Kurs projektowania 3D w 360. Bryły walcowe - lekcja 2
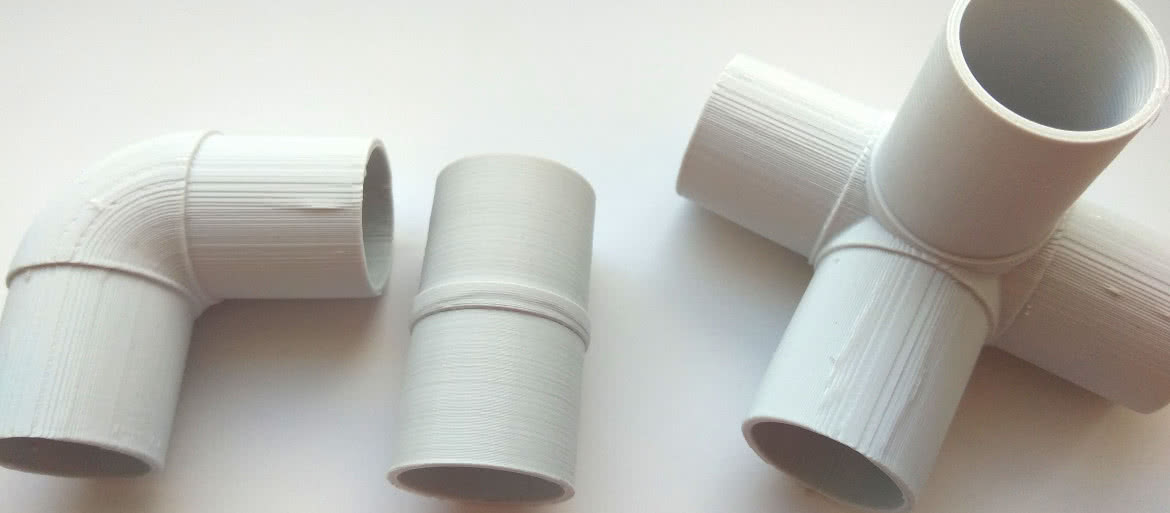
Plastikowe rurki często wykorzystywane są w przydomowych warsztatach ze względu na powszechną dostępność i przystępną cenę. Na całym świecie powstają różne konstrukcje budowane z rurek o najróżniejszych średnicach - od słomek do napojów, przez rurki instalacji wodnych i elektrycznych, aż po kanalizacyjne. Nawet z dostępnych w marketach budowlanych łączników i kolanek instalacji wodnych można wiele zrobić (2, 3).
Możliwości są naprawdę ogromne, a dostęp do specjalnego rodzaju łączników jeszcze je zwielokrotnia. W krajach anglosaskich na rynku znajdziemy złączki przeznaczone specjalnie dla majsterkowiczów - ale kupowanie ich za granicą poważnie podważa sens ekonomiczny całego przedsięwzięcia… Nic to! Przecież można w łatwy sposób zaprojektować i wydrukować we własnym domu nawet takie złączki, których i w Ameryce nie da się kupić! Już po najnowszej lekcji naszego kursu nie powinno to stanowić żadnego problemu.
Na początek coś prostego - łącznik zwany mufką
To zdecydowanie najprostszy z łączników. Podobnie jak w poprzedniej lekcji - polecam rozpocząć od stworzenia szkicu na jednej z płaszczyzn, rysując okrąg o środku w środku układu współrzędnych. Średnica jego końcówek powinna mieć wymiar średnicy wewnętrznej rur, które planujemy łączyć (w opisywanym przypadku będą to rurki elektryczne o średnicy 26,60 mm - cieńsze więc, tańsze niż wodne, ale wyjątkowo ubogie w odpowiednie dla majsterkowiczów łączniki).
Czas na coś bardziej złożonego - kolanko 90o
Projektowanie tego elementu rozpoczniemy od szkicu na dowolnej płaszczyźnie. W tym wypadku także warto rozpocząć w środku układu współrzędnych. Rozpoczniemy, rysując dwie równe, prostopadłe do siebie linie. Pomoże w tym siatka w tle arkusza, do której "przykleją się" rysowane linie.
Każdorazowe pilnowanie, aby linie były równe, może być uciążliwe - zwłaszcza jeśli będzie ich więcej. Z pomocą przychodzi tu okno pomocnicze, przyklejone do prawej strony ekranu (domyślnie może być zwinięte). Po jego rozwinięciu (przy pomocy dwóch strzałek widocznych nad napisem) ukazują się dwie listy: Options oraz Constraints.
Zaznaczając obie narysowane linie, odszukujemy na drugiej liście opcji Equal. Po kliknięciu można ustawić zależność pomiędzy długościami linii. Na rysunku w pobliżu linii pojawi się znak „=”. Pozostaje zaokrąglić szkic tak, aby przypominał kolanko. Użyjemy opcji Fillet z rozwijalnej listy zakładki SKETCH. Po wybraniu tej opcji klikamy punkt łączenia narysowanych linii, wprowadzamy wartość promienia i zatwierdzamy wybór, klikając Enter. W ten sposób powstała tzw. ścieżka.
Potrzebny teraz będzie profil kolanka. Zamykamy obecny szkic, klikając opcję z ostatniej zakładki (STOP SKETCH). Ponownie tworzymy nowy szkic - wybór płaszczyzny jest tu kluczowy. Powinna to być płaszczyzna prostopadła do tej, na której znajdował się poprzedni szkic. Rysujemy okrąg (średnica 28,10 mm), podobnie jak poprzednie (ze środkiem w środku układu współrzędnych), i zarazem na początku wcześniej narysowanej ścieżki. Po narysowaniu okręgu zamykamy szkic.
Wybierzmy opcję Sweep z rozwijalnej listy zakładki CREATE. Otwiera się okienko pomocnicze, w którym musimy wskazać profil oraz ścieżkę. W przypadku zniknięcia szkiców z pola roboczego możemy je wybrać z drzewka po lewej stronie z zakładki Sketches.
W okienku pomocniczym podświetla się opcja Select przy napisie Profile - wybieramy więc profil, czyli drugi szkic. Następnie klikamy przycisk Select poniżej i wybieramy ścieżkę, czyli pierwszy szkic. Zatwierdzenie operacji tworzy kolanko. Średnica profilu może być oczywiście dowolna - w przypadku kolanka tworzonego na potrzeby tego artykułu ma wymiar 28,10 mm (to średnica zewnętrzna rurki).
Chcemy, aby łącznik wchodził do wnętrza rurki (12), więc musi mieć średnicę taką samą jak średnica wewnętrzna rurki (w tym wypadku to 26,60 mm). Efekt ten uzyskamy, przycinając odnogi kolanka. Na końcach kolanka rysujemy okrąg o średnicy 26,60 mm, oraz drugi okrąg - już o średnicy większej niż średnica zewnętrzna rurek. Tworzymy wzór, którym przytniemy łącznik na odpowiednią średnicę, pozostawiając zagięty fragment kolanka o średnicy zewnętrznej rurki.
Zabieg ten powtarzamy na drugiej odnodze kolanka. Podobnie jak w przypadku pierwszego łącznika odchudzimy teraz kolanko. Wystarczy użyć opcji Schell z zakładki MODIFY. Po wybraniu tej opcji zaznaczamy końcowe ścianki, które mają być wydrążone i określamy szerokość obrzeża, które ma zostać. Omówiona funkcja usuwa jedną ścianę i tworzy z naszego modelu "wydmuszkę".
Zrobione?
Voila! Kolanko gotowe (15)!
OK, mamy to! I co dalej?
Bieżąca lekcja, przedstawiając zasady tworzenia prostych brył walcowych, otwiera jednocześnie możliwość realizacji podobnych projektów. "Produkcja" bardziej złożonych łączników jest równie prosta jak tych przedstawionych powyżej (18). Opiera się na zmianie kątów pomiędzy liniami ścieżki lub doklejeniu kolejnego kolanka. Operację wydrążenia środka wykonujemy na samym końcu projektowania. Przykładem są choćby łączniki sześciokątne (lub klucze imbusowe), a otrzymamy to dzięki zmianie kształtu profilu.
Modele mamy gotowe i umiemy je już zapisać do pliku o odpowiednik formacie (.stl). Tak zapisany model możemy otworzyć w specjalnym programie, który przygotuje plik do wydruku. Jednym z najpopularniejszych i darmowych programów tego typu jest Ultimaker Cura, dostępny w polskiej wersji językowej.
Po zainstalowaniu poprosi nas o podanie modelu drukarki. Ma bardzo przejrzysty interfejs i nawet osoba po raz pierwszy uruchamiająca program bez problemu poradzi sobie z przygotowaniem modelu do druku. Otwieramy plik z modelem (Plik → Otwórz plik), w prawym okienku zadajemy materiał, z jakiego będziemy drukować, określamy dokładność i ustawiamy dodatkowe opcje poprawiające jakość wydruku - wszystkie stają się dodatkowo opisane po najechaniu na napis.
Wiedząc, jak zaprojektować i wydrukować stworzone modele, pozostaje tylko przetestować zdobytą wiedzę. Niewątpliwie przyda się w kolejnych lekcjach - komplet tematów całego kursu prezentujemy w tabeli poniżej.
• Lekcja 1: Bryły przeciągane (breloki)
• Lekcja 2: Bryły walcowe (łączniki rurek)
• Lekcja 3: Bryły kuliste (łożyska)
• Lekcja 4: Bryły złożone (elementy konstrukcyjne robotów)
• Lekcja 5: Proste mechanizmy na raz! (przekładnie kątowe).
• Lekcja 6: Prototypy modeli (model dźwigu budowlanego)
Zobacz także:
3D w 360 - czyli jak w pełnym zakresie pracować z nowymi technologiami
Praktyczny Kurs Druku 3D
Motoryzacja z drukarki 3D
Bartłomiej Jakobsche