Kurs projektowania 3D w 360. Prototypy modeli - lekcja 6
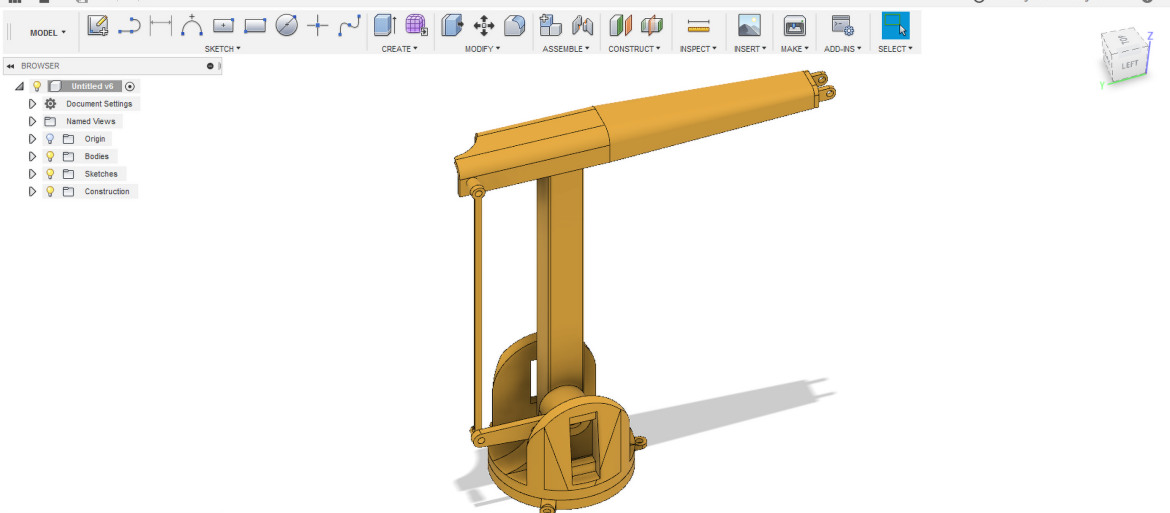
Jak zwykle zaczniemy od czegoś prostego, czyli podstawy, na której osadzimy ramię.
Podstawa
Rozpoczynamy od szkicu okręgu na płaszczyźnie XY. Okrąg o średnicy 60 mm, ze środkiem w początku układu współrzędnych, wyciągnięty w górę na wysokość 5 mm, utworzy pierwszą część podstawy. W stworzonym walcu warto wyciąć kanał na kuli i dzięki temu stworzyć wewnątrz podstawy łożysko kulkowe (1). W opisanym przypadku użyte kule będą miały średnicę 6 mm. Do stworzenia tego kanału potrzebny będzie szkic okręgu o średnicy 50 mm, o środku w początku układu współrzędnych, narysowany na powierzchni walca. Dodatkowo potrzebny będzie szkic na okręgu (w płaszczyźnie YZ), o średnicy odpowiadającej średnicy kulek. Okrąg musi być oddalony o 25 mm od środka układu współrzędnych i mieć środek na powierzchni walca. Używając operacji Sweep z zakładki CREATE, wycinamy tunel na kulki. Następny krok to wycięcie otworu w osi obrotu podstawy. Średnica otworu wynosi 8 mm.
Czas na górną część podstawy (2). Rozpoczynamy od skopiowania dolnej części za pomocą operacji Mirror z zakładki CREATE. Przestawiamy pierwszy parametr na Bodies i wybieramy obiekt od odbicia, czyli dolną część. Pozostaje wybrać płaszczyznę lustra, którą będzie górna powierzchnia dolnej części. Po zatwierdzeniu powstaje niezależna górna część, do której dodamy następne elementy. Rozpoczynamy szkic na górnej powierzchni i rysujemy dwie linie - jedną oddaloną o 25 mm, drugą o 20 mm. Powstanie z tego ścianka o grubości 5 mm. Rysunek powtarzamy symetrycznie, po drugiej stronie podstawy. Metoda dowolna, czyli ręcznie lub lustrem. Wyciągamy powstały szkic na wysokość 40 mm, upewniając się, że doklejamy, a nie tworzymy nowy obiekt. Następnie, na jednej z powstałych ścianek, szkicujemy kształt, którym zaokrąglimy ścianki. Przycinamy obydwie ścianki. Warto dorobić ładne przejście z płaskiej ścianki do podstawy. Pomoże w tym operacja Loft z zakładki CREATE. Mając już wybraną tę opcję, zaznaczamy powierzchnię ściany oraz fragment podstawy, do którego chcemy wyrównać. Po zatwierdzeniu powtarzamy to dla drugiej ścianki (3).
W podstawie brakuje już tylko miejsca, w którym zamontujemy serwomechanizmy do poruszania ramieniem. W tym celu wytniemy specjalne łoże w stworzonych ściankach. Na środku jednej z powstałych ścianek szkicujemy prostokąt odpowiadający wymiarom planowanego serwomechanizmu. W tym wypadku będzie to 12 mm szerokości i 23 mm wysokości. Prostokąt musi być ustawiony w środku podstawy, ponieważ ruch serwomechanizmu będzie przekazany na ramię. Wycinamy prostokąt przez całą podstawę. Pozostaje przygotować wcięcia, dzięki którym zamontujemy serwomechanizmy (4). Dorysowujemy prostokąty o wymiarach 5×12 mm na dole i na górze otworów. Wycinamy w jednej ściance otwory, ale z parametrem Start ustawionym na Offset Plane i wartością -4 mm. Takie wycięcie wystarczy skopiować przy pomocy lustra, wybierając odpowiednie płaszczyzny, które zostaną odbite. Wycięcie otworów pod śruby do zamontowania serwomechanizmów nie powinno być już problemem.
Pierwsze ramię
Na podstawie rozpoczynamy szkic i rysujemy profil ramienia - niech będzie to ceownik (5). Grubość ścianek ramienia nie musi być duża - wystarczą 2 mm. Wyciągamy stworzony profil w górę, z odsunięciem od powierzchni szkicu. Podczas wyciągania zmieniamy parametr Start na Offset Plane i ustawiamy wartość odsunięcia na 5 mm. Wyciągamy na wysokość 150 mm. Końcówkę ramienia warto zaokrąglić (6), aby druga część lepiej się poruszała. Wykonać to można przy pomocy prostego cięcia. Czas dokończyć dół ramienia. Warto dodać wypełnienie dolnej części prostym szkicem i wyciągnięciem.
Następny krok to wycięcie otworu, w który wprowadzimy orczyk serwomechanizmu. Tu, niestety, pojawia się drobny problem, ponieważ serwomechanizmy nieco się różnią i trudno podać jeden wymiar, który będzie zawsze pasował. Otwór należy zwymiarować i wyciąć w zależności od planowanego serwomechanizmu. Pozostaje zaokrąglić krawędzie według uznania oraz wyciąć otwór u góry ramienia, aby przygotować miejsce na oś obrotu drugiej części. W tym przypadku otwór ma średnicę 3 mm.
Drugie ramię
Pracę nad drugim ramieniem rozpoczynamy od zrobienia dźwigni, którą poruszany będzie drugi element (7). Zaczynamy szkic na płaskiej płaszczyźnie drugiej części podstawy i rysujemy okrąg o średnicy 15 mm i środku w miejscu osi obrotu serwomechanizmu. Dodajemy ramię, dzięki któremu poruszymy górną część. Ramię dźwigni powinno mieć 40 mm długości. Szkic wyciągamy z ustawionym parametrem Start na Offset Plane, z wartością odsunięcia równą 5 mm. Na końcu dźwigni pozostaje wyciąć otwór, w którym zamontujemy popychacz do poruszania górnej części (8).
Następny krok to wspomniany popychacz (11). Rozpoczynamy szkic na płaszczyźnie XY i rysujemy profil popychacza. Wyciągamy naszkicowany profil w górę na 125 mm, z parametrem Start ustawionym na From Object oraz parametrem Offset ustawionym na 1 mm. Ten element powinien być stworzony z parametrem Operation ustawionym na New Body. Następnie wybieramy operacją Extrude i zaznaczamy dolną ścianę popychacza. Pozwoli to na dobranie długości do dźwigni.
Na końcach popychacza brakuje jeszcze zaczepów, którymi będzie można połączyć dźwignię z drugą częścią ramienia. Szkic rozpoczynamy na płaszczyźnie dźwigni. Okrąg o średnicy odpowiadającej końcowemu zaokrągleniu dźwigni wyciągamy tak, aby zlało się z popychaczem. Okrąg powinien być odsunięty od powierzchni szkicu, w przeciwnym razie ten element połączy dźwignię z popychaczem w jeden element, a to utrudni wydruk. To samo powtarzamy na drugim końcu popychacza. Na koniec wycinamy otwory pod śruby, którymi będzie można połączyć elementy.
Drugi element ramienia rozpoczynamy od szkicu na grzbietowej ścianie pierwszej części ramienia (9, 10). Rysujemy profil ramienia w formie ceownika obejmującego pierwszy element ramienia. Po narysowaniu pierwszego kształtu profilu przy pomocy funkcji Offset z zakładki SKETCH odsuwamy pierwszy kształt o 2 mm. Zamykamy szkic dwoma krótkimi liniami. Tak przygotowany profil wyciągamy na odległość 25 mm z parametrem Direction ustawionym na Symmetric.
Stworzony element jest bazą do dalszego jego rozwoju. Na tylnej płaszczyźnie rozpoczynamy szkic. Przy pomocy funkcji Offset powielamy kształt profilu - kluczem w tym zabiegu jest ustawienie parametru odsunięcia na 0 mm. Mając powielony kształt, przycinamy go na środku dorysowując linię. Wyciągamy jedną z połówek profilu (tę bliżej popychacza) na odległość 15 mm. Powstały element warto zaokrąglić.
Następny krok to druga strona tej części ramienia. Przy pomocy operacji Offset Plane tworzymy płaszczyznę odsuniętą o 90 mm od powierzchni bazowej części ramienia. Na powstałej płaszczyźnie powstanie szkic profilu ramienia, ale pomniejszony. W tym szkicu najważniejsze, aby dolne części znajdowały się na tej samej wysokości co dolna część profilu. Po zamknięciu szkicu tworzymy resztę ramienia poprzez wyciągnięcie po profilach. Kryje się to pod operacją Loft, która już nie raz się pojawiała w tym kursie.
Wzmocnienia
Ramię w takiej formie wymaga jeszcze kilku wzmocnień (13). Między ramieniem a dźwignią jest sporo wolnego miejsca. Można je wykorzystać na dodanie podpory, która wzmocni ramię i przeniesie siły z serwomechanizmów na podstawę.
Szkic rozpoczynamy na górnej płaszczyźnie podstawy i rysujemy prostokąt w wolnej przestrzeni. Prostokąt powinien być trochę odsunięty od ramienia i dźwigni, aby nie połączyło się to w jedną bryłę. Tworzone wzmocnienie należy dołączyć do podstawy. Szkic wyciągamy na wysokość 31 mm i zaokrąglamy górne krawędzie oraz dolne, wedle uznania. Pozostaje wyciąć otwór w osi obrotu o średnicy 3 mm.
Do podstawy warto dodać elementy, którymi przymocujemy ramię do podłoża (14). Rozpoczynamy szkic na dolnej płaszczyźnie podstawy i rysujemy prostokąt o wymiarach 10×15 mm. Wyciągamy go w górę na wysokość 2 mm i zaokrąglamy krawędzie. Następnie zaokrąglamy krawędź pomiędzy stworzonym prostokątem a podstawą ramienia. Wycinamy otwór na śrubę. Takie elementy, pozwalające na zamontowanie, powinny być co najmniej trzy - przy pomocy operacji szyku kołowego powielamy zatem stworzony element trzykrotnie (15).
Do pełnego ramienia brakuje już tylko chwytaka, bądź innego końcowego narzędzia. Naszą lekcję zakończymy jednak na konsoli, do której będzie można zamontować własne narzędzie (12). Na końcowej ścianie ramienia rozpoczynamy szkic, odbijamy kształt ściany i domykamy prostą linią. Wyciągamy na odległość 2 mm. Następnie szkicujemy na powstałej ścianie prostokąty o wymiarach 2×6 mm. Powinny być oddalone od siebie o 7 mm oraz ustawione symetrycznie względem środka. Taki szkic wyciągamy na odległość 8 mm i zaokrąglamy. W powstałych elementach wycinamy otwory, dzięki którym zamontujemy dodatkowe narzędzie.
Podsumowanie
W sześciu lekcjach naszego kursu zostały omówione i zaprezentowane podstawy programu Autodesk Fusion 360 - funkcje, które pozwalają na stworzenie prostych i średniozaawansowanych modeli 3D: ozdób, elementów technicznych oraz prototypów własnych konstrukcji. Jest to dobra ścieżka do kreowania nowych możliwości, może nawet podejmowania nowego hobby, bo przecież przy aktualnym rozwoju technologii druku 3D umiejętność zaprojektowania własnego modelu staje się bardzo przydatna. Pozostaje teraz doskonalić nowo poznane sposoby i projektować z użyciem omówionych funkcji.
Bartłomiej Jakobsche
Zobacz także:
Kurs projektowania 3D w 360. Czyli jak w pełnym zakresie pracować z nowymi technologiami - lekcja 1
Kurs projektowania 3D w 360. Bryły walcowe - lekcja 2
Kurs projektowania 3D w 360. Bryły kuliste - lekcja 3
Kurs projektowania 3D w 360. Bryły złożone - elementy konstrukcyjne robotów - lekcja 4
Kurs projektowania 3D w 360. Proste mechanizmy na raz! - lekcja 5