Części zamienne
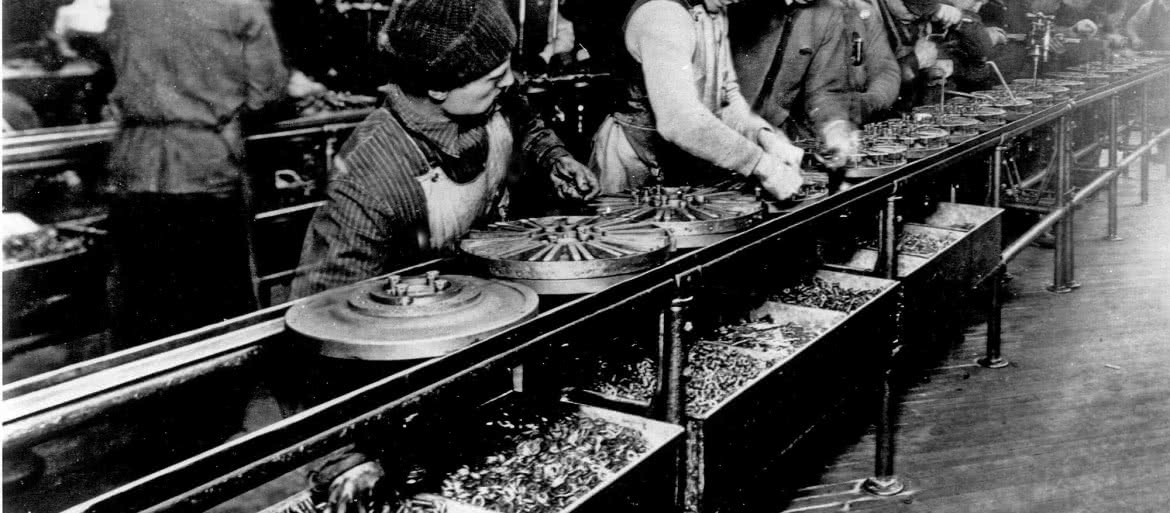
Trzecie tysiąclecie p.n.e. Przy wznoszeniu piramid w Egipcie stosowano stałe wymiary elementów budowlanych.
III w. p.n.e. W czasie pierwszej wojny punickiej (lata 264-241) Kartagińczycy wykorzystywali ustandaryzowane części wymienne. Były one nawet dostarczane z instrukcją montażu.
Ok. 1450 W weneckim Arsenale przygotowuje się "znormalizowane" drewniane części statków, w tym np. ławy. Są wytwarzane według jednego wzoru, dzięki czemu można je montować w sposób wymienny, z niewielkimi modyfikacjami.
1720 Według historycznych przekazów, szwedzki wynalazca Christopher Polhem stosuje w swoim warsztacie zegarmistrzowskim części wymienne. Innowacja ta nie wykroczyła jednak poza próg jego pracowni.
1773 Guillaume Deschamps produkuje wymienne zamki do muszkietów. Były one jednak horrendalnie drogie - za jeden zamienny zamek można było kupić siedem tradycyjnych, wytwarzanych techniką dorabiania. To podważało cały sens pomysłu, dlatego Francuz nie odniósł sukcesu.
1780 Francuski generał porucznik Jean-Baptiste Gribeauval konsekwentnie standaryzuje artylerię. Tworzy szereg ściśle zdefiniowanych klas armat (1) i sprawia, że amunicja jest w nich dopuszczana do użytku po przejściu przez znormalizowane wzorniki. Działania te, mające u podłoża raczej zamiłowanie do porządku, przyniosły nie do końca zamierzony, ale całkiem pozytywny efekt uboczny - w określonych klasach artylerii drewniane części dział stały się w pełni zamienne.
1785 Honoré Blanc demonstruje na dziedzińcu zamku Vincennes system wymiennych, złożonych części mechanicznych - demontuje zamki muszkietów, miesza części i składa wszystko ponownie. Niestety, nie miał szans na rozwój swoich pomysłów, gdyż wkrótce wybuchła rewolucja francuska i duża część potencjalnie zainteresowanych jego wynalazkiem odbiorców została stracona na szafocie, albo uciekła.
Istnieją jednak świadectwa na to, że warsztat Blanca odwiedził sam Thomas Jefferson - ówczesny amerykański ambasador Francji, a późniejszy prezydent USA. Będąc pod wrażeniem zaobserwowanych metod, miał nawet zawieźć pomysł i próbki produktów za ocean, promując tam ideę części zamiennych. Faktem jest, że pierwsza masowa produkcja zamiennych części do broni miała miejsce w formującej się armii nowo powstałych Stanów Zjednoczonych Ameryki.
1797-1801 Jako pionier produkcji części zamiennych i masowej produkcji przemysłowej wymieniany jest często Amerykanin Eli Whitney (2). Zademonstrował on swoją koncepcję części zamiennych do broni prezydentowi Johnowi Adamsowi i wiceprezydentowi Thomasowi Jeffersonowi.
W połowie 1798 r. otrzymał kontrakt, zgodnie z którym zobowiązał się do dostarczenia rządowi USA do 1801 r. 10 tys. sztuk broni. W tamtym czasie karabiny zazwyczaj wciąż były montowane w całości przez rzemieślników, a każdy model miał swój odrębny projekt.
Whitney wynalazł maszyny, które umożliwiały robotnikom wycinanie metalu według wzoru i produkcję jednego konkretnego, specyficznego elementu. Po złożeniu każda część, choć wykonana oddzielnie, stawała się modelem roboczym.
Po pierwszych kilku latach produkcji Whitney był w stanie dostarczyć tylko część obiecanego zamówienia - zakończenie produkcji 10 tys. sztuk zajęło mu dziesięć lat. Mimo to podpisał kolejną rządową umowę, na 15 tys. karabinów, które tym razem wytworzył w ciągu zaledwie dwóch lat.
Dziś jest uważany za pioniera "amerykańskiego systemu", czyli masowej produkcji ustandaryzowanych części, które można składać w gotowe produkty. Do lat 70. XIX wieku system amerykański był wykorzystywany do wytwarzania ręcznej broni strzeleckiej, zegarów, maszyn włókienniczych, maszyn do szycia i wielu innych wyrobów przemysłowych.
1800 Henry Maudslay konstruuje pierwszą przemysłową praktyczną maszynę do gwintowania (3). Pozwoliło to na standaryzację wymiarów gwintów śrubowych i utorowało drogę do wymienności nakrętek i śrub. Wcześniej gwinty wykonywano z użyciem dłuta i pilników.
Maudslay znormalizował stosowane w jego warsztacie gwinty i wyprodukował zestawy szablonów do gwintów, dzięki którym nakrętki i śruby były zgodne z normami, a każda śruba o określonym w "normie" rozmiarze pasowała do nakrętek tego samego rozmiaru. Był to znaczący postęp w technologii warsztatowej i zamienności części technicznych.
1802-1808 Francuski inżynier Marc Brunel, pracując dla brytyjskiej admiralicji w Portsmouth, opracował proces maszynowej produkcji znormalizowanych drewnianych krążków i bębnów do montażu lin okrętowych (4). Brytyjscy producenci zignorowali jednak jego pomysły.
Dopiero na londyńskiej słynnej Wystawie Crystal Palace w 1851 r. tamtejsi inżynierowie - oglądając przykłady rozwiązań używanych w Stanach Zjednoczonych do produkcji części zamiennych na jednostkach pływających - zaczęli stosować system, który pięćdziesiąt lat wcześniej wynalazł w ich własnym kraju Brunel.
1814 Linię produkcyjną w Plymouth w stanie Connecticut opuszcza zegar konstrukcji Eliego Terry’ego, wykonany z drewnianych ustandaryzowanych elementów. W ten sposób rusza pierwsza amerykańska produkcja masowa z użyciem drewnianych części zamiennych.
1824 John Hancock Hall organizował w amerykańskim mieście Harpers Ferry warsztaty produkcji broni. Dążył w nich do wprowadzenia systemu części zamiennych na jak największą skalę. Zdał sobie sprawę, że najważniejsza dla wymienności elementów jest ich precyzja. Jej zakres niezbędny do wykonania konwencjonalnego elementu zamka do broni wynosił ±0,2 mm, ale do zamienności potrzebne było już zmieszczenie się w przedziale ±0,02 mm.
Hall skupił się na wielokrotnych pomiarach. Opracował nowe techniki pomiarowe i stworzył wytrzymalsze maszyny, ze zredukowanymi wibracjami. Udoskonalił również techniki obróbki metali. Osiągnął to, że w 1824 r. części zamków produkowanych w jego warsztatach były już w pełni wymienne.
1834-1843 Kolejnym krokiem stała się wymienność części pomiędzy różnymi wytwórcami. Udało się to osiągnąć, gdy współpracę z Hallem nawiązał rusznikarz Simeon North. Owocem tej współpracy i ustandaryzowania części zamiennych okazał się znany model karabinu Hall-North wzór 1843 (5). Był używany podczas wojny amerykańsko-meksykańskiej (1846-1848) oraz wojny secesyjnej (1861-1865).
1841 Joseph Whitworth tworzy pierwszą (nieoficjalną) normę techniczną, która zaczęła służyć do określania w różnych krajach rozmiarów gwintów. Znana była pod nazwą British Standard Whitworth i została przyjęta w wielu miejscach na świecie. Jak każdy postęp w normalizacji wspierała również zasadę zamienności części.
druga połowa XIX w. W czasie wojny secesyjnej w USA amerykańska broń była już w pełni wykonana z części wymiennych, podobnie jak broń francuska i angielska. Tego rodzaju elementy zaczęły się pojawiać także w wielu innych produktach ówczesnego przemysłu, np. w maszynach do pisania i do szycia, rowerach, a w końcu w samochodach. Nie zawsze przychodziło to bez oporów.
Przykładowo, wytwarzająca maszyny do szycia firma Singer nie wprowadziła wymienności części aż do ok. 1900 r. - do tego czasu nie była też wymienialna większość części samochodowych.
1907 Trzy samochody Cadillaca Model K (6) zostały przetestowane na torze wyścigowym, po czym całkowicie zdemontowane. Wiele części o wysokiej precyzji zostało następnie wymieszanych i ponownie zmontowano z nich trzy pojazdy. "Nowe' auta nie tylko pomyślnie przeszły kolejne próby, ale jedno z nich wygrało nawet test niezawodności na dystansie 3 tys. km. To, co dziś wydaje się czymś zupełnie naturalnym, w 1907 r. stanowiło niezwykłe osiągnięcie.
1913 Henry Ford połączył koncepcję części zamiennych Whitneya z wymogiem ciągłej ich dostępności i dostarczania na linię montażową (7). Wytwarzany zgodnie z tą ideą model Forda T zmienił oblicze motoryzacji.
Opracowując procesy montażowe w swojej fabryce, Ford czerpał inspirację z dziewiętnastowiecznych zakładów pakowania mięsa w Cincinnati, Ohio i Chicago. Stosowano tam specjalne wózki do transportu tusz między pracownikami - połączone łańcuchami umożliwiały taśmowy rozbiór mięsa, tworząc pierwowzór fordowskiej linii montażowej, przy której robotnicy wykonywali powtarzalne czynności, korzystając ze standardowych części.
1926-1947 W roku 1926 powstała Międzynarodowa Federacja Krajowych Stowarzyszeń Normalizacyjnych (ISA). Jej misją było poszerzenie współpracy państw w zakresie wszystkich norm i specyfikacji technicznych. Działała do roku 1942, kiedy to została zawieszona.
Po II wojnie światowej utworzono Komitet Koordynacyjny ds. Standardów Narodów Zjednoczonych (UNSCC), który wystąpił z propozycją powołania nowego globalnego organu normalizacyjnego. W październiku 1946 r. w Londynie spotkali się delegaci ISA i UNSCC z dwudziestu pięciu krajów, którzy zgodzili się połączyć siły w Międzynarodowej Organizacji Normalizacyjnej (ISO). Nowy podmiot oficjalnie rozpoczął działalność w lutym 1947 r.
1945-1962 Kiichirō Toyoda, syn założyciela firmy Toyota, stawia przed swoją firmą wyzwanie "pościgu za Ameryką". Było jednak jasne, że nie da się tego zrealizować, przyjmując amerykański model masowej produkcji. Potrzebny był nowy pomysł - produkcja masowa oznaczała bowiem konieczność wykonania tysięcy identycznych części w celu uzyskania ekonomii skali, ale brakowało materiałów, zamówienia były duże, a zapotrzebowanie na różnorodność rosła.
Zgodnie z wizją Toyody, wszystkie części przeznaczone do montażu powinny trafiać na linię montażową dokładnie w momencie, gdy są potrzebne do montażu (just-in-time). Należy więc je wykonywać tuż przed ich użyciem. Realizacja tego pomysłu wymagała czasu - udało się to dopiero w 1962 r., dekadę po śmierci Toyody.
Śmiałą koncepcje wprowadzał w życie Taiichi Ohno (8), kierownik fabryki maszyn, wykorzystując również wnioski wynikające ze studiowania systemu produkcji Forda oraz metod inwentaryzacji stosowanych przez amerykańskie supermarkety. Dodał do tego wiedzę i doświadczenia z branży włókienniczej oraz spostrzeżenia kierowanych przez siebie pracowników.
W swojej książce "Toyota Production System" Ohno nazywa tzw. system Toyoty "systemem całkowitej eliminacji odpadów". Wyjaśnia, że opiera się on na dwóch filarach: przepływie just-in-time oraz autonomizacji (tzw. jidoka), umożliwiającej samodzielną pracę maszyn pod jedynie ogólnym nadzorem człowieka.
Lata 80. Pojawiają się pierwsze drukarki 3D. Początkowo służyły wyłącznie do zabawy. Potem do tworzenia prototypów. Obecnie są już całkiem regularnie wykorzystywane do produkcji części zamiennych. Szczególnie obiecujący w tej mierze wydaje się rozwój technik addytywnych z metalu.
Chociaż pomysł na druk 3D z metalu i niektóre związane z tym patenty pochodzą jeszcze z lat 70. i 80. XX wieku, pierwszą firmą, która stworzyła urządzenie do druku 3D z tego materiału był Electro Optical Systems (EOS), założony w 1989 r. W 1994 r. udostępniono na rynku jego system EOSINT M 250 (9).
Lata 90. Powstaje koncepcja tzw. inteligentnych materiałów (smart materials), do których zalicza się materiały samonaprawiające się. Reagują one na uszkodzenie strukturalne, czyli np. pęknięcia, ubytki czy wygięcia.
W dzisiejszych czasach istnieje kilka mechanizmów samonaprawiania. Związane są one głównie z pamięcią kształtu i technologiami samogrupowania się cząsteczek. Materiały smart mogą znaleźć zastosowanie w licznych dziedzinach, otwierając drogę do nowych standardów w inżynierii i w projektowaniu aplikacji dla przemysłu oraz dla zwykłych użytkowników. Ich upowszechnienie w przemyśle ma też szansę zrewolucjonizować sektor części zamiennych, eliminując docelowo konieczność stosowania takich części w ramach napraw urządzeń.
2014 Na Międzynarodowej Stacji Kosmicznej (ISS) powstaje pierwszy wydruk za pomocą drukarki 3D, firmy Made in Space - jest nim tabliczka z napisem "Made in Space" oraz skrótem "NASA". Drukarka docelowo ma zająć się wytwarzaniem części zamiennych potrzebnych na pokładzie (10). Według informacji producenta, wykorzystywać może do tego celu nie tylko polimery, ale też metale, kompozyty i inne materiały.
Klasyfikacja części maszyn
Części maszyn to wchodzące w skład maszyn elementy samodzielne lub zespoły, zwykle o charakterze uniwersalnym (czyli dające się wykorzystywać w różnych urządzeniach) - co pozwala na ich znormalizowanie. Podstawowa klasyfikacja części prowadzona jest według kilku głównych kryteriów i obejmuje:
- Połączenia (mechaniczne)
a. Nierozłączne:
• nitowe,
• spawane,
• zgrzewane,
• lutowane,
• klejone,
• skurczowe;
b. Rozłączne:
• kształtowe:
–– wpustowe,
–– wypustowe,
–– wieloboczne;
• sworzniowe,
• kołkowe,
• gwintowe,
• sprężyste,
• rurowe. - Łożyska
• ślizgowe,
• toczne. - Sprzęgła
a. Nierozłączne:
• przymusowe,
• luźne,
• podatne,
• kątowe;
b. Rozłączne:
• sterowane,
• samoczynne. - Hamulce
- Napędy
- Przekładnie
• cierne,
• pasowe,
• łańcuchowe,
• zębate.
Normalizacja części maszyn
Normalizacja polega na ujednoliceniu oraz uproszczeniu nazewnictwa i pojęć, a także ustaleniu kształtów, wymiarów, materiału i dokładności wykonania, co gwarantuje właściwą jakość części oraz ułatwia konstrukcję i naprawę maszyn.
Dzięki skróceniu czasu przygotowania i uruchomienia produkcji oraz zmniejszeniu liczby potrzebnych obrabiarek i przyrządów pomiarowych normalizacja usprawnia produkcję maszyn, którą prowadzą fabryki i zakłady rozrzucone po całym kraju, ułatwia konstruktorom opracowywanie nowych maszyn, obniża koszty produkcji, a ponadto w dużym stopniu przyspiesza prace montażowe.
Użytkownikom końcowym normalizacja ułatwia nabycie gotowych części w różnych branżowych składnicach, a także wymianę zużytych lub uszkodzonych części na nowe, bez potrzeby ich dorabiania i dopasowywania. Uszkodzony element można też łatwo zidentyfikować za pomocą katalogu, wiedząc z którego zespołu lub podzespołu maszyny został wymontowany.
Znormalizowane nazewnictwo ułatwia też porozumiewanie się producentów i użytkowników. Polskie Normy (oznaczone symbolem PN) zatwierdzone są przez polski Komitet Normalizacyjny (PKN). Współpracuje on z podobnymi instytucjami w innych krajach oraz organizacjami zajmującymi się normalizacją w skali międzynarodowej, np. ISO (International Standard Organization). Dlatego oprócz norm krajowych istnieją również międzynarodowe normy i zalecenia normalizacyjne.
Mirosław Usidus