Projektowanie części metodą ewolucyjną. Części NASA jak wzięte z natury
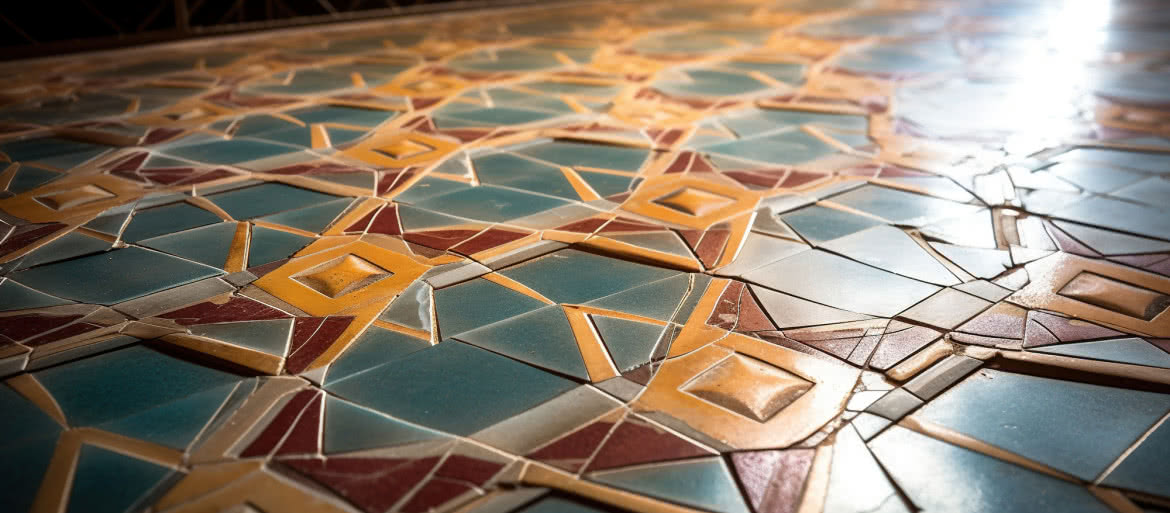
Projektowanie generatywne (ang. generative design) to metoda projektowania, która wykorzystuje algorytmy uczenia maszynowego i sieci neuronowe do zautomatyzowanego generowania rozwiązań projektowych. Polega ona na zastosowaniu algorytmów do procesu projektowania i pozwala na wygenerowanie dużej liczby wariantów projektowych na podstawie wstępnie określonych parametrów i ograniczeń. Projektowanie generatywne jest już niekiedy stosowane w wielu dziedzinach, takich jak architektura, design produktów, grafika czy animacja.
W projektowaniu generatywnym projektant określa zbiór zmiennych projektowych, takich jak wymiary, kształty, materiały i warunki obciążeniowe, a następnie korzysta z algorytmów generatywnych, aby wygenerować wiele możliwych rozwiązań projektowych, które spełniają wymagania. Algorytmy te wykorzystują uczenie maszynowe, sieci neuronowe i algorytmy genetyczne, aby przetestować i zoptymalizować różne kombinacje zmiennych projektowych, aż do znalezienia najlepszego rozwiązania. Dzięki zastosowaniu algorytmów generatywnych, projektanci mogą szybciej i dokładniej wygenerować wiele różnych rozwiązań projektowych, co pozwala na wybór najlepszego rozwiązania i osiągnięcie lepszych wyników projektowych.
Przyspieszona ewolucja w chmurze obliczeniowej
Można w tej "filozofii" projektowania znaleźć analogię z ewolucją organizmów biologicznych, która kształtowała przez wieki coraz doskonalsze i lepiej dostosowane szkielety zwierząt pod kątem zdolności do przenoszenia obciążeń. Przyspieszona symulacja procesu ewolucji pomaga teraz agencji NASA tworzyć mocniejsze i lżejsze części do swoich projektów statków kosmicznych. Ważne, że dzieje się to w krótkim czasie, a nie miliony lat, jak w ewolucji życia na Ziemi.
W ciągu ostatniej dekady koszty startu w kosmos zmniejszyły się znacznie, ale wynoszenie masy na orbitę nadal nie jest tanie - najkorzystniejsze ceny w SpaceX nadal przekraczają tysiąc dolarów za kilogram. Tak więc przemysł lotniczy i kosmiczny pozostaje wciąż branżą, w której zmniejszenie wagi ma duże znaczenie po stronie kosztów.
W 2017 roku w popularnym wśród projektantów oprogramowaniu CAD Fusion360 firmy Autodesk znalazły się funkcje, które pozwalają na zgrubne opracowanie projektu części, prawidłowe wykonanie wszystkich krytycznych pomiarów, poinformowanie oprogramowania o tym, jakie obciążenia i naprężenia musi wytrzymać dana część i z jakich kierunków, a następnie umożliwienie programowi podążenia drogą wytyczoną przez parametry i podjęcia serii eksperymentów, poszukujących metody wykonania projektu z maksymalną wydajnością. Program zaczyna poddawać obiekt kolejnym modyfikacjom, zmieniając elementy po kawałku, co jest bardzo podobne do procesów ewolucji, w których kolejne mutacje wypróbowują kolejne kombinacje DNA organizmów i testują je pod kątem wymaganych celów efektywności, czyli tego, że życie testuje mutacje DNA. W ciągu milionów operacji oprogramowanie zwiększa ilość metalu w jednym miejscu, usuwa trochę w innym, i sprawdza, czy dana część jest wytrzymalsza czy słabsza, lżejsza czy cięższa od poprzednich.
W zaskakująco krótkim czasie (kilka godzin, jeśli ma się dostęp do wysokowydajnego przetwarzania w chmurze) otrzymujemy kształty, których człowiek raczej nie mógłby samodzielnie zaprojektować. Są one zadziwiająco podobne do dzieł natury. Tam, gdzie trzeba poradzić sobie z większym naprężeniem, stopniowo stają się grubsze. Tam, gdzie naprężenia są mniejsze, stają się cieńsze. Struktury nośne zanikają tam, gdzie nie są potrzebne, i mają tendencję do ustawiania się w zgodności ze ścieżkami obciążenia. Krótko mówiąc, zaczynają wyglądać dziwnie jak szkielety kostne i struktury organiczne.
Jeśli działa, to w czym problem?
Najważniejsze jednak jest to, że ta metoda po prostu przynosi dobre efekty dla końcowego projektu. Ryan McClelland, inżynier z NASA, twierdzi, że owe "wykształcone struktury" często wykonują swoją pracę znacznie lepiej niż cięższe części zaprojektowane przez człowieka: Po przeprowadzeniu analiz naprężeń inżynierowe stwierdzają, że części generowane przez algorytm nie wykazują takich koncentracji naprężeń, jakie występują w przypadku konstrukcji zaprojektowanych przez człowieka. Współczynniki naprężeń są prawie dziesięciokrotnie niższe niż części tworzone przez wykwalifikowanego inżyniera-projektanta.
McClelland był prekursorem i orędownikiem wykorzystania projektowania generatywnego w NASA, prezentując możliwości zmniejszania masy poszczególnych elementów konstrukcyjnych nawet dwie trzecie za pomocą tych metod. Chociaż ta ewolucyjna technika AI najlepiej współgra w połączeniu z produkcją addytywną, czyli procesami druku 3D, które pozwalają na projektowanie kształtów, które nie mogą być wytwarzane w sposób tradycyjny, wydaje się, że NASA na tym etapie projektuje w ten sposób części wytwarzane także drogą obróbki skrawaniem.
Części te były już wykorzystywane w szerokim wachlarzu projektów, od misji Mars Sample Return do teleskopów kosmicznych, monitorów pogody kosmicznej, instrumentów planetarnych, obserwatoriów balonowych i innych. Przykładem są kształtki w tytanowym rusztowaniu tylnej części teleskopu EXCITE, którego start zaplanowano na ten rok. Łączą one płytę z włókna węglowego podtrzymującą główne lustro z odbiornikiem podczerwieni umieszczonym w aluminiowej komorze kriogenicznej. Występowały tu kombinacje specyficznych połączeń i precyzyjnych parametrów obciążenia, które okazały się sporym wyzwaniem dla projektantów. Zastosowane w konstrukcji materiały charakteryzują się bardzo różnymi właściwościami rozszerzalności cieplnej. Inżynierowie musieli stworzyć między nimi połączenie, które nie będzie obciążać żadnego z materiałów.
Projektowanie generatywne pomogło w tym trudnym inżynierskim wyzwaniu. Pomaga w wielu innych. Jeśli technika ta sprawdzi się w kosmosie, to kto wie, czy już za kilka, kilkanaście lat nie zobaczymy charakterystycznych, "organicznych" kształtów także w wielkich konstrukcjach naziemnych, np. w mostach czy w dźwigach.
Mirosław Usidus