Stopy metali
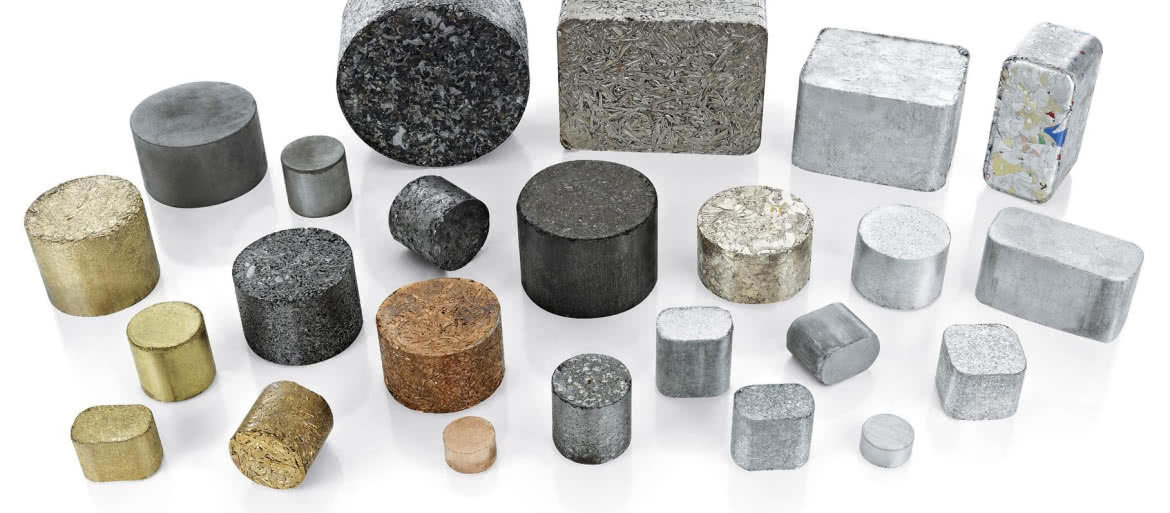
4500–3150 p.n.e. Na Bliskim Wschodzie zaczyna się na szeroką skalę obróbka miedzi i stopy miedzi z arsenem. Stopy miedzi z tym metalem były stosowane jeszcze długo w czasie epoki brązu.
3500 p.n.e. Pierwszy znany przypadek użycia brązu, który miał miejsce w starożytnym Sumerze (1). Był to początek tak zwanej epoki brązu. Produkcja stopów przynosiła dwie korzyści: wzmacniała metal w procesie zwanym utwardzaniem roztworowym oraz ułatwiała odlewanie, ponieważ stopy miały niższą temperaturę topnienia. Z brązu odlany był Kolos Rodyjski, olbrzymich rozmiarów posąg Heliosa wybudowany na wyspie Rodos przez Charesa z Lindos w latach 292-280 p.n.e., jeden z siedmiu cudów świata. Posąg miał ok. 32-36 m wysokości i ważył ok. 70 ton. Starożytne cywilizacje brały pod uwagę różne właściwości, które miały mieszaniny metali w różnych proporcjach, takie jak twardość, wytrzymałość i temperaturę topnienia. Na przykład, groty strzał z czasów chińskiej dynastii Qin (około 200 lat p.n.e.) były często budowane z grotem z twardej odmiany brązu, w innych częściach miały bardziej miękki brąz-tang, który zapobiegał pęknięciom podczas użytkowania.
3000-200 p.n.e. W Eshnunna w Iraku znaleziono fragment klingi żelaznej pochodzącej z I połowy III tysiąclecia p.n.e. Uznano ją za pierwszy ślad metalurgii żelaza. Około 1400 roku p.n.e. Hetyci w Anatolii wprowadzają metodę produkcji względnie dużych ilości wytopionego żelaza. Ok. 800 r. p.n.e. technologia produkcji żelaza rozpowszechniła się w Europie. Coś zbliżonego do współczesnego żeliwa, bardzo twardy, ale kruchy stop żelaza i węgla, był produkowany w Chinach już w 1200 r. p.n.e. W VII w. p.n.e. stosowano tam pionowe piece do wytopu. Dla rozwoju odlewnictwa w Chinach bardzo istotne było występowanie na tych terenach odpowiedniej gliny, która pozwalała na konstrukcję pieców hutniczych. Chińczycy odkryli też, iż dodanie "czarnej ziemi" (zawierającej fosfor) powoduje obniżenie temperatury, w której metal staje się płynny). W III w. p.n.e. pojawiła się tam obróbka cieplna stopów żelaznych. Prawdopodobnie już wtedy Chińczycy zastosowali techniki podobne do procesu Bessemera, który został opracowany w Europie dopiero w XIX wieku.
2000-500 p.n.e. W starożytnym Egipcie i Mykenach złoto było często łączone stopowo z miedzią do produkcji czerwonego złota (2) lub z żelazem do produkcji jaśniejszego złota różowego. Złoto często było topione ze srebrem lub innymi metalami do produkcji różnego rodzaju kolorowego złota.
Metale te były również wykorzystywane do wzajemnego wzmacniania się, dla bardziej praktycznych celów. Miedź była często dodawana do srebra w celu uzyskania srebra szterlingowego, zwiększając jego wytrzymałość do stosowania w naczyniach, sztućcach i innych praktycznych przedmiotach. W VII w. p.n.e. wybijano monety z elektrum, stopu złota i srebra, zaś dwieście lat później pojawiły się monety z brązu - stopu miedzi i cyny. Dość często metale szlachetne były stapiane w monetach i przedmiotach jubilerskich z mniej cennymi substancjami przez fałszerzy, co z czasem stało się prawdziwą zmorą.
VI-IV wiek p.n.e. W starożytnych Indiach rozwija się wysoko zaawansowana metalurgia. Narodziła się wówczas m.in. stal "wootz". Rzemieślnicy z południowych Indii używali tygli do wytapiania kutego żelaza z węglem drzewnym. Charakterystyczne widoczne w jej strukturze pasma (3) są tworzone przez warstwy węglików w osnowie z odpuszczonego martenzytu lub perlitu w stali wysokowęglowej lub przez opaski ferrytowe i perlityczne w stalach o niższej zawartości węgla. Z V w. p.n.e. pochodzi tzw. Żelazna Kolumna z Delhi (4) z kutego żelaza o znakomitej jakości z dużą zawartością fosforu i niewielką siarki, dzięki czemu nie ulega korozji.
IV-I w. p.n.e. Mosiądz po raz pierwszy pojawił się w czasach rzymskich. Podobno jako pierwsi wytwarzali mosiądz Mossyni, jeden z ludów w Azji Mniejszej, którzy stapiali miedź z mieszaniną węglanu cynku i krzemianu cynku - rudy nazywanej dzisiaj galmanem. W późniejszych czasach mosiądz wytwarzano, stapiając miedź z tlenkami cynku, osadzającymi się w postaci białego nalotu wewnątrz pieców służących do wytapiania miedzi.
200 p.n.e. Rtęć, wytapiana w starożytności z cynobru, rozpuszcza wiele metali, w tym złoto, srebro i cynę, dzięki czemu powstają amalgamaty (stopy w temperaturze otoczenia w postaci miękkiej pasty lub cieczy). Amalgamaty są używane od II w. p.n.e. w Chinach do złocenia zbroi i luster metalami szlachetnymi. Starożytni Rzymianie często używali amalgamatów rtęciowo-cynowych do ozdabiania swoich zbroi. Amalgamat był stosowany jako pasta, a następnie podgrzewany aż do odparowania rtęci, pozostawiając złoto, srebro lub cynę. Obecnie najbardziej znanym polem wykorzystania amalgamatów jest stomatologia (5).
XI wiek n.e. Na Bliskim Wschodzie opracowano stal damasceńską, wykorzystywaną głównie do produkcji ostrzy mieczy. Ostrza z Damaszku produkowano z wlewków stali "wootz", sprowadzanych z Indii. Do dziś nie odtworzono dokładnie techniki produkcji doskonałych ostrzy z tej stali.
XIV-XVII w. Pierwsze wielkie piece pojawiają się w czasach odrodzenia we Włoszech i w Austrii. W piecach otrzymywano ciekłą surówkę. Z surówki tej wykonywano odlewy żeliwne (głównie odważniki, kule i lufy armatnie). Stopniowo wprowadzano kolejne udoskonalenia, takie jak zastosowanie na początku XVIII w. przez Abrahama Darby’ego koksu do wytopu rudy żelaza na masową skalę, zamiast drewna i węgla drzewnego, co pozwalało wytwarzać stal lepszej jakości.
1828 Powstaje wielki piec hutniczy w nowoczesnej formie. Jego wynalazca, James Beaumont Neilson (6) zastosował żeliwne nagrzewnice powietrza, które były opalane węglem kamiennym. Powietrze po nagrzaniu było wdmuchiwane do wielkiego pieca hutniczego. Przyczyniło się to do znacznej poprawy efektywności wytopu żelaza.
1856 Henry Bessemer patentuje swoją metodę - tzw. gruszkę Bessemera (7), umożliwiająca tanie wytwarzanie jakościowej stali. W czasie swoich eksperymentów doszedł do wniosku, że nadmiar tlenu doprowadza do usunięcia węgla z surówki, która wcześniej została ogrzana, tak jak to dzieje się w procesie pudlowania. Zauważył też, że wdmuchiwanie powietrza w roztopione żeliwo nie tylko je oczyszcza, ale także doprowadza do wyższej temperatury, dzięki czemu może być ono "rozlewane" do odpowiednich form. Ten dodatkowy efekt polegający na rozgrzaniu żelaza jest wynikiem reakcji tlenu z węglem i krzemem w nim zawartym. Cały proces odbywał się w specjalnym konwertorze, do którego można było wlewać surówkę przed wdmuchaniem powietrza od spodu.
1862-1865 Pierre-Émile Martin, francuski inżynier, udoskonalił piec do wytopu stali konstrukcji Carla Siemensa, znany współcześnie jako piec Siemensa-Martina lub piec martenowski, hutniczy wannowy piec płomieniowy z odzyskiwaniem ciepła spalin. Opracował też nowe metody uszlachetniania stali. Został wprowadzony do użytku w 1865 r.
Lata 60-70. XIX w. Termin "stal stopowa" używany od XIX w. i później aż do dziś wynika z pewnego nieporozumienia historycznego. Aż do XIX w. nie zdawano sobie sprawy, że stal sama w sobie jest stopem żelaza i węgla. Pierwsza stal stopowa zawierała chrom i została opatentowana w 1865 r. przez amerykańskiego hutnika Juliusa Baura i wyprodukowana przez Chrome Steel Co. z Brooklynu, N.Y. Nie odniosła sukcesu, ale zainteresowała francuskiego hutnika Henri Ami Brustleina. Brustlein produkował i sprzedawał stal chromową na narzędzia, łuski armatnie i pancerze, zanim nadeszły najgłośniejsze odkrycia w tej dziedzinie.
1868 Pojawia się stal wolframowa, wynaleziona przez Roberta Musheta. Zauważył on, że przez dodanie wolframu do stali można uzyskać produkty niezwykle odporne na utratę twardości w wysokich temperaturach. "Stal specjalna R. Musheta" stała się pierwszą stalą szybkotnącą. W stalach narzędziowych wkrótce zastąpiono wolfram - węglikiem wolframu i dodano niewielkie ilości chromu oraz wanadu, dzięki czemu uzyskano doskonałą stal do użytku w narzędziach do obróbki.
1882 Robert Hadfield produkuje stop stali zawierający około 12 proc. manganu. Stop ten, nazywany mangalloyem lub stalą Hadfielda, wykazywał ekstremalną twardość i wytrzymałość, stając się pierwszym znanym szeroko stopem stali. Stosowany był m.in. do wyrobu gąsienic do czołgów, blach pancernych, kas ogniotrwałych.
1906 Niemiec Alfred Wilm odkrywa stopy hartowane metodą wydzieleniową. Pod kierunkiem Alfreda Wilma były prowadzone badania nad nowymi materiałami. Pracowano nad materiałem mającym zastąpić w produkcji łusek bardzo drogi mosiądz. Podczas badań stopu aluminium z miedzią jeden z laborantów pozostawił badaną płytkę i przez kilka dni nie pojawiał się w laboratorium. Po powrocie dokończył badania i uzyskał bardzo dobre wyniki. Kilka dni przerwy dało czas na zajście samoczynnego procesu starzenia naturalnego. Wynalazek poczyniono w miejscowości Düren w Niemczech, skąd pochodzi nazwa duraluminium (8), zaś według innych źródeł od łacińskiego słowa "durus" - twardy.
Chociaż wyjaśnienie tego zjawiska pojawiło się dopiero w 1919 roku, duraluminium stało się już wcześniej jednym z pierwszych zastosowanych stopów "utwardzanych starzeniowo", stając się podstawowym materiałem do budowy pierwszych zeppelinów, a wkrótce potem wielu innych. Ponieważ często wykazują one połączenie wysokiej wytrzymałości i małej wagi, stopy te stały się szeroko stosowane w wielu gałęziach przemysłu, w tym do budowy nowoczesnych samolotów.
1912-13 Huta Kruppa w Niemczech opracowuje stal odporną na rdzę, dodając 21 proc. chromu i 7 proc. niklu, dzięki czemu powstała pierwsza stal nierdzewna. Stal nierdzewna została opatentowana w 1912 r. przez niemieckich inżynierów Kruppa. Patent dotyczył stali austenitycznej (9). Nazwy "stal nierdzewna" jako pierwszy użył angielski inżynier Harry Brearley w 1913 roku - dla swojego wynalazku mieszanki żelaza, węgla oraz chromu. Anglikowi udało się przekonać do nowego wynalazku producenta noży R.F. Mosleya. Początkowo stal nierdzewna używana była tylko do wyrobu sztućców.
1955-70 Stopy do produkcji "części zamiennych" do człowieka, stopy kobaltu i tytanu z żelazem i innymi metalami, np. niklem. Przykładem tej generacji stopów jest stosowany w implantach kości i stentach np. w naczyniach krwionośnych - nitinol, zawierający 49 proc. niklu i 51 proc. tytanu, który po odkształceniu powraca do zapamiętanego kształtu.
1970-95 Wprowadzenie nadstopów, grupy materiałów na bazie żelaza, niklu i kobaltu, cechujących się wysoką żaroodpornością, wytrzymałością i odpornością na pełzanie w wysokich temperaturach, dobrą stabilnością powierzchniową i odpornością na korozję i utlenianie. Nadstopy mają zazwyczaj austenityczną strukturę krystaliczną.
Główną siłą napędową rozwoju nadstopów był i jest nadal przemysł lotniczy i energetyczny. Typowe zastosowanie to np. łopatki turbinowe do wysokotemperaturowych części silników odrzutowych i turbin gazowych. Przykładem nadstopów są hastelloy, inconel, np. IN100, IN600, IN713, waspaloy, rene alloys, np. rene 41, rene 80, rene 95, rene N5, haynes alloys, incoloy, MP98T, stopy TMS.
Nadstopy są powszechnie używane w tych częściach turbin gazowych, które są narażone na wysokie temperatury i gdzie wymagana jest wysoka wytrzymałość, doskonała wysokotemperaturowa odporność na pełzanie, zmęczenie, stabilność fazowa i odporność na korozję i utlenianie. Termin "nadstop" został po raz pierwszy użyty krótko po II wojnie światowej do określenia grupy stopów opracowanych do stosowania w turbosprężarkach i lotniczych silnikach turbinowych, choć już w latach 1910-15 opracowano austenityczne (faza γ) stale nierdzewne do wysokich temperatur w turbinach gazowych. Chociaż dawni hutnicy nie wiedzieli jeszcze o tym, tworzyli małe osady γ’ w nadstopach na bazie Ni. W latach 60. i 70. XX wieku hutnicy przesunęli punkt ciężkości z chemii stopów na przetwarzanie. Opracowano m.in. kierunkowe krzepnięcie, dzięki czemu uzyskano kolumnową ziarnistość lub monokrystaliczną łopatkę turbiny.
Klasyfikacja i niektóre interesujące rodzaje stopów
I. Podział stopów ze względu na główny składnik
- stopy aluminium
- stopy magnezu
- stopy miedzi
- stopy niklu
- stopy ołowiu
- stopy rtęci, amalgamaty
- stopy żelaza z węglem
- stal
- staliwo
- żeliwo - inne stopy
- inmet (stop oporowy miedzi i manganu z domieszką glinu i żelaza, wykorzystywany do wyrobu rezystorów pomiarowych)
- wironit (oparty głównie na kobalcie i chromie stop do protez szkieletowych)
II. Ciekawe stopy metali
Stop Devardy - stop metali, w którego skład wchodzi: miedź - 50%, glin - 45%, cynk - 5%. Stop opisał w 1894 r. włoski chemik Arturo Devarda (1859-1944) i od jego nazwiska pochodzi nazwa. Stop w postaci sproszkowanej jest stosowany w laboratoriach jako środek redukujący.
Nowe srebro (wg polskiej normy: mosiądz wysokoniklowy) - srebrzystobiały stop metali zawierający 40-70% miedzi, 10-20% niklu i 5-40% cynku. Gęstość 8,4-8,7 g/cm³. Nowe srebro wynaleziono w Chinach. Stało się znane w Europie po sprowadzeniu go przez spółki handlowe. Wbrew swojej nazwie zwyczajowej nie zawiera on srebra, jednak z wyglądu przypomina ten metal. Służy do wyrobu ozdób, sztućców, sprzętu medycznego, instrumentów muzycznych, rozmaitych przyborów itp., a także drutów oporowych.
Tombak, mosiądz czerwony - stop miedzi z cynkiem, zawierający powyżej 80% miedzi. Cechuje się żółtą barwą przypominającą złoto, jest jednak mało wartościowy, a w celu uniknięcia pomylenia go ze złotem na biżuterii z tombaku wybija się znak probierczy. Stosowany głównie jako imitacja złota do wyrobów artystycznych i jubilerskich oraz instrumentów muzycznych, a także na wężownice, rurki manometryczne i do platerowania. Jest też używany do produkcji pocisków i naboi pistoletowych i karabinowych w celu zmniejszenia tarcia między pociskiem a lufą w czasie wystrzału.
Galinstan - niskotopliwy stop eutektyczny galu, indu i cyny, płynny w temperaturze pokojowej, zestala się w temperaturze około -20°C. Dzięki temu, że jest mniej toksyczny, znajduje zastosowanie w termometrach zamiast rtęci lub stopu sodowo-potasowego.
Stop Newtona - niskotopliwy stop metali o składzie wagowym: bizmut 50%, ołów 31,2%, cyna 18,8%. Jego temperatura topnienia wynosi 96-97°C. Stoswany w dentystyce, modelarstwie, mechanice i odlewnictwie precyzyjnym. Jest bezpieczniejszą (nie zawiera kadmu) alternatywą dla stopu Lipowitza do wykonywania osłon przed promieniowaniem podczas radioterapii. Odkrywcą tego stopu jest Isaac Newton. Znany jest też inny niskotopliwy stop określany mianem stopu Newtona, który zawiera ołów, bizmut i kadm w stosunku wagowym 7:4:1 i topi się w temperaturze 95°C.