Aeromobil
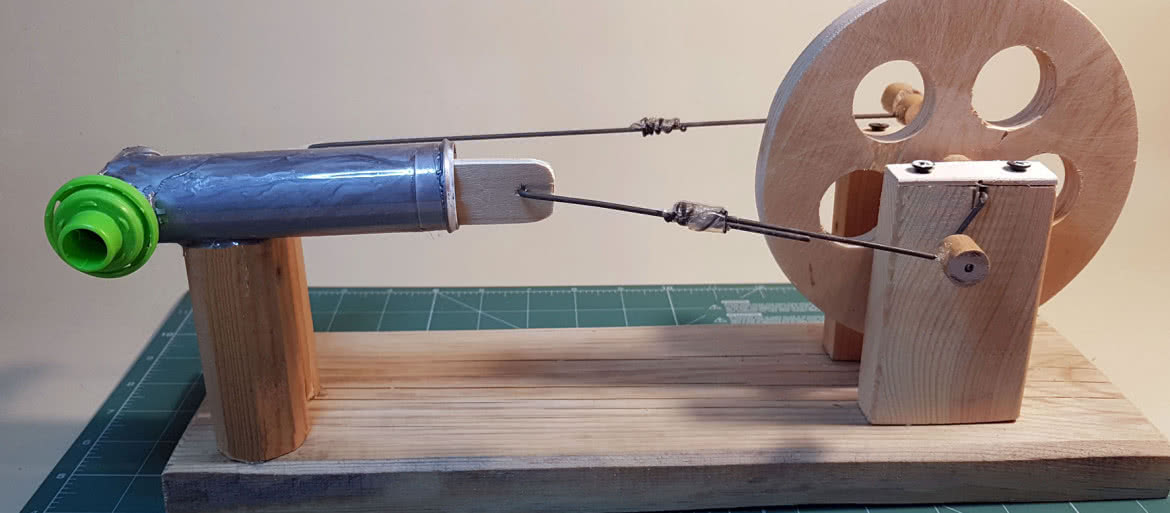
Gdyby zastąpić plastikowe tubusy cylindrami z rurek miedzianych, a tłok choćby odlewem z ołowiu, można by naszą maszynę poruszyć parą. Ale nie tym razem. Nasz działający model będzie poruszany sprężonym powietrzem pochodzącym z warsztatowej sprężarki. Od zwykłych maszyn parowych nasz model odróżnia się nietypowym rozrządem, pracującym pod kątem 90 stopni do głównego cylindra. Zwykle rozrząd jest zaprojektowany jako równoległy do głównego cylindra i podaje parę raz z jednej, a raz z drugiej strony cylindra. Nasz model ma mniej sprawny sposób podawania sprężonego medium, bo tylko raz na cykl pracy. Zużyte powietrze ucieka odsłoniętym otworem, wypychane przez tłok siłą bezwładności obracającego się koła zamachowego.
Prześledźmy, jak działa nasz model. Do rozrządu dostarczamy sprężone powietrze. Gdy tłok rozrządu jest w skrajnym, najdalszym położeniu, powietrze dostaje się otworem do cylindra i popycha tłok pracy. Tłoczysko przenosi tę siłę na korbę wału korbowego, a ten zmienia ruch posuwisty na ruch obrotowy koła zamachowego. Koło obraca się i siłą bezwładności przesuwa tłok pracy w cylindrze. Ponieważ tłok rozrządu zmienił swoje położenie na drugie skrajne, zużyte powietrze może wydostać się z cylindra rozrządu. Wał dalej się obraca i cykl może powtarzać się od początku. Tu widzimy, że maszyna wykonuje pracę tylko w czasie, kiedy powietrze wypycha tłok. Straty w wydajności są dość duże i może dlatego tego typu maszyny znalazły zastosowanie jedynie do napędu zabawek albo jako silniki parowe do drobnych prac domowych, choć te ostatnie zostały wyparte przez silniki elektryczne. Praktycznie takie silniki przeszły do historii i możemy je podziwiać w muzeach techniki, i to nie wszystkich. Działanie maszyny możemy obejrzeć i przeanalizować na rysunku. Z łatwością zrozumiemy jego działanie i bez problemu możemy przystąpić do budowy.
Materiały potrzebne do budowy: Deseczka drewniana calowa na podstawę, gruba 12-milimetrowa sklejka to materiał na koło zamachowe, kantówka 60×20 milimetrów na suport cylindra oraz koła zamachowego i mechanizmu rozrządu, cienka 3-milimetrowa deseczka ze skrzynek po owocach, plastikowe fiolki po lekach i witaminach, 6 szprych rowerowych, kit dwuskładnikowy pod nazwą Poxilina, z której powstanie tłok maszyny.
Narzędzia: klej na gorąco w serwującym go pistolecie, wiertarka na statywie zapewniającym nam pożądaną prostopadłość wierconych otworów, wiertło stolarskie o średnicy 30 i 20 milimetrów oraz zwyczajne walcowe wiertła średnic 3,3 i 4 milimetry, wyrzynarka, piła ukośnica, szlifierka, wkrętarka, dremel z oprzyrządowaniem do cięcia i szlifowania, linijka, kątomierz, ołówek, cyrkiel, punktak, młotek, olej silikonowy.
Podstawa maszyny: zrobimy ją z deski o wymiarach 350×120×25 milimetrów. Powinna być ciężka, by zapewnić stabilność modelu. Po odcięciu materiału na odpowiedni wymiar, za pomocą szlifierki taśmowej lub ręcznie papierem ściernym, wyrównajmy powierzchnię podstawy. Warto też fazować krawędzie deski. Fazowanie oznacza oszlifowanie ostrych krawędzi pod kątem 45 stopni, tak jak widać na zdjęciu. Nada to profesjonalizmu i sznytu naszej podstawie modelu.
Suport koła zamachowego: składa się z dwóch klocków kantówki o wymiarach 95×60×20 milimetrów każdy. Papier ścierny posłuży do wyrównania powierzchni po cięciu. Za pomocą piły do metalu lub dremela uzbrojonego w tarczę do cięcia, w czołach zestawionych ze sobą klocków wypiłujemy wgłębienie, w którym będzie pracował wał korbowy. Oczywiście wcześniej narysujemy zarys wgłębienia na klockach. Wymiary wgłębienia powinny być szerokości i głębokości nieco większej niż rowerowa szprycha, z której będziemy robić wał korbowy. Rowki wgłębień zakrywają dwie cienkie deseczki o wymiarach dokładnie takich jak czoło klocków kantówki. Odrysujemy je i wytnijmy z drewna pochodzącego ze skrzynki po owocach. Mają mieć wymiary dokładnie takie jak czoło klocków suportu. Pokrywy te mocujemy drewnowkrętami po dwa każda. Tak wykonane suporty przyklejamy do podstawy modelu, w odległości od siebie takiej, jaką ma nasze koło zamachowe. Celem dokładnego ustawienia, podczas klejenia suportów, w wypiłowane wgłębienia włożymy prostą szprychę zastępującą chwilowo wał korbowy. Od razu zorientujemy się, czy ustawienie klocków jest prawidłowe i wał ustawiony jest prostopadle do boku podstawy oraz równolegle do powierzchni deski.
Suport cylindra: jest zrobiony z klocka sześciokątnego lub kantówki o wysokości 80 milimetrów.
Suport rozrządu: jest zrobiony z klocka sześciokątnego o wysokości 80 milimetrów.
Cylinder: to plastikowy tubus o średnicy 30 milimetrów, w którym pierwotnie były pastylki zestawu witamin czy wapna. Opakowania takie są do kupienia w popularnych sieciach handlowych. Za pomocą dremela uzbrojonego w tarczę do cięcia odcinamy z naszej tubki o średnicy 30 milimetrów rurkę o długości 110 milimetrów. Odciętą krawędź zaokrąglamy, formując wgłębienie tak, by potem dała się do niej przykleić tubka zawierająca tłoczek rozrządu. Druga rurka o długości 15 milimetrów, odcięta z tej samej tubki, stanie się formą do wykonania cylindra. Oczywiście do cięcia zamiast dremela można użyć drobno ząbkowanego brzeszczotu do metalu, który poradzi sobie z twardym plastikiem. Aby precyzyjnie odciąć tubus, należy go położyć na lekko rozchylone szczęki imadła, podkładając uprzednio papierową chusteczkę. Papier zapobiegnie porysowaniu tubusu przez szczęki imadła podczas cięcia.
Cylinder rozrządu: to cylindryczna plastikowa tuba o średnicy 20 milimetrów, po jakimś leku. Dzielimy ją na dwie części 50 i 20 milimetrów, uprzednio odcinając dno. W dłuższej części, centralnie w jej boku, wiercimy otwór o średnicy 14 milimetrów, jak to jest widoczne na fotografii. Krótsza część cylindra posłuży nam jako forma do zrobienia tłoczka rozrządu.
Tłoki: wykonamy z poxiliny i ze szprychy rowerowej. Wystająca szprycha będzie tłoczyskiem. Trudno byłoby ot tak ulepić tłok o właściwej średnicy i dodatkowo tak dokładnie, żeby tłoczysko było umieszczone centralnie i prostopadle do tłoka. Poradzimy sobie z tym, przygotowując odpowiednią formę. Zaczniemy od podstawy formy, czyli od wyszukania pomocniczej deseczki o wymiarach około 90×150×20 milimetrów. Wiercimy w niej najpierw otwór 3,3 milimetra, czyli taki, jaką ma średnicę nasza szprycha. Ten otworek rozwiercamy wiertłem stolarskim o średnicy 30 milimetrów, ale tylko na głębokość około 5 milimetrów. Do otworu dopasowujemy krótką rurkę, tę, którą odcięliśmy od tubki i przeznaczyliśmy na formę cylindra. Do małego otworu 3,3 milimetra wkładamy szprychę razem z jej nakrętką. Nakrętka ta będzie potem zalepiona i schowana w środku tłoka. Na spód drewnianej formy jeszcze wkładamy krążek papieru i smarujemy go oraz wnętrze rurki oliwą techniczną lub smarem silikonowym. Nie żałujmy tłuszczu. To zapobiegnie przyklejeniu się poxilinowego tłoka do elementu formy.
Teraz możemy sięgnąć po masę i odciąć odpowiednią ilość poxiliny. W przekroju odpakowanej masy widać, że składa się ona z dwu różnych warstw. Odcinamy nożem odpowiednią ilość dwukolorowej masy, aby powstał z niej tłok. Należy te warstwy, ciemniejszą i jaśniejszą, zmieszać w taki sposób, jak się ugniata plastelinę. Gdy masa otrzyma już jednakowy szary kolor, w poxilinie zaczyna się reakcja utwardzania, ale my mamy czas i korzystając z tego, upychamy ją do rurki z wystającą od spodu szprychą. Powinna schnąć około doby. Po tym czasie możemy cieszyć się gotowym tłokiem. Jeśli nie pożałowaliśmy smaru, oddzielimy nasz tłok bez problemu od jego formy. Po przymiarce, do drugiej części rurki mającej pełnić funkcję cylindra, pewnie trzeba będzie użyć papieru ściernego i wyrównać czoło tłoka, a nawet troszeczkę jego średnicę. Po tej obróbce znowu smarujemy tłok i cylinder smarem. Wreszcie, gdy wszystko poszło dobrze, możemy cieszyć się pasującym do tłoka cylindrem. Ale zaraz. Nim zabierzemy się do robienia tłoka, równocześnie proponuję zrobienie także zaworu tłoka rozrządu. Wszystko robimy tak samo, tylko uwzględniamy mniejszą średnicę cylindra rozrządu. W naszej deseczce wiercimy drugi otworek na szprychę, rozwiercamy na głębokość 5 milimetrów, taką średnicą wiertła, jaką ma cylinder rozrządu. Wkładamy krótką rurkę, formę tego cylindra, smarujemy silikonowym smarem i napełniamy poxiliną. Ponieważ cylinder rozrządu jest niższy, nieznacznie skracamy szprychę razem z jej nakrętką. Widzimy to na fotografiach.
Wałeczki stabilizujące: odetniemy je z pręta drewnianego o średnicy 10 milimetrów. Wysokość każdego wałeczka to 10 milimetrów. Potrzebujemy sześciu takich kawałków. Piła ukośnica, którą będziemy ciąć pręt, zapewni równoległość powierzchni czołowych i prostopadłość do ścianek detalu. W sześciu wałeczkach wiercimy centralnie, uprzednio napunktowane, otwory o średnicy szprychy, czyli 3,3 milimetra, a w dwu pozostałych 4 milimetry.
Suwak: do wystającego z tłoka na 50 milimetrów kawałka szprychy doklejamy prostokątny kawałek deseczki o wymiarach 60×25×3 milimetra. Ta deseczka to suwak. Ma on za zadanie zapewnić zawsze równoległy ruch tłoka do ścianki cylindra. Tłoczysko przykleimy klejem na gorąco do deseczki. W osi tłoczyska wiercimy otwór 3,3-milimetrowy w odległości 10 milimetrów od krawędzi. Na koniec zaokrąglamy rogi suwaka i sprawdzamy, jak pracuje w rurce cylindra. Powinien poruszać się bez oporu.
Napęd rozrządu: od wału korbowego ruch przenosi szprycha z jednej strony wklejona w wałeczek drewniany o wymiarach 10 milimetrów średnicy i 10 wysokości. W wałku, z boku, centralnie wiercimy otwór 3,3 milimetra. Druga szprycha ma zagięty koniec pod kątem 90 stopni i włożona jest w otwór elementu w kształcie trójkąta. Szprychy na czas montażu połączymy wstępnie za pomocą cienkiego drutu. Będziemy je mogli rozsuwać lub skracać połączenie, aż dobierzemy odpowiednią długość korbowodu. Gdy to się stanie, zafiksujemy je ze sobą za pomocą kleju na gorąco. Widzimy to na fotografii.
Trójkąt rozrządu: z cienkiej deseczki wycinamy trójkąt prostopadły, którego ramiona mają wymiary 50×70 milimetrów. W jego rogach wiercimy otwory o średnicy trochę większej, niż ma nasza szprycha, czyli 3,3 milimetra. Wyrównajmy wszelkie nierówności i zaokrąglijmy rogi naszego trójkąta za pomocą szlifierki lub ręcznie papierem ściernym. W otworze znajdującym się najbliżej kąta prostego trójkąta będzie oś obrotu. Trójkąt rozrządu, poruszając się, będzie przekształcał ruch posuwisto-zwrotny na taki sam, ale obrócony o 90 stopni i będzie poruszał tłok w cylindrze rozrządu. Jego działanie widzimy na rysunku.
Koło zamachowe: powinno być w miarę możliwości spore i ciężkie. Proponuje sklejkę o grubości 12 milimetrów. Na jej powierzchni rysujemy cyrklem koło o średnicy 140 milimetrów. Za pomocą wyrzynarki starannie wycinamy kształt. Dla ułatwienia sobie pracy wyrzynarką proponuję zamocowanie sklejki ściskiem stolarskim do powierzchni stołu. To pozwoli się nam skupić na wycinaniu, a nie pilnowaniu wędrującej po stole sklejki. Gdy mamy już wycięte koło, na jego powierzchni wyznaczmy miejsca pod pięć otworów, o średnicy 30 milimetrów, rozmieszczonych co 72 stopnie. Koło upodobni się nieznacznie do koła szprychowego. Na koniec proponuję użyć papieru ściernego dla wyrównania formy i dbałości o estetykę modelu. Koło nakładamy na prosty odcinek drutu pobranego ze szprychy rowerowej. Oś tę mocujemy na klej. Do boków koła, z obu stron doklejamy po wałeczku z drewna. Wałeczek taki ma 10 milimetrów średnicy i 10 wysokości. One także mają być trwale przyklejone do szprychy.
Korby wału korbowego: są zrobione ze szprychy rowerowej, właśnie tej, do której przykleiliśmy nasze koło zamachowe. Korby, jedna o długości 20 milimetrów, a druga 10, wygniemy za pomocą imadła i młotka. Ten zestaw narzędzi sprawi, że kąty zagięć będą proste, a wygięcie powstanie w sposób kontrolowany tam, gdzie to przewidzieliśmy. Pracę tę będziemy mogli wykonać, gdy do podstawy modelu przykleimy klejem na gorąco suporty koła zamachowego. Koło ma się zmieścić pomiędzy nimi a szprychą, czyli wał ma być prostopadły do dłuższej krawędzi podstawy. Gdy koło jest umieszczone w szczelinach suportu, możemy wyznaczyć, w których miejscach należy formować korby. Widzimy to na fotografii.
Montaż modelu: Zaczniemy od sklejenia cylindra rozrządu z cylindrem pracy. Zadbajmy, żeby otwór w boku cylindra rozrządu trafiał dokładnie na dno cylindra pracy. Możemy te części po sklejeniu pomalować lakierem w sprayu. Koło zamachowe z jego wałem korbowym umieszczamy w suportach, zabezpieczając pokrywkami. Do podstawy przyklejamy suport cylindra. Do suportu przyklejamy klejem na gorąco cylinder i rozrząd. Oś cylindra ma trafiać na jedną z korb wału korbowego, tę dłuższą. Za pomocą korbowodu i suwaka łączymy te elementy, regulując długość korbowodu. Pozostaje nam do zamontowania mechanizm rozrządu. Tłoczek rozrządu ustawiamy w jego cylindrze, w pozycji zamykającej otwór wlotowy. Trójkąt ustawiamy w pozycji neutralnej i za pomocą gwoździa z dużym łepkiem mocujemy go do suportu. Pozostaje połączyć drugim korbowodem trójkąt z korbą po przeciwnej stronie koła zamachowego. Przyjrzyjmy się rysunkowi ze schematem działania naszego modelu, a wszystko stanie się jasne. Na koniec doklejamy do cylinderka rozrządu fragment nakrętki od tubki. Od tej strony będzie dostarczane sprężone powietrze. Pozostaje podłączyć do naszej maszyny warsztatową sprężarkę i można się cieszyć działaniem najnowszego dzieła.
Adam Łowicki
Zobacz także:
Lekki mobil
Druciany mobil
Mobil dwucylindrowiec