojazdu, takie jak poziom paliwa, oleju i hydrauliki. Instrukcje mogą być również wysyłane z platformy SmartFarm do maszyn. Ponadto SmartFarm wyświetli informacje o dotychczasowym użyciu i zasięgu kompatybilnego sprzętu firmy John Deere. Historia lokalizacji urządzenia SmartFarm pozwala również na przeglądanie trasy przebytej przez maszynę przez ostatnie sześćdziesiąt dni i zawiera takie informacje, jak lokalizacja, prędkość jazdy i kierunek. Rolnicy mają również możliwość zdalnego dostępu do swoich maszyn John Deere, aby rozwiązywać problemy lub wprowadzać zmiany.
W ciągu dekady liczba robotów przemysłowych wzrosła trzykrotnie, z nieco ponad miliona jednostek operacyjnych w 2010 r. do planowanych 3,15 miliona jednostek w 2020 r. Chociaż automatyzacja może (i rzeczywiście) poprawić wydajność, produkcję na mieszkańca i ogólny standard życia, niektóre aspekty automatyzacji budzą obawy, choćby jej negatywny wpływ na pracowników o niskich kwalifikacjach.
Zadania rutynowe i wymagające niskich kwalifikacji są na ogół łatwiejsze do wykonania przez roboty niż nierutynowe zadania wymagające wysokich kwalifikacji. Oznacza to, że wzrost liczby robotów lub poprawa ich wydajności zagraża tym miejscom pracy. Ponadto pracownicy wyżej wykwalifikowani zazwyczaj specjalizują się w zadaniach, które automatyzacja uzupełnia, takich jak projektowanie i konserwacja robotów, nadzór i zarządzanie. Popyt na pracowników wysoko wykwalifikowanych i ich płace mogą wzrosnąć w wyniku automatyzacji.
Pod koniec 2017 r. McKinsey Global Institute opublikował raport (5), w którym oszacował, że niestrudzony marsz automatyzacji może wyeliminować do 2030 r. nawet 73 miliony miejsc pracy w samych tylko Stanach Zjednoczonych. "Automatyzacja jest z pewnością czynnikiem wpływającym na przyszłość siły roboczej", komentował w raporcie Elliot Dinkin, znany ekspert w kwestiach rynku pracy. "Istnieją jednak przesłanki, że jej wpływ na redukcję zatrudnienia może być mniejszy, niż przewidywano".
Dinkin zauważa również, że w odpowiednich okolicznościach automatyzacja ułatwia rozwój biznesu, a tym samym stymuluje wzrost zatrudnienia, a nie spadku. Firma Ford Motor Company wprowadziła linię montażu samochodowego w 1913 r., skracając czas montażu z 12 godzin na samochód do około półtorej godziny i umożliwiając ogromny wzrost produkcji. Od tego czasu przemysł samochodowy wciąż zwiększa automatyzację i... wciąż zatrudnia ludzi - w latach 2011-2017 liczba miejsc pracy pomimo automatyzacji wzrosła w tej branży o prawie 50 proc.
Nadmiar automatyzacji prowadzi wręcz do kłopotów, czego świeżym przykładem jest fabryka Tesli w Kalifornii, w której, jak przyznał sam szef firmy Elon Musk, przesadzono z automatyzacją. Analitycy z renomowanej firmy Bernstein w Wall Street twierdzą, że Elon Musk zbytnio zautomatyzował Teslę. Maszyny, które, jak mówił często wizjoner, zrewolucjonizują przemysł samochodowy, kosztowały firmę tak wiele, że przez pewien czas mówiono nawet o możliwości bankructwa Tesli.
Prawie w pełni zautomatyzowany zakład produkcyjny Tesli we Fremont w Kalifornii zamiast przyspieszyć i usprawnić dostawy nowych aut, stał się źródłem kłopotów firmy. Fabryka nie była w stanie sprostać zadaniu odpowiednio szybkiej produkcji nowego modelu auta Teslia 3 (Zobacz także: Gdzie piękna Tesla, a gdzie ponura Katanga). Proces produkcyjny był oceniany jako zbyt ambitny, ryzykowny i skomplikowany. "Tesla wydała około dwóch razy więcej niż tradycyjny producent w branży motoryzacyjnej na jednostkę mocy produkcyjnych", pisali w swojej analizie eksperci firmy analitycznej Berstein. "Firma zamówiła ogromną liczbę robotów Kuka. Automatyczne jest nie tylko tłoczenie, malowanie i spawanie (jak w większości innych producentów samochodowych), ale również próbowano tu zautomatyzować proces końcowego montażu. Tutaj Tesla wydaje się mieć problemy (jak również w spawaniu i montażu akumulatorów)".
Bernstein dodaje, że najwięksi na świecie producenci samochodów, Japończycy, starają się ograniczyć automatyzację, ponieważ "jest kosztowna i statystycznie negatywnie koreluje z jakością". Japońskie podejście polega na tym, że najpierw uruchomiony zostaje proces, a następnie wprowadza się roboty. Musk postąpił odwrotnie. Analitycy zwracają uwagę, że inne firmy samochodowe, które próbowały automatyzować 100 proc. procesów produkcyjnych, w tym giganci tacy jak Fiat i Volkswagen, również poniosły porażkę.
Hakerzy lubią przemysł
Pandemia COVID-19 prawdopodobnie przyspieszy rozwój i wdrażanie technologii automatyzacji. Pisaliśmy o tym w jednym z niedawnych wydań MT. Choć automatyzacja może przynieść przemysłowi wiele korzyści, nie należy zapominać, że jej rozwój niesie ze sobą nowe wyzwania, a jednym z największych wśród nich jest bezpieczeństwo. W niedawnym raporcie NTT pt. "Global Threat Intelligence Report 2020" są m.in. takie informacje, że np. w Wielkiej Brytanii i Irlandii produkcja przemysłowa jest najbardziej atakowanym cybernetyczne sektorem. Obszar ten notuje prawie jedną trzecią wszystkich ataków, przy czym 21 proc. ataków na świecie polega na skanowaniu przez cybernapastników luk w systemach i zabezpieczeniach.
"Produkcja przemysłowa wydaje się jedną z najbardziej atakowanych branż na świecie, najczęściej związane jest to z kradzieżą własności intelektualnej", pisze w raporcie NTT, jednak branża ta coraz częściej boryka się również z "naruszeniami danych o charakterze finansowym, ryzykiem związanym z globalnym łańcuchem dostaw oraz zagrożeniami wynikającymi z niedopasowanych słabych punktów".
Komentując raport, Rory Duncan z NTT Ltd. podkreślił, że: "Słabe bezpieczeństwo technik przemysłowych to rzecz znana od dawna - wiele systemów zostało zaprojektowanych z myślą o wydajności, przepustowości i zgodności z przepisami, a nie o bezpieczeństwie informatycznym". W przeszłości opierały się one również na pewnej formie "zabezpieczenia poprzez ukrycie". Protokoły, formaty i interfejsy w tych systemach były często złożone i zastrzeżone oraz różniły się od tych w systemach informatycznych, dlatego też atakującym trudno było przeprowadzić udany atak. Ponieważ coraz więcej systemów pojawia się w sieci, hakerzy wprowadzają innowacje i postrzegają te systemy jako podatne na ataki".
Konsultanci ds. bezpieczeństwa IOActive przeprowadzili niedawno atak cybernetyczny na systemy robotyki przemysłowe, aby przedstawić dowód, że można w ten sposób zakłócić funkcjonowanie największych korporacji. "Zamiast szyfrować dane, napastnik mógłby wycelować w kluczowe elementy oprogramowania robota, tak aby robot nie działał do czasu zapłacenia okupu", twierdzili badacze. Aby udowodnić swoją teorię, przedstawiciele IOActive skoncentrowali się na NAO, popularnym robocie w dziedzinie badań i edukacji. Ma on "prawie taki sam" system operacyjny i słabe punkty jak jeszcze bardziej znany Pepper firmy SoftBank. Atak wykorzystuje nieudokumentowaną funkcję, która pozwala przejąć zdalną kontrolę nad maszyną.
Następnie można wyłączyć normalne funkcje administracyjne, zmienić domyślne funkcje robota i przekierować dane z wszystkich kanałów wideo i audio na zdalny serwer w internecie. Kolejne kroki ataku obejmują podnoszenie uprawnień użytkownika, zakłócanie mechanizmu resetowania fabrycznego i zarażanie wszystkich plików w pamięci. Innymi słowy, mogą sprawić, że robot może wyrządzić szkody, a nawet fizycznie komuś zagrozić.
Jeśli proces automatyzacji nie zagwarantuje bezpieczeństwa, będzie to hamulec tego procesu. Trudno wyobrazić sobie, że przy tak wielkiej determinacji, by automatyzować i zrobotyzować, co się da, ktoś zaniedbał sfery zabezpieczeń.
Mirosław Usidus