Rewolucja druku 3D po opadnięciu kurzu. Rozwój produkcji warstwa po warstwie
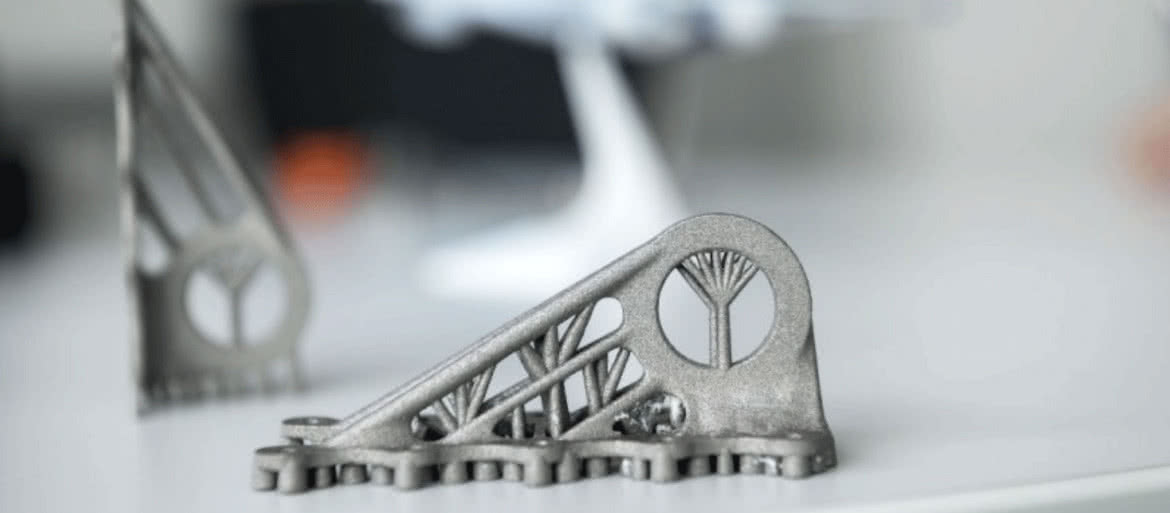
Dziś w addytywnych technikach produkcji dostrzega się nowe zalety, które ujawniły się w ostatnich czasach, podczas pandemii i zakłóceń gospodarczych nią wywołanych. Zwraca się uwagę, że druk 3D pozwala firmom szybko reagować na zakłócenia w dostawach bez konieczności utrzymywania kosztownych wielkich zapasów części, które ostatecznie mogą nie być potrzebne.
Produkcja addytywna z użyciem metali nie wymaga kucia ani odlewania, procesów kosztownych i czasochłonnych. Dzięki drukowi 3D części mogą być wytwarzane i dostarczane w ciągu kilku godzin lub najwyżej dni po ich zamówieniu. Skrócony czas realizacji przynosi korzyści obecnie głównie branży lotniczej i kosmicznej, ale też coraz częściej innym branżom, sparaliżowanym przez wąskie gardła w łańcuchach dostaw. W ostatnich latach odnotowano przecież przypadki, gdy zakłady otrzymywały części prawie rok po ich zamówieniu.
Produkcja addytywna może pozwolić na całkowite uniezależnianie od dostaw z zagranicy. Mniejsze zapasy pozwalają przedsiębiorstwom na obniżenie cen, uwolnienie kapitału np. w celu dokonania inwestycji. Przedsiębiorstwa mogą również szybciej reagować na zmianę asortymentu produktów oraz zwiększać lub zmniejszać produkcję w odpowiedzi na popyt.
Taniej i lżej
Ogólna koncepcja druku 3D znana jest od dziesięcioleci, jednak eksplozja nowych rozwiązań i zainteresowania nimi trwa dopiero od ok. dekady, choć trzeba przyznać, że przemysł wciąż przede wszystkim wykorzystuje konwencjonalne techniki obróbki zarówno metali, jak i innych materiałów, współcześnie głównie obrabiarki CNC.
Druk 3D może służyć jako dodatek lub substytut konwencjonalnej obróbki. Uznaje się go obecnie za najlepszą metodę tworzenia prototypów. Produkcja addytywna może także wytwarzać komponenty, które są trudne lub zbyt kosztowne do wytworzenia przy użyciu tradycyjnych, masowych linii produkcyjnych. Dochodzą do tego inne zalety produktów techniki addytywnej, np. niższa masa (np. dzięki strukturom kratownicowym) i możliwość uzyskania złożonych geometrii, które nie są możliwe w tradycyjnych procesach. Ponadto procesy addytywne radzą sobie coraz lepiej w wytwarzaniu wielomateriałowych części o specyficznych właściwościach co do przewodnictwa elektrycznego i wytrzymałości. Wytwarzanie addytywne ułatwia produkcję na żądanie dowolnego produktu przy kontroli kosztów i ustalonym czasie realizacji, skracając czas projektowania i wprowadzania produktu na rynek.
Druk 3D może być wsparciem dla bardziej tradycyjnych metod produkcji, choćby produkcji matryc z metalu do formowania wtryskowego. Dzięki zdolności druku 3D do wytwarzania złożonych konstrukcji można znacznie poprawić wydajność układów chłodzenia formy. Zdolność do tworzenia kształtów z pustymi lub kratownicowymi strukturami w środku znacznie obniża masę tam, gdzie nie jest potrzebna. Na przykład tytanowy wspornik produkowany addytywnie przez Airbusa jest o 30% lżejszy od tradycyjnie wytwarzanego poprzednika, bez uszczerbku dla wydajności lub trwałości (1).
Każda część wyprodukowana przez maszynę może być unikatowa, co otwiera drogę do masowej personalizacji. Wyeliminowanie czasochłonnego wytwarzania narzędzi i tradycyjnych operacji produkcyjnych przyspiesza zarówno projektowanie, jak i produkcję, skracając czas wprowadzenia na rynek. Złożona głowica wtryskiwacza paliwa używana w najnowszej rakiecie Ariane 6 jest teraz wytwarzana addytywnie jako pojedynczy kawałek stopu na bazie niklu. Poprzednie wersje tej części były spawane z ćwierci tysiąca indywidualnie obrabianych elementów.
Produkowana addytywnie przez General Electric dysza paliwowa do silników samolotów komercyjnych jest wykonywana z jednego komponentu zamiast z dwudziestu pojedynczych komponentów, co daje 30-procentową redukcję kosztów wytwarzania. Nowa dysza jest o 25 procent lżejsza i pięć razy bardziej wytrzymała. Firma Cellcore stworzyła metodą druku 3D prototypową dyszę rakietową z kanałami chłodzącymi w ściankach, która wygląda jak dzieło sztuki (2).
Wreszcie druk 3D może uprościć konserwację i wsparcie produktów w terenie, zmniejszając zapotrzebowanie na zapasy części zamiennych poprzez umożliwienie produkcji elementów na żądanie z plików cyfrowych. Siły Powietrzne USA drukują w 3D metalowe części zamienne na żądanie, uwalniając się od konieczności posiadania kosztownych zapasów lub czekania latami na części wykonane z trudno dostępnych komponentów. Z pomocą CAD projekty dosłownie wszystkich części mogą być przechowywane w formie cyfrowej kopii na dysku twardym komputera, co eliminuje konieczność utrzymywania zapasów. Nawet części, które już nie są produkowane, mogą być odtworzone na podstawie cyfrowych skanów. Tak można wytworzyć np. części zamienne klasycznych samochodów, co robi m.in. firma Mercedes-Benz.
Techniki addytywne są obecnie stosowane rutynowo i na dużą skalę do wytwarzania szerokiej gamy produktów medycznych, w tym protez i implantów, prowadnic chirurgicznych i modeli anatomicznych do planowania przedoperacyjnego lub edukacji pacjentów. Przemysł farmaceutyczny i urządzeń medycznych jest liderem w tej dziedzinie. Firmy produkujące urządzenia medyczne wytwarzają spersonalizowane implanty biodrowe zdolne do stymulowania wzrostu kości, tworząc porowate struktury, niemożliwe do wykonania metodami konwencjonalnej produkcji. W sektorze farmaceutycznym stosowane jest to do produkcji pigułek z dostosowanymi dawkami leków i ściśle zaprojektowaną charakterystyką uwalniania.
Wiele sektorów, takich jak motoryzacyjny, lotniczy i kosmiczny (3), zaczęło już wykorzystywać produkcję addytywną w swoich liniach produkcji części ze względu na skrócony czas realizacji i niskie koszty prototypowania. Wielka marka samochodowa, Porsche, rozpoczęła produkcję tłoków do silników i innych części za pomocą druku 3D (4).
Druk z metali - obiecująca, choć niełatwa alternatywa
Druk 3D, czy inaczej produkcja addytywna, to terminy używane do nazywania procesów budowania struktur poprzez łączenie materiału, np. tworzywa sztucznego, metalu czy gumy, warstwa po warstwie na bazie cyfrowych plików CAD.
40 lat po opracowaniu pierwszych komercyjnych maszyn do druku 3D wartość tej branży wynosi obecnie kilkanaście mld dolarów i rośnie w tempie ponad 20% rocznie. Jeśli chodzi o samą technikę, to ważny jest wzrost szybkości działania tych technik. Ma to duże znaczenie dla przemysłu. Na przykład najnowsze i najszybsze systemy oparte na selektywnym spiekaniu laserowym (SLS) wykorzystują aż milion diod laserowych, co znacznie przyspiesza tempo produkcji.
W raporcie firmy badawczej IDTechEx z marca 2022 r. pt. "Metal Additive Manufacturing 2022–2032: Technology and Market Outlook", kompleksowo przeanalizowano obecny stan branży druku 3D z wykrzystaniem materiałów metalicznych. Jej wartość ma za 10 lat wynieść 18,5 mld USD. Rynek jest obecnie zdominowany przez dwie firmy, ExOne i voxeljet.
Barierą jest ograniczona dostępność materiałów do tej techniki. Nie tylko stosunkowo niewiele metali o wysokiej wydajności jest dostępnych do wymagających zastosowań, ale koszt proszków metalowych często sięga setek dolarów za kilogram. Aby rozwiązać ten problem, bada się zastosowanie nowych materiałów, np. aluminium, oraz alternatywnych form granulek i zawiesin.
Mimo problemów metoda budowania geometrii warstwa po warstwie z topionego i spiekanego proszku metalowego na bazie modelu cyfrowego jest coraz bardziej ceniona wśród producentów złożonych komponentów, zaworów, dysz, wsporników, kształtek itd. Druk 3D z metali jest wykorzystywany przede wszystkim w przemyśle lotniczym, energetycznym, obronnym i medycznym, zyskuje też na popularności w przemyśle naftowym i gazowym.
Najbardziej popularne addytywne techniki metalowe to:
- Powder Bed Fusion (selektywne spiekanie, PBF) - Sproszkowany metal jest stapiany ze sobą przy użyciu źródła energii, zazwyczaj lasera o dużej mocy lub wiązki elektronów. Zastosowanie wiązki elektronów wymaga próżni. Jest to najbardziej rozpowszechniona forma druku 3D z metali, w której materiałem może być aluminium, stopy stali, stopy miedzi, nadstopy niklu i żelaza, metale szlachetne, metale ogniotrwałe, stopy tytanu i wiele innych.
- Binder Jetting (BJT) - Metoda, w której przemysłowa głowica drukująca selektywnie natryskuje ciekły środek spajający na cienką warstwę materiału budulcowego, warstwa po warstwie, zgodnie z przygotowaną bitmapą. Jest to jedna z najszybszych metod fabrykacji, ze względu na duży obszar roboczy maszyn operujących w technologii Binder Jetting i dużą ilość natryskiwanego spoiwa. W technologii Binder Jetting można wytwarzać elementy z prędkością osiągającą nawet 40 kg metalu na godzinę.
- Directed Energy Deposition (DED) - Proszek lub drut metalowy jest wprowadzany do jeziorka topnienia utworzonego przez laser lub wiązkę elektronów w procesie podobnym do spawania. Maszyny DED są powszechnie stosowane w naprawach komponentów o wysokiej wartości, takich jak łopatki turbin.
Druk 4D. Materiały oraz tworzywa jak metale
Rozwój addytywnej produkcji z metali to ważny, ale nie jedyny i nie ostatni krok w ewolucji technik addytywnych, z dużym potencjałem w dziedzinie wytwórstwa i projektowania urządzeń. To druk 4D, czyli technika jedno- lub wielomateriałowego drukowania urządzeń lub obiektów, które mogą, drogą tzw. morfingu (przeobrażeń) przeobrażać się w czasie. Przekształcenia takie zachodzą wskutek np. ogrzewania, światła, procesów elektrochemicznych lub zanurzenia w cieczy. Inaczej mówiąc, projektowany jest tu nie tylko kształt i statyczne właściwości, ale zachowanie pod wpływem określonych w planie bodźców.
Może to być przydatne np. w budowie robotów bez konieczności stosowania skomplikowanych urządzeń elektromechanicznych i chemicznych, a także w produktach adaptujących się, odzieży lub w mechanizmach reagujących na potrzeby użytkownika i zmieniające się otoczenie.
Warto też zwrócić uwagę na inny nurt - nie tyle poszukiwania najlepszej techniki druku 3D z metali, ile znalezienie materiału, który byłby we właściwościach podobny do metalu, ale miał zalety polimerów z punktu widzenia prostoty techniki druku 3D.
Zespół badawczo-rozwojowy w Weerg, firmie produkcyjnej oferującej obróbkę CNC i druk 3D, wprowadził w 2021 r. na rynek nowy materiał do produkcji addytywnej. To PEEK, organiczny polimer termo-plastyczny o wyjątkowych właściwościach mechanicznych, który gwarantuje wydajność podobną do aluminium. Zapewnia wytrzymałość na rozciąganie rzędu 89 MPa, jest trudnopalny i odporny na działanie substancji takich jak oleje, smary i węglowodory. Produkty z PEEK-u firmy Weerg nadają się do stosowania w trudnych warunkach i surowym środowisku, np. w sektorze lotniczym, gdzie może być wykorzystywany do produkcji elementów konstrukcyjnych, osłon i izolacji.
Aeronautyka ziemią obiecaną druku 3D
To właśnie sektor lotniczy, a idąc dalej, także kosmiczny, jest dziś na czele listy odbiorców produkcji addytywnej. Wymaga się tu komponentów o wysokich parametrach bezpieczeństwa, działających w wymagającym środowisku. Jednocześnie zwykle zapotrzebowanie jest na pojedyncze sztuki lub małe serie, przy szybkim czasie realizacji. Kolejne wymaganie to lekkość konstrukcji, która bez straty dla parametrów mechanicznych ma przekładać się na obniżenie kosztów, materiału i paliwa.
Konstrukcje latające są zazwyczaj systemami wysokiej złożoności i małej objętości, co oznacza, że techniki addytywne mają pole do popisu. Dawniej opierały się na elementach kutych i odlewanych. Kucie wymaga kosztownego projektowania, procesów produkcji i testów wstępnie uformowanych matryc, zaś obróbka odlewów jest z natury kosztowna, przy czym typowy stosunek ceny do jakości szacuje się na 20:1. Na przykład produkt końcowy o masie 10 kg wymagałby 200 kg materiałów z magazynu. Technika addytywna wytwarza niewiele lub nie wytwarza żadnych odpadów przy stosunku wynoszącym od 1:1 do 3:1.
Wciąż wyzwaniem jest jakość i odpowiednie właściwości wytwarzanych komponentów. Dotyczy to m. in. chropowatości powierzchni, porowatości, naprężeń strukturalnych i związanych z nimi pęknięć lub wypaczeń elementów. Zachodzi także niepewność co do właściwości materiałów oraz wysokie wymagania projektowe w procesach druku 3D.
Pomimo tych wad, nie brakuje scenariuszy, w których druk 3D świetnie sprawdza się w zastosowaniach lotniczych, mając w wielu przypadkach dużą przewagę nad tradycyjnymi metodami produkcji. Jedną z kluczowych zalet produkcji addytywnej jest to, że może ona wytwarzać części, których nie mogą wytwarzać konwencjonalne techniki produkcyjne.
Typowymi materiałami dla druku 3D w przemyśle lotniczym są stopy aluminium, stal nierdzewna, stopy tytanu, nadstopy na bazie niklu i żelaza, stopy miedzi, stopy kobaltu, stopy ogniotrwałe oraz stale, wśród innych materiałów metalicznych. Inne stopy metali, które mogą być używane w tej dziedzinie, to stopy ogniotrwałe z użyciem niobu, tantalu i wolframu i innych metali rzadkich, takie jak C-103. Są one wykorzystywane w zastosowaniach związanych z ekstremalnymi temperaturami, takimi jak pędniki kosmiczne (5). Większość z nich stosowana jest w postaci proszku, najczęściej wytwarzanego metodą atomizacji gazowej lub też w postaci drutu w zależności od procesu.
Nie można na zakończenie nie wspomnieć, iż przedstawiciele przemysłu widzą jednak istotne przeszkody w rozwoju technik addytywnych. Mimo wspominanych postępów w szybkości, wciąż ocenia się tę technikę jako bardzo wolną w porównaniu z tradycyjnymi technikami obróbki metali. W dodatku rozmiary produktów są ograniczone. Maszyny addytywne okazały się również dość trudne do zintegrowania ze znanymi procesami produkcyjnymi. Ponadto sprzęt do druku 3D często opiera się na oprogramowaniu sterującym specyficznym dla danego producenta, z ograniczoną interoperacyjnością pomiędzy różnymi systemami. Wciąż problemem jest stabilność jakości i wydajności. Także materiały do druku 3D nie należą do łatwych w produkcji i tanich np. dodatkowe przetwarzanie wymagane do przekształcenia stopów metali w formę proszku znacznie zwiększa koszty.
Są w końcu bariery wynikające z konserwatyzmu środowisk przemysłowych i niechęci do nowych rozwiązań, z których korzyści nie są dla każdego jasne. I choć możemy je uważać za nieuzasadnione, są faktem, którego nie można lekceważyć.
Mirosław Usidus